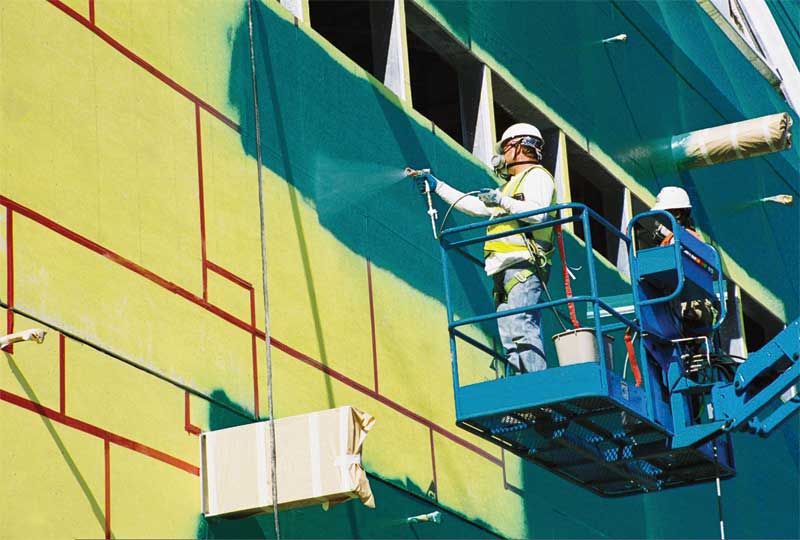
Fluid-applied air and water barrier products have rapidly gained market share in many areas of the country, but they are still relatively new to the industry. It is perhaps unsurprising then that various failures of these products have been seen during their installation.
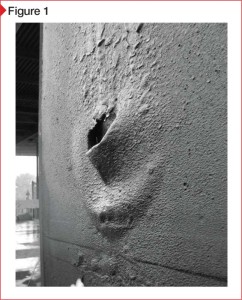
The opportunity to observe these conditions is relatively narrow and usually occurs in the first few weeks of application before the exterior cladding is installed over the barrier. The most significant of these issues include cured membranes developing large water-filled blisters (Figure 1) or sliding off the wall (Figure 2). These failures occurred after the membrane had been installed for at least two weeks and immediately following rain. Their occurrence indicates excessive water absorption leading to poor adhesion, or reversion of the membrane to a fluid-like state.
Other shortcomings observed in the field include tearing of the membrane along the edge of self-adhered flashing, and alligator cracking of its surface. The first is symptomatic of poor elongation properties of the membrane, while the second is likely caused by excessive ultraviolet (UV) exposure.
Currently, the industry has few standards addressing the durability of these products, particularly when exposed to moisture over the long term. Many of these assemblies serve as the water-resistive barrier (WRB), as well as the air barrier for the wall. The Air Barrier Association of America (ABAA) evaluates fluid-applied systems by testing air permeance, water resistance, fastener sealability, adhesion to substrates (i.e. pull adhesion), and crack bridging.
The water resistance testing—per American Association of Textile Chemists and Colorists (AATCC) 127-03, Water Resistance: Hydrostatic Pressure Test—gauges the cured membrane against hydrostatic pressure for five hours. In reality, many membranes will be exposed to moisture for much longer than this period, particularly when used in the wet zone of the wall assembly. While the ABAA evaluation addresses initial performance, it does not deal with long-term durability issues. Even so, widespread project failures are observed even with products that have been evaluated, and approved, by ABAA. Although ASTM is developing a standard for fluid-applied air barriers, it does not currently address durability issues for these products.
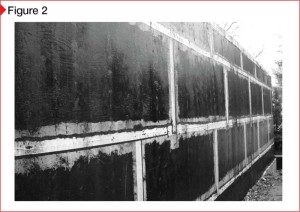
Given the relatively short track record of these products and the failures observed with some, it seemed prudent to develop an in-house program of laboratory testing to better assess their prospects for long-term performance. For practical reasons, the testing program was limited to products from four manufacturers that were early leaders in the fluid-applied air barrier market.
Both vapor-permeable and vapor-impermeable products from each manufacturer (including two vapor-permeable ones from the same company) were tested for a total of nine. These materials included membranes that exhibited those aforementioned problems in an attempt to replicate the failures in the laboratory and confirm suspected mechanisms. The ultimate goal was to have a basis for deciding their prospects for long-term performance in lieu of a historical track record. This is particularly important since many building owners are interested in using these products; furthermore, many contractors are requesting these materials as alternates to more time-proven products such as self-adhered membranes.
Lab testing of fluid-applied air barriers
To achieve the set goals, testing focused on three important performance properties: pull adhesion, flexibility (i.e. elongation), and water absorption.
Pull adhesion
For a membrane to successfully perform as an air barrier, it must exhibit adequate adhesion to the wall substrate. The membranes were tested for adhesion to several common materials.
Flexibility
The membrane must span joints in sheathing boards, and joints between dissimilar materials, such as at flashings. These joints experience minor movements through the life of the building. Since the membrane must provide a continuous barrier, and not split or tear under these movements, its flexibility was evaluated by elongation testing.