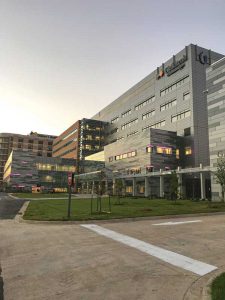
Resistance to sulfate attacks
Sulfates, which are present in seawater, wastewater, and some soils, can react with the alumina in Portland cement and cause expansion. Some SCMs offer powerful resistance to these attacks because they contain fewer of the compounds which react with sulfates, and their low permeability keeps sulfate-bearing waters out. Typically, slag cement, silica fume, and Class F fly ashes are very effective in improving sulfate resistance.
Portland-limestone cement
One proven solution for reducing greenhouse gases per ton of cement—without sacrificing its performance—is Portland-limestone cement (PLC). Proven to serve as an effective alternative to ordinary Portland cement (OPC), PLC is a high-performance blended cement manufactured with up to 15 percent of finely ground high-quality limestone.
In the U.S., the American Society for Testing and Materials (ASTM) permitted up to five percent limestone in Portland cement in 2004 (ASTM C595). At the time, it was estimated that these changes would reduce energy consumption by 11.8 trillion Btu and CO2 emissions by more than 2.5 million tons (2.3 million tonnes) per year. In response to calls to further reduce the carbon footprint of the building sector, ASTM C595 was revised in 2012 to allow up to 15 percent limestone in Type IL blended cement. Type IL cement provides strength development, durability, workability, and other properties like Type I and II cements.
With Type IL cement, similar percentages of SCMs can be used in concrete mixes while also replacing up to 15 percent of the Portland cement with limestone. This results in an additional 10 percent reduction in greenhouse gas emissions associated with the production of Portland cement clinker. When combined with SCMs, the effective reduction in the CO2 footprint of concrete is highly significant.
Slag and PLC: Lowering carbon footprints of buildings in Seattle
Seattle has quickly become one of the fastest-growing technology hubs. In pursuit of its goal to become carbon neutral by 2050, the birthplace of the nation’s green building movement has adopted an ambitious climate action plan and was the first U.S. city to approve the use of PLC for structural concrete. With an ever-expanding presence in their hometown, tech leaders responded to the call to action on global warming with affirmative commitments to lower their carbon footprint.
When a prominent local technology and logistics company added 39,019 m2 (420,000 sf) of new headquarters space and broke ground on a major building expansion, the construction used high-performance mixes to achieve a clinker factor of 16 percent, the lowest in the Seattle area.
The concrete used in the signature “spheres” of the headquarters was designed with 80 percent slag cement to achieve its sustainability goals, 55,158 kPa (8000 psi) strength requirements, and aesthetic needs.
Another iconic resident in Seattle’s business community has committed to removing more carbon than it emits by the end of the decade.
The addition of more than 1.86 million m2 (2 million sf) of new office space at this tech giant’s 202-ha (500-acre) headquarters campus is relying on concrete mixes, designed with PLC and slag cement to reduce embodied carbon by at least 15 percent.
The photo caption to this story has incorrect information: the project One Dalton is located in Boston, Massachusetts – not Washington DC and it is LEED certified Silver, not platinum.
Thanks a lot for pointing that out. We have modified the caption of the photo.