FAILURES
Deborah Slaton, David S. Patterson, AIA, and Kenneth M. Itle, AIA
From the late 19th century through the 1930s, terra cotta was widely used as a façade material in the United States. Terra cotta initially became popular because of its fireproof qualities, and was soon recognized for its aesthetic characteristics as well. The material could be fabricated in simple or elaborate forms, with glazes providing a wide range of colors and aesthetic effects. Terra cotta is generally durable, but when façade rehabilitation is planned, one of the most challenging questions is whether a distress condition that is observed requires repair or replacement of the unit, or can be left as is.
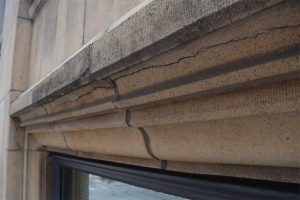
Photos © Kenneth Itle, WJE
When evaluating existing conditions of terra cotta, it is important to understand both the causes of the observed distress and the typical methods of installation used historically with the material. In the first example shown, a continuous crack extends across the face of several terra cotta units above a window head. The terra cotta units at this location are suspended from steel framing using J-bolts and steel rods. Gaps in the mortar and sealant joints between the terra cotta units have allowed water to reach the steel, which has subsequently corroded. Expansive corrosion has exerted pressure on the terra cotta units, causing them to crack. Cracks in these units are similar in size to those observed in other units on the façade. However, the configuration of the units at this location suggests the fractured portions of the suspended units may not be properly supported in the current condition. The terra cotta units will need to be removed to examine the concealed steel and implement repairs. If the fractured units can be removed in intact pieces, it may be possible to pin each unit together prior to reinstallation (followed by repair of the cracks). However, depending on the configuration of the steel anchorage and the extent to which the units fracture further upon removal, replacement of the affected units may be required.
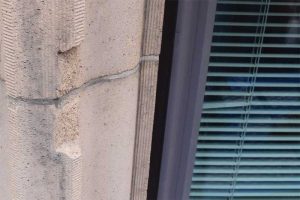
In the second example, a spall has occurred on either side of a bed joint between two terra cotta jamb units. The form of the spall suggests it occurred because of a localized stress concentration, possibly due to either expansion of the terra cotta over time or an incompletely filled bed joint. The spall is shallow enough that the hollow interior of the unit is not exposed. Also, this spall is located high up on the façade and is not considered aesthetically intrusive. Although the terra cotta body is exposed, it is not particularly absorptive, and the spall area does not require a glaze repair. (Note, the terra cotta shown in these examples has a matte finish, typically achieved with a slip glaze.) The configuration of the spall does not prohibit proper pointing of the mortar joint; thus repair of the spall is not needed.
Determination of appropriate repairs requires not only assessment of observed conditions, but also an understanding of underlying conditions and as-built construction. A condition that may indicate a structural deficiency in one location (e.g. the fractured suspended units mentioned above) may not require repair in another (e.g. where the unit is well supported within the field of the wall).
The opinions expressed in Failures are based on the authors’ experiences and do not necessarily reflect those of The Construction Specifier or CSI.
Deborah Slaton is an architectural conservator and principal with Wiss, Janney, Elstner Associates (WJE) in Northbrook, Illinois, specializing in historic preservation and materials conservation. She can be reached at dslaton@wje.com.
David S. Patterson, AIA, is an architect and senior principal with WJE’s office in Princeton, New Jersey. He specializes in investigation and repair of the building envelope. He can be reached at dpatterson@wje.com.
Kenneth M. Itle, AIA, is an architect and associate principal with the Northbrook office of WJE, specializing in historic preservation. He can be reached via e-mail at kitle@wje.com.