Why substitutes might be considered
One of the foremost reasons a substitute may be used is the limited availability of the original material. This can be the case for traditional materials found in pre-war construction, as well as industrial materials for modernist and contemporary buildings. Availability issues can include such things as quarries being closed when an exact stone match is desired, or when an old growth wood is no longer harvested.
Availability can also be affected by the reduced quantity of skilled craftsman. Prior to mass production, many historic structures with ornamental components were produced by specialized individuals, such as carvers, metalsmiths, stonemasons, and carpenters. Although these trades still exist, most remaining workers within these professions are typically educated to produce more standardized contemporary assemblies. So, there are fewer trained people available to reproduce historic conditions, and this is especially applicable to complex, handcrafted pieces.
Constructability issues can also generate the need for substitutes, even if the material or trade is readily available. Sometimes, the size, weight, or configuration of original materials might be too cumbersome to replace with a matching material, such as monolithic stone blocks in load-bearing masonry construction. Repair in lieu of replacement of these elements is often preferred.
Availability can be an issue even for historic materials which were once mass produced, such as terra cotta. A popular material in the late 19th and early 20th centuries that once had many sources throughout the United States, architectural terra cotta now only has two major manufacturers in the country. Limited availability not only affects lead time, as it can take longer to source, but it also makes the product more costly. These conditions can also be exacerbated by the amount of material that is needed to be replaced, but how this plays out depends on multiple factors. Less material does not necessarily take less time to generate, as it may not be beneficial to the fabricator to interrupt steady production of standard units if only a handful of unique units need to be replicated. However, if there is a large number, and especially if they are repetitive, the supplier may be motivated to prioritize the order.
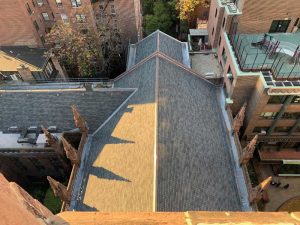
When cost and lead time are a problem, it can be especially concerning when deteriorated material is being replaced to address a safety issue. This is common with masonry conditions on urban high-rise buildings, especially those municipalities with stringent facade inspection requirements, like New York and Chicago. In these scenarios, when owners are under pressure to correct safety issues within strict timeframes set forth by local laws, they may be inclined to replace with a substitute, especially if it costs less or is readily available. This problem can be exaggerated by the compounding costs of protection, scaffolding, and stabilization that might be needed to address the unsafe conditions, not to mention the fines incurred from local building departments. This can further sway building owners toward substitutes, at least as a temporary solution.
There can also be performance reasons for selecting a substitute material. A design professional may determine the original or existing materials have fundamental deficiencies, or they were inappropriately implemented in an assembly, climate, or exposure that makes them prone to deterioration. Some examples include:
Thin marble panels
Used in many modernist buildings, thin marble is susceptible to hysteresis when exposed to heat, a type of permanent deformation that causes it to progressively bow, crack, and eventually dislodge from its attachments. Several of these buildings have required multiple replacements of the original material, and some have been reclad with a different material due to the ongoing issue.
Brownstone
Commonly used in 19th century townhouses in the northeastern United States, this soft and porous stone is subject to exfoliation and spalling, which is worsened by the northeast climate, where freeze/thaw cycles occur every winter. It is worse yet in urban areas with heavy pollution, as surface soiling traps moisture which further wreaks havoc during freeze/thaw cycles.
Metals prone to corrosion
Corrosion is often found in early high-rise buildings, which began to use ferrous structural and anchorage components in a substantial way but did not necessarily incorporate coatings, membranes, or adequate solid masonry infill to protect the metal. Additionally, certain combinations of metal can make them prone to galvanic action (corrosion resulting from adjacent dissimilar metals, such as aluminum and copper).
Inappropriate use of wood
Wood can also be expressive of this condition, as not all species and types are equally suitable to exterior exposure. This is more prevalent in post-war wood constructions that no longer used old growth lumber, which was more decay resistant.
These examples show substitutes do not necessarily have to involve more contemporary synthetic materials. Instead, they might also include traditional materials that are more suitable to the application than the original material. The example of metal also shows how substitute materials can be equally relevant to concealed anchorage and structural systems, as they are surface materials. These components may need to be replaced with substitutes, not only because they lack corrosion-resistance, but because they may have fatigued or were not engineered to contemporary standards. Sometimes supporting metal has deteriorated but cannot be replaced, or its structural capacity cannot be confirmed. These can be additional reasons to replace exterior claddings that rely on these metal components with substitutes that are lighter weight, such as cast composite resin replacing stone or brick masonry, or asphalt shingles replacing slate or terra cotta roofing.
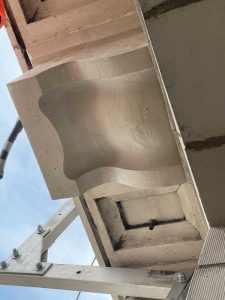
Other backup and underlayment materials might also need to be replaced with substitutes for both facade and roofing projects, such as waterproofing materials. Historically, felt paper and coal tar pitch were used. However, contemporary advancements such as self-adhered rubberized membranes or fluid-applied membranes can allow for greater ease of installation than hot-applied materials. These membrane systems are more waterproof than traditional felt paper, too.
Substitutes might also be used when there is a new addition to an existing building, or a portion of a building is being largely reconstructed. In these scenarios, the new addition or reconstruction might intentionally be made to look like an intervention to the surrounding fabric and the substitutes could assist with creating an aesthetic contrast, whereby new material colors and finishes are purposefully different than the old. Additionally, these new or reconstructed assemblies may need to comply with contemporary standards or be reconfigured to correct deficiencies that prompted replacement or augmentation in the first place. These upgrades might demand physical and chemical properties that differ from those of the original assembly, such as structural strength, lighter weight, or improved moisture management.
What are the concerns with using substitute materials?
While there may be situations where substitute materials can be used, there are considerations design professionals and owners should thoroughly evaluate before implementing them. The most common and significant concern with substitutes is compatibility, especially when select materials are being replaced in an otherwise existing or original assembly. The new material may have properties that differ from those of adjacent materials, which could make it prone to deterioration or liable to cause damage or accelerate decay within the surrounding substrates. Differences in coefficients of thermal expansion, for example, can cause adjacent materials to crack or displace as they move differentially over time.
Differences in vapor permeability, watertightness, and porosity are also a concern, as they all play a role in moisture mitigation, both from external precipitation and condensation of warm, moist air from building interiors. Substitute material insertions should be carefully analyzed to verify they do not admit excessive moisture into the assembly. They should also allow moisture to escape where appropriate. Interventions within historic masonry assemblies can be especially sensitive to these issues, as they manage moisture differently than contemporary cavity walls or rainscreens. Condensation can also be a concern in historic roofing assemblies that are replaced with less porous cladding, underlayments, and/or insulation, which can cause moisture to accumulate at the underside of the roof deck, within attic spaces, or within the roof assembly. Not only can condensation cause water-related deterioration, but it also could potentially generate mold.
Other compatibility issues can involve differences in dimensional stability, the tendency for a material to maintain its shape and size over time. Clay-based materials like brick and terra cotta gradually expand as they re-absorb moisture, but concrete materials tend to shrink as they continually cure. Additionally, materials not only experience elastic deformation, and regularly change size and shape when exposed to the elements, but as noted with thin marble, they can also become plastically deformed when their molecular structure changes due to fluctuations in thermal or structural loading. Over time, these dimensional changes can create microscopic openings that are avenues for moisture infiltration and freeze/thaw damage. On a macroscopic level, they can also cause cracking and displacement, as localized failures cause differential settlement.