Common Substitutes and Associated Exterior Components | ||
Original/Existing/Historic Materials | Substitute Materials | Typical Facade and Roofing Components |
Solid Stone Masonry (Limestone, Granite, Bluestone, Marble, etc.) and Structural Clay Masonry (Brick and Terra Cotta) | Cast Stone/Architectural Precast Concrete, Geotextile Fiber Reinforced Concrete (GFRC), Cast Composite Resin | Facade/Parapet Wall and Chimney Bricks, Blocks, Copings and Caps, Windowsills and Headers, Facade Ornamentation (Cornices, Brackets, Banding, Statuary), Steps, Landings, Pavement, and Site Walls |
Slate and Terra Cotta (Roofing and Cladding) | Composite (Plastic/Rubber), Plastic/Rubber, Asphalt, Cast Stone/Architectural Precast Concrete | Roof Shingles, Wall and Rain Screen Tiles |
Solid Wood Timber (Non-Structural) | Composite (Plastic Encased Wood Fibers), Vinyl, Cement Fiber | Facade Siding/Cladding, Window/Door Trim, Sills and Headers, Eave/Rake Soffits and Fascia, Facade Ornamentation (Cornices and Brackets), Porch Finish Decking, Posts, Steps, and Guardrails/Railings |
Solid Wood Timber (Structural) | Engineered Wood (Cross-laminated Lumber, Densified Wood, Wood Byproducts (Plywood, Waferboard, Fiberboard, Laminated Lumber) | Roof and Porch Substrate Decking, Facade Sheathing, Framing Members (Studs, Posts, Beams/Joists, Rafters, Joists, Trusses, Purlins, Bracing) |
Cast Iron and Wrought Iron (Structural) | Extruded Aluminum, Plain Carbon Steel, Stainless Steel, Galvanized Steel | Guardrails/Railings (Roofs, Balconies/Terraces Landings/Stairs), Window Guards, Decorative Grills, Gates/Fences, Stone Anchorage, Supporting Angles/Lintels, Framing Members (Beams/Girders/Joists, Trusses, Rafters, Columns, Bracing), Bolted Connections/Fasteners |
Copper, Lead, Tin, etc., Sheet Metal and Non-Structural Cast Iron | Aluminum, Galvanized Steel, Stainless Steel, and Galvalume Sheet Metal, Polyvinyl Chloride (PVC) Sheets/Pipes/Sections, Sheet Membrane (Bituminous/Rubberized, Fluid/Liquid Applied) | Roofing Seams, Roofing Shingles/Sheets, Flashings, Fascia, Drip Edges, Exterior and Interior Roof Drainage (Scuppers, Conductor Heads, Drain Domes/Bodies, Downspouts/Leaders) |
Asphalt Soaked Felt Paper, Coal Tar Pitch, Hot Mopped Asphalt, Mastic | Sheet Membrane (Bituminous/Rubberized, Fluid/Liquid Applied) | Roofing, Flashings, Underlayments |
Mortar and Grout | Sealant/Caulking (Silicone, Polyurethane, Butyl, Latex), Neoprene and Rigid Foam, Epoxy and Methyl Methacrylate Adhesive | Joints and Setting Beds for Masonry/Tile Facade/Cladding and Pavement, Expansion/Control Joints, Flashing Terminations, Bearing Pads, Compressible Filler and Backer Rod, Setting Pockets for Masonry Anchors and Reinforcement Bars |
Oil Paint | Acrylic, Latex, Epoxy, Fluoropolymer, Potassium Silicate | Coating/Coloring Wood, Metal and Masonry/Concrete Surfaces |
Substitute materials can also create problems if strength and weight are not properly evaluated. Not all masonry is created equal, and depending on its type, origin, and applications, it can have different degrees of compressive, tensile, and/or flexural strength, as well as different densities. Similarly, for structural components, stainless steel may be significantly less prone to corrosion than plain carbon steel, but it is also weaker, so dimensions, attachments, or frequency may need to be adjusted to accommodate these differences.
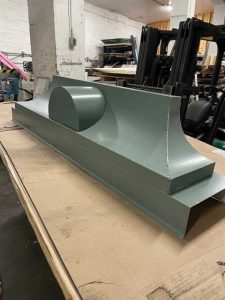
Addressing these compatibility concerns is not only a matter of selecting the right materials but may require alterations to the material unit or assembly. This could involve supplemental reinforcements, anchorage, and support augmentation, or redirecting load paths to address structural concerns. To mitigate potential moisture infiltration issues, it might involve the introduction of waterproofing membranes or sheet metal flashings and drip edges where none currently exist or increasing their size or configuration where they do. It could also involve the use of coatings, either for the substitutes or adjacent existing materials, to increase their weather durability and waterproofing capacity or to conceal differences between new and old materials.
Different joint materials might also need to be used to address concerns with breathability, adhesive capacity, or galvanic action. For example, cast composite resin does not bond well with mortar unless primed, as it is not porous like masonry or concrete, but sealant will adhere to it. However, the potential for trapping moisture must once more be considered as the less porous cast composite increases this potential, especially when combined with watertight sealant. When new metal types are introduced, it might require a separation, such as a gasket or coating to avoid contact with a dissimilar metal. These conditions demonstrate the need to consider the behavior of the entire enclosure, and how much of it is being replaced, because that affects whether the substitute materials may present issues or require modifications.
Other concerns include the ability of a substitute to achieve a true color, texture, or profile match, which requires special consideration on landmarked historic buildings. Material technology has evolved greatly in recent decades to allow for closer matches, but as many substitutes are machine-fabricated and mass-produced, they do not always have the handcrafted or natural character of traditional materials, which often contain more surface variations. Some composite materials with external veneers or coatings have been engineered to create better matches, but they are susceptible to delamination of the veneer or coating from its substrate. Colorfastness, the ability to hold color over time, is also an important aesthetic consideration, as many natural and traditional materials tend to exhibit better colorfastness. Some substitutes, especially those with coatings and thin veneers, are not dyed throughout their cross-sectional thickness, and can be subject to fading from ultraviolet (UV) degradation and weathering, and might require recoating.
Exterior replacements, and associated material selection, can be subject to review and approval by preservation boards or the State Historic Preservation Office (SHPO), depending on landmark status and applicable regulations. In general, replacement elements with higher visibility tend to be subject to greater scrutiny and are often needed to match original or existing materials. Substitute materials are more likely to be approved for components located on the upper floors, parapets, or roofs, or for isolated elements, as their different texture might be less noticeable, or less likely to contrast with adjacent elements. Whether or not the building is part of a landmark district, or a prominent individual landmark, can also affect where, how, and what substitutes could be used. The reason for landmark status could also affect the decision to allow a substitute. A building that is landmarked because of a historical event, as opposed to architectural character, might have fewer design limitations.