Sustainable, high-performance design with natural stone
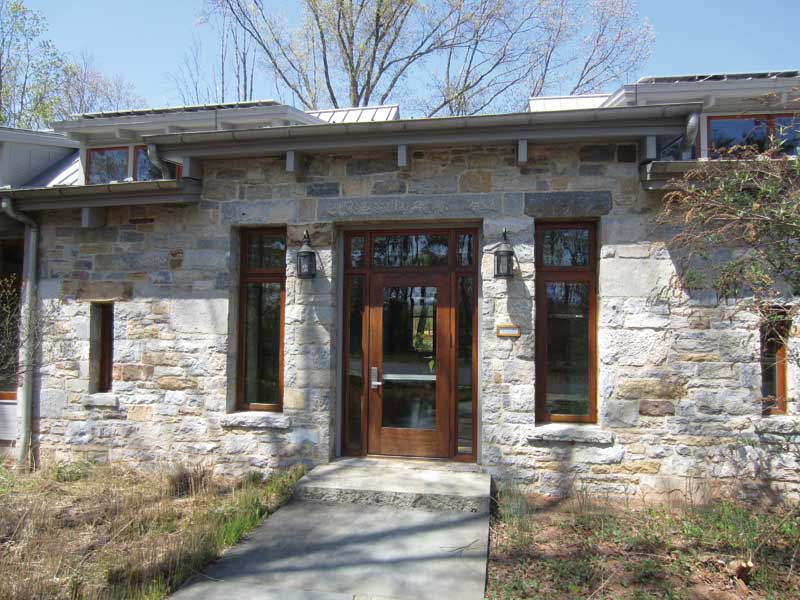
Photo courtesy the Willow School
Stone can also be reused or recycled, minimizing the need for raw or virgin materials and reducing material replacement costs over a longer period. Mark Biedron, the founder of The Willow School (Gladstone, New Jersey) understood this concept well. The project’s team chose to incorporate several sources of local, recycled stone into the school to achieve LEED credits while also establishing a 150-year life cycle for the building. The classrooms used the remains of two barns and a house from Eastern Pennsylvania dating to the 19th century—a 75 percent hand-cut limestone and 25 percent sandstone mixture. This stone had already served for 100 years in the barns, but was expected to last another 150 in the school—a testimony to the material’s endurance.
The project requirements also stipulated the following:
- specification of at least 20 percent of building materials that are manufactured regionally within a radius of 800 km (500 mi);
- use of local stone to meet LEED Regional Materials credits and Material Conservation credits; and
- use of durable materials to support a 150-year life cycle.
The design called for the stone to be used as part of the façade and cavity walls in 200-mm (8-in.) sizes. At the foundation, the stone was specified at 100 mm (4 in.) and had to be solidly mortared to the foundation. The stone was also used for the lintels. All these approaches supported the goals of meeting the 150-year life cycle with durable materials and installations. Due to the unique nature of the project, the stone detailing had to be specified onsite.
A different approach to sustainability and performance was taken by architect David Hughes for the creation of a train drivers’ facility in Ireland. The project was designed to meet Passivhaus requirements, which attempt to strike a balance between the heat losses (e.g. through the building fabric and ventilation) with the heat gains (e.g. from people, appliances, lighting, and solar gains in the winter). The project was also designed for deconstruction in mind.
Granite was selected to address both goals, and can be used in another application in the future. This was achieved by designing the stone units to be the same size, except at the corners and details to windows, which made the ordering and processing of the stone more efficient. This also makes the stone’s reuse much easier due to the consistent dimension. The stone is dry-mounted on a stainless steel hanging system that uses the dead weight of the units (and some concealed dowels) to fix the stone on an independent self-supporting fixing system.
No silicone sealant was used in the joints for several reasons. First, from a deconstruction point of view, the material remains close to pristine. Technically, the joints allow for the pressure equalization of the ventilated air layer behind the stone. Aesthetically, omitting silicone avoids staining the edge of the stone, which can often be seen when silicone is used to seal the stone joints.
With many light-colored stones available, landscape design or site elements are enhanced by including stone as paving, stairs, railings, and walls to reduce the absorption, retention, and emittance of solar heat, contributing to reductions in heat island effect. Understanding the thermal properties of natural stone will encourage designers to incorporate it into the building envelope design for energy reduction strategies. Maintenance costs of natural stone are also minimal, contributing to reduced operations and maintenance costs over time. However, coordination with the operations and maintenance crews is essential to ensure sustainable cleaning methods are implemented.
Use of the most appropriate treatment and cleaning products is important to extend the life of the stone. Strong acidic cleaners can destroy stone, especially limestone and sandstone. If joint sealants are utilized, they need to be replaced every 10 to 15 years, depending on the type of sealant. If mortar is used, tuckpointing may be required during the life of the cladding.
Conclusion
There are many different approaches to creating a high-performance building project using natural stone. By understanding the drivers in the sustainability and high-performance building movement, including advancements in the natural stone industry, one will be equipped with the knowledge of how to select, source, and install the best stone for the project. This leads to a building that performs well and makes an excellent ROI over a long period.
ADDITIONAL RESOURCES |
|
Stephanie Vierra, Assoc. AIA, LEED AP BD+C, is the president of Vierra Design & Education Services LLC. With almost 30 years of experience in architectural associations, practice, and research, she has developed, managed, and taught programs that support an interdisciplinary and integrated approach to a variety of design and technical topics. Vierra has actively developed education and outreach programs on sustainability for the natural stone industry for the last decade, teaching and writing extensively on the material. She served on the NSC 373 green standard and Chain of Custody standard committees for the natural stone industry, and is a technical editor for the National Institute of Building Sciences (NIBS) Whole Building Design Guide (WBDG) portal. Vierra can be reached at suvierra@comcast.net.