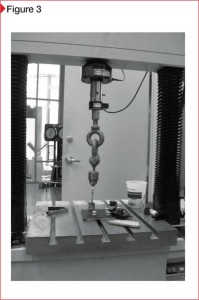
Water absorption
From previous testing of roofing and waterproofing membranes, water absorption has proven to be a good indicator of long-term membrane durability. Currently, no industry standards address water absorption of fluid applied membranes; therefore, traditional water absorption testing of waterproofing and roofing membranes is a starting point. Industry experience has shown reliable waterproofing membranes have low water absorption, ranging from less than a four percent increase by weight to an upper bound of 10 percent.
While the air barrier will be exposed to far less water than will a roofing or plaza waterproofing membrane, cladding systems are almost never watertight. This means the air barrier, which typically also acts as the WRB, is exposed to some water. Additionally, when insulation is used in the cavity wall, water can be held against the membrane for prolonged periods, trapped between the air barrier and the insulation. Often, water entering cavity walls does so at the same locations during each storm; while the entire wall membrane might not be wetted, other areas will be, repeatedly.
Summary of conditioning
To help assess the prospects for long-term product performance, samples were conditioned to reflect various environmental factors, and the pull-adhesion, elongation, and water-absorption tests were repeated. Conditioning of the samples included exposing them to UV light, freezing temperatures, accelerated aging, and water exposure. Only one conditioning element was applied to an individual sample, and not the aggregate of all the conditioning.
UV exposure
Using a UV fluorescent light apparatus, the samples were exposed to UV light for 14 days—22 hours of UV light followed by two hours of condensation daily.
No direct correlation can be made between hours in the UV machine and days exposed on a job site. Of all conditioning procedures, UV-exposed samples exhibited the greatest change in physical appearance.
All tested fluid-applied air barrier products, except one, are not marketed as ‘UV-stable’ and not intended to be exposed (permanently) to UV light. Still, all products will be exposed to UV for some amount of time, depending on the phasing of construction projects.
During testing, two of the membranes changed color after exposure. Three of the membranes, including the one marketed as ‘UV-stable,’ exhibited cracking and crazing of the exposed surface.
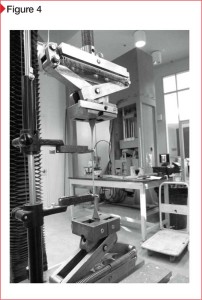
Freezing temperatures
Before testing, the samples were exposed to –6.7 C (20 F) temperatures for 48 hours, followed by 24 hours minimum at room temperature.
Accelerated aging
The samples were oven-aged for 28 days at a temperature of 70 C (158 F), followed by 24 hours minimum at room temperature prior to testing.
Water exposure
For elongation testing, samples were submerged in distilled water for 24 hours. For adhesion testing, edges of the substrates were taped off to prevent water absorption by the substrate, and the membrane covered with wet burlap and polyethylene for 24 hours. All samples dried for at least 24 hours before testing.
Testing procedures
Testing of each respective property was conducted in general conformance with ASTM standards:
Adhesion to substrate
Using ASTM D4541, Standard Test Method for Pull-off Strength of Coatings Using Portable Adhesion Testers, adhesion of the fluid-applied air barriers was tested to six common construction materials, all of which are listed as acceptable substrates for the nine materials tested. As shown in Figure 3, substrates tested were:
- plywood;
- oriented strandboard (OSB);
- fiberglass mat gypsum sheathing;
- concrete masonry units (CMUs);
- gypsum wallboard; and
- self-adhered membrane flashing (product as recommended by each manufacturer).
Samples with the following conditioning were tested:
- unconditioned (control);
- freezer exposure;
- accelerated aging; and
- water exposure.
The samples could not be exposed to UV due to limitations of the machine on the size of the samples.
Elongation
A universal test machine was used to apply a tensile force to the ‘dog-bone-shaped’ samples, as per ASTM D412, Standard Test Method for Vulcanized Rubber and Thermoplastic Elastomers–Tension (Figure 4). Samples with the following conditioning were tested:
- unconditioned (control);
- freezer exposure;
- UV exposure;
- accelerated aging; and
- water exposure.