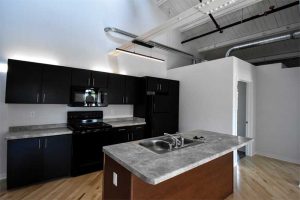
Adaptive reuse reimagines historic malted milk company
An aggressive construction schedule and a visionary developer known for unique adaptive reuse projects are driving the $100-million conversion of the 100-plus year-old historic Horlick Malted Milk Company factory complex—now named Belle City Square—into a mixed-use development that will include rental units, commercial, hotel, and dining spaces.
The $42.4 million Phase I construction began in August 2020 and includes the site’s two largest buildings. The southern building, ‘Arabella,’ named after William Horlick’s wife, began construction in August 2020 and was completed in May 2021, and includes 60 units that are a mix of 12 market-rate and 48 affordable apartments.
All of the apartments have the same finishes and range from studios to 93-m2 (1000-sf) three-bedroom units. While a variety of floor plans are repeated throughout the complex, each unit is unique through incorporating the building’s already-existing arched openings and other elements that were original to the historic facility.
The ‘Arabella’ is certified Wisconsin Green Built as part of the Wisconsin Environmental Initiative. The project meets the U.S. Green Building Council’s (USGBC’s) Leadership in Energy and Environmental Design (LEED) Gold requirements, however, at the time of writing, the developer was not seeking LEED certification. Fifty percent of the funding for this project is from state and federal historic tax credits.
The northern building, ‘The William,’ will achieve USGBC’s LEED Gold requirements and will house approximately 76 market-rate units. The ground floor opens to a large two-story area that will be constructed into two-floor apartments. The upper-level floors are so vast that an atrium is being constructed in the center to bring natural light into the hallways. These projects were made possible in part by State of Wisconsin and federal tax credit programs.
Challenges
Abandoned for the past 45 years, the factory complex fell into increasing states of disrepair. It was so damaged and deteriorated contractors had extremely limited access for walk throughs of the buildings when touring. The first months of work on the ‘Arabella’ was largely spent emptying the structure of detritus left by previous tenants, including everything from heavy machinery to garbage. After the buildings were cleared, which included removing trees growing in the buildings, the general contractor could see the poor conditions.

Flooring
The team demolished most of the tongue-and-groove floor system because over the years the roof leaked, and the floor rotted, causing huge holes and leaving only 25 percent walkable space. When possible, materials were salvaged and brought back to their original shape. For example, field analysis of the 2×6 tongue-and-groove wood deck subfloor was conducted to indicate where the rot ended, what could be salvaged from the original floor and where they needed to build back. Trade partners made seamless transitions, which included replacing the rotted maple with new 19 mm (0.75 in.) maple, matching the plank width and size, and running them the same 45-degree angle so it is virtually impossible to delineate the old floor from the newly constructed [floor].
Prior to the maple floor being installed, acoustic sound mats were glued onto the top side of each floor to dampen and absorb sound. Gypcrete, a lightweight concrete, was then added for fire rating and to further reduce sound.
Unlike the second, third, and fourth floors, the first floor kept the existing concrete floor that was more than the 2×6 tongue-and-groove deck. However, where this was rotted—just like with the wooden floors—the concrete was replaced or patched as needed. The existing concrete was also deep cleaned to remove 100 years of oil and dirt.