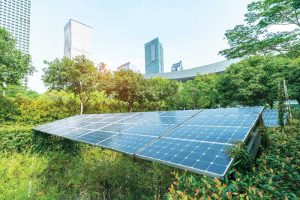
Many new design processes, materials, and construction techniques have been developed to achieve this goal, and sustainable buildings are frequently cost-effective, but it often takes a considerable investment to save money. In 2019,
the International Energy Agency (IEA) estimated that realizing the potential of sustainable buildings can save $1.1 trillion by 2050; but these savings necessitate an increase of $270 billion in annual capital expenditure until 2030, with 70 percent of that being new construction and retrofits.4
Despite perceptions of higher investment, sustainable construction is not necessarily more expensive than traditional construction. Some sustainable design and construction costs have eased as sustainable building codes have become stricter globally, technologies have evolved, and the industry has become more adept at delivering sustainable buildings.5
Materials, methods, and models
It is helpful to view sustainable building development through three lenses: materials, methods, and models.
Materials
Sustainable materials, such as treated wood and smart glass, help reduce emissions throughout their lifecycle. They require end-to-end strategic sourcing capabilities, including cost, quality, and supplier management. If their upfront cost is higher, the difference can be offset by a lower long-term life-cycle cost, particularly for high-performance facades and energy-efficient systems. Costs of sustainable or low-carbon construction materials will likely gradually decline compared to conventional materials due to lower ingredient costs of recycled or by-product materials.
Methods
Sustainable methods such as prefabrication, modular construction, 3D printing, advanced manufacturing, and generative design can dramatically reduce the waste lifecycle of construction projects, further saving costs. These methods require effective supplier collaboration and development programs to manage cost and risk. These methods can also help reduce labor costs, ensure better design and quality control (QC), and shorten project schedules to help minimize budget overruns.6 Deloitte found that nearly half (46 percent) of respondents to its 2023 Engineering and Construction Industry Outlook will likely invest in prefabrication and modular construction capabilities next year.7