2.5 Temporary supports
Another important consideration in the design of field installed SSG is determining the configuration and attachment of temporary supports, often called ‘temporary stops,’ or ‘temps.’ Temporary supports are generally composed of small sections of metal pressure plates secured to the structural frame with a screw fastener or temporary toggle bolt that place the plate in contact with the glass through a silicone or neoprene gasket/pad.
The primary difference between the fastener attachment and toggle bolt attachment is the fastener must penetrate the frame to provide positive engagement, often resulting in a penetration through the system’s air/water line that must later be sealed and can reduce the system’s overall weather durability. A toggle bolt attachment, on the other hand, preserves the frame air/water line integrity and does not involve subsequent sealing steps; however, toggle bolts require the frame to have a toggle receptor included as part of the original framing system design (Figure 5).
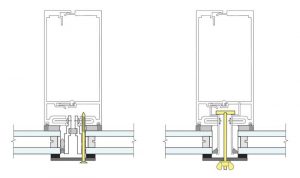
The design of the attachment of temporary supports should accommodate the components and cladding loads per the appropriate code (often the Aluminum Design Manual for glazed aluminum systems). Panels should have a minimum of one temporary stop per side (or horizontal pressure bar along a side with no temporary supports) to maintain deflection compatibility between the glass and frame and reduce stress on the sealant prior to cure. Consult the glazing system manufacturer’s literature for additional design and placement guidance for the temporary supports, particularly for systems that include toggle bolt receptors in the framing.
3. Specifying for better outcomes
3.1 Specify the correct sealant
Designers should understand that specifying a structural sealant for field installation involves more than reading the original project specification which was likely intended for shop installation.
Sealant selection can influence aesthetics (i.e. color, gloss), performance (i.e. material strength and elongation properties), schedule (i.e. cure time), installation process (i.e. work time, pump speed, priming requirements), and warranty (i.e. manufacturer limits). Historically, two-part sealants used in factory-fabricated systems were not practical for field use because they require large, sophisticated pump equipment and regular quality control calibrations that are costly and cumbersome. As a result, installers traditionally relied on one-component, self-priming, neutral cure, structural silicone sealants for field installations.
Many one-part structural silicone sealants have a long track record of successful performance spanning over 20 years. However, these one-part sealants typically develop full cure and adhesion after 14 to 30 days, or more in cold weather. A long cure time not only affects logistics of accessing a building facade to replace glass and remobilizing facade access to remove temporary supports, but it also delays the required quality control activities by 14 to 30 days (i.e. pull tests and deglazes which are discussed below). In large glass replacement projects, finding a quality issue after 30 days of production could mean reworking or deglazing a large percentage of the completed contract work. For this reason, when using a one-part sealant it is essential the contractor perform on-building, pre-construction mockups to identify and resolve quality issues prior to production.
Recently, several manufacturers have developed two-part, fast cure (i.e. 24 to 48 hours) structural silicone sealants for field use. Rather than sophisticated pump equipment, the components mix in a disposable nozzle attached to a standard sealant cartridge. Billed to have equal performance to traditional two-part shop-applied sealants without the corresponding schedule delay of one-part sealants, these two-part sealants have a relatively short track record of around five years, and mixed reception with installers and the challenges of field installations in the experience of the authors.
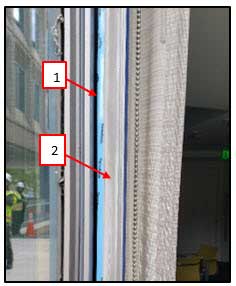
Sealant manufacturers market two-part sealants as a ‘cure’ to the one-part silicone cure-time problem. However, the fast cure times of current two-part sealant formulations also result in fast skin-over times, particularly in hot weather. In summer months, two-part sealants can skin over prior to complete installation of an SSG joint, sometimes resulting in hard edges between cured and uncured silicone, fissures, and gaps in the joint from resistance to smooth tooling, or aesthetically ‘clumpy’ tooled joints. The slow pump speed of the two-part sealant guns exacerbates these issues, and multiple workers will commonly apply sealant to the same panel simultaneously to finish the perimeter within the two-part sealant work time. A bigger issue arises when an IGU requires blind seal installation, the two-part sealant may skin over before the installation of the IGU, creating a poor, or non-existent, bond between the glass and the sealant. For this reason, it is also important to perform pre-construction mockups for two-part sealants and continue to monitor skin-over time of two-part sealant as weather and installation conditions change.
the installers shall be trained in the proper installation of dow 795 structural silicone