Casing bead installation and joinery
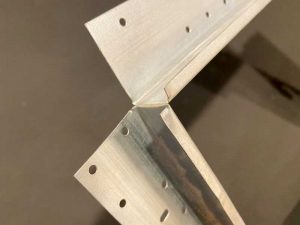
Casing bead installation and joinery requires careful planning, an understanding of water management requirements, and coordination to assure the objectives of the installation are satisfied. Typical joinery consists of linear splice joints and corner joints, such as around windows, doors, and other exterior building components.
Casing beads should be constructed and installed to prevent water penetration along panel edges. This is consistent with Appendix A2.1.3 of ASTM C926, which reduces the burden on the wall’s water resistive barrier and flashing components. As Bateman and Luft illustrate, casing bead linear splice joints can be constructed in several different ways to improve water resistance of the stucco cladding system. Watertight linear splices may require splice plates, nested tabs, and sealant applied in the correct locations to be functionally effective at water management. Casing bead perimeter frames surrounding a wall opening will include corners at head/jamb and jamb/sill conditions. Simply slitting the casing beads’ attachment flange and bending it 90 degrees will result in a casing bead corner open to water infiltration. Configuring an installed casing bead with a solid attachment flange where the corners are correctly lapped and sealed may, with careful planning and execution, improve water resistance and allow integration with the water resistive barrier assembly on the wall.
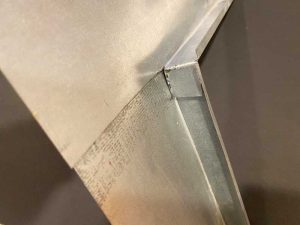
Recent casing bead innovations with enhanced function and aesthetics
Based on the hundreds of patents issued for stucco-related innovations over the years, the stucco industry has a history of attracting innovators and inventors. In the last couple of years, a few notable casing bead-related products have made it to market through major manufacturers.
One manufacturer has developed a casing bead featuring an integral backer rod, which provides both the necessary gap to adjacent unplastered construction and to receive sealant. This manufacturer tested two windows installed into a laboratory test wall—one without their casing bead and sealant, and the other with their casing bead and sealant—subjecting both specimens to an ASTM E331 test. The casing bead and sealant specimen passed the test of an 80-km/h (50-mph) wind-driven rain, while the specimen without the casing bead and sealant failed in less than 15 minutes. This same manufacturer is now also producing a casing bead with a self-furring key attachment flange, to improve embedment of the casing bead. Another manufacturer is producing a casing bead with a recessed and embedded rather than exposed capture flange. This innovation accommodates a lamina base coat and eliminates the buildup and cracking typical of standard capture flange casing beads, when used with lamina base coats.
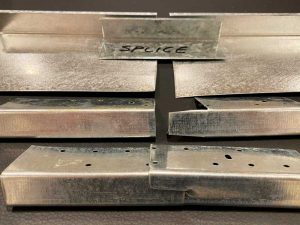
Conclusion
In summary, a significant concern of building owners, designers, and stucco craftsmen is ‘stucco leaks,’ with resultant concealed water-related exterior wall damages. This is in part due to omission of the panel edge joint at stucco cladding perimeter conditions at dissimilar materials (unplastered construction), such as around windows and doors. Concealed water-related exterior wall damages can be minimized or avoided where the stucco panel edge joint consisting of casing beads and sealant to prevent the entry of water as ASTM stucco standards describe, is included as an essential subassembly of the stucco cladding system, in both design and construction.
A great overview; I wish it had been available when I became an architect, or even later, when I became a specifier!
I am an owner builder in the San Diego area. I would like to know the casing manufacturers of the casing types that were discussed on the last page of your article
Al’s Can you refer me to or provide a spec that I can use in the bid process.