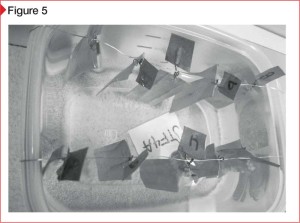
Water absorption
Using ASTM D471, Standard Test Method for Rubber Property–Effect of Liquids, Procedure 10, samples were submerged in distilled water for 24 hours (Figure 5) and their increase in mass was measured. Samples with the following conditioning were tested:
- unconditioned (control);
- freezer exposure; and
- UV exposure.
Summary of test results
This section summarizes the results of the testing.
Adhesion to substrate (pull adhesion)
ABAA has set a minimum pull adhesion of 110 kPa (15.95 psi) in its evaluation, which is also used for this testing. The failure mode—cohesive, adhesive, or failure of substrate—is recorded for each sample. The membrane passes when the average stress at failure is greater than this value and fails when the average is less than or equal to it. As Figure 6 shows, all samples exhibited adequate adhesion to all substrates under all conditions.
Elongation testing
Based on manufacturers’ published data for self-adhered air and water barrier membranes, elongation less than 200 percent is considered inadequate to accommodate expected movement at joints in the substrate. Elongation above 600 percent is considered excellent.
Generally, the elongation of the membranes increased after freezer exposure. Water and UV exposure had mixed effects on the membranes’ elongation, typically increasing it for the vapor-permeable ones and decreasing it for vapor-impermeable membranes. Accelerated aging generally resulted in a slight decrease of the elongation.
Further, the product that exhibited tearing (splitting) at the self-adhered flashing also exhibited poor elongation during the testing. Figure 7 summarizes the results.
Water absorption rates should be as low as possible—less than four percent by weight is ideal and greater than 10 percent is unacceptable. During testing, some membranes more than doubled in weight, which is excessive. Membranes that reverted to a fluid state or softened to the point where pieces broke away from the sample are considered to have failed.
All the vapor-permeable membranes increased in weight more than 10 percent. Two of the vapor-impermeable membranes increased in weight less than 10 percent.
The effect of additional cure time was also tested by examining other samples at week increments beyond the manufacturer’s stated initial cure time. Additional cure time was found to have no significant effect on the percent increase in the sample’s weight.
The team noted (confirmed) membrane failures observed in the field, such as large water-filled blisters and membranes returning to a fluid-like state and sliding of the wall, correlated with membranes that exhibited high or excessive water absorption during testing (Figure 8). Figure 9 summarizes the results of the water absorption testing.
Conclusion
The test results showed significant differences among these products, particularly when measuring for water absorption and, in some cases, elongation. When the design intent is to use the membrane as a water-resistive barrier within the exterior wall assembly’s ‘wet zone,’ only a few of the vapor-impermeable membranes seem appropriate based on water absorption values of 10 percent or less. All the vapor-impermeable membranes failed the water absorption tests, with some membranes dissolving or falling apart in water.
Many of the products tested were asphaltic-based membranes. New fluid-applied air barriers are constantly entering the market. Membrane manufacturers are now developing and beginning to market membranes with silicone and polyether chemistries, among others. These newer membranes are not included in the testing described in this article, but they too would likely have a range of results.
New products are often appealing and can offer initial cost savings to owners and contractors. After the cladding is installed, membrane deficiencies may go unnoticed for years, causing hidden structural damage. Once discovered, repairing the waterproofing (and any other damage) will be costly. Designers should be wary of products that do not have an established track record or sufficient testing to help predict long-term performance.
Katherine S. Wissink, PE, LEED AP, is a senior staff I at Simpson Gumpertz & Heger (SGH). She joined the firm’s building technology department in 2006 after receiving a master’s degree in structural engineering from Cornell University. Wissink is a member of SGH’s practice group for exterior wall systems, along with ASTM Committee E06–Performance of Buildings. She can be reached at KSWissink@sgh.com.
Laura R. Kellett is a staff II at SGH, joining in 2008. She is part of the building technology department, and a member of SGH’s practice group for exterior wall systems. Kellett graduated from Cornell University with a bachelor’s degree in civil engineering. She can be contacted via e-mail at LRKellett@sgh.com.
Stephen S. Ruggiero, PE, is a senior principal with SGH. He has worked in its building technology department since 1977, and specializes in exterior wall systems. Ruggiero is the former leader of SGH’s national practice group for exterior wall systems, remaining an active participant. He can be reached at ssruggiero@sgh.com.