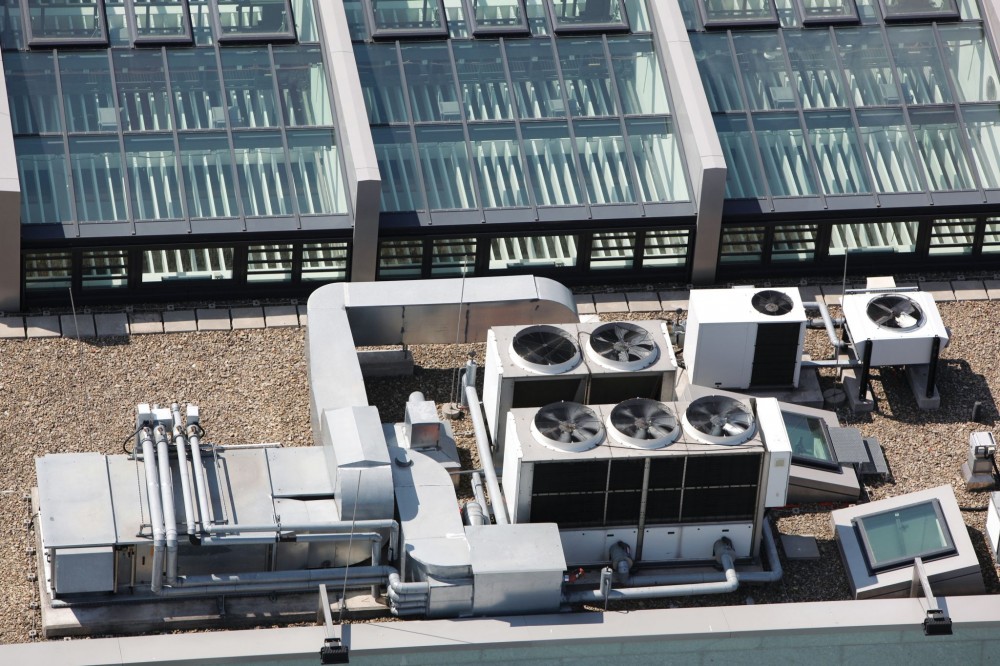
by David Brender, PE
For years, rooftops have housed mechanical systems?everything from heating and air-conditioning units to antenna communication infrastructures and mounted solar photovoltaic (PV) panels. With building space at a premium, property owners are now also looking at the roof for viable living space. It is not uncommon to see gardens, as well as outdoor living areas equipped with barbecue stations, in-ground pools, and rooftop bars, requiring full electrical systems for operation.
The roof has become prime real estate for commercial businesses and this trend is not expected to change. However, as the use of outdoor space becomes more popular, safety concerns related to the installation of electrical systems on the rooftop for industrial, commercial, and other flat-roofed buildings, have also grown.
The National Electrical Code (NEC) requires electrical cables in circular raceways (e.g. conduits) exposed to sunlight on rooftops, be ampacity-adjusted. Otherwise, they may be damaged. Ambient temperature is defined as the air temperature surrounding the conductor. Additional adjustments may be required for more than three current-carrying conductors in a raceway—the enclosed channel of metal or non-metallic materials designed for holding wires, cables, or busbars.
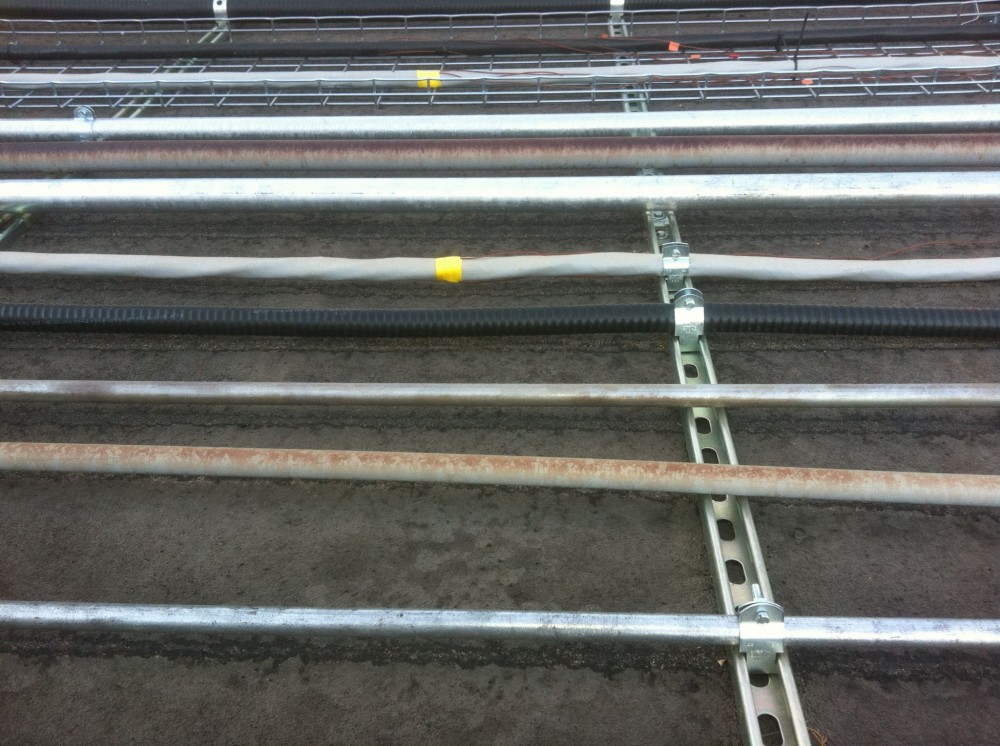
Testing the system
NEC requires no conductor should be used in a manner in which its operating temperature exceeds that for which it was designed. The NEC panel responsible for cable ampacities asked for comprehensive testing to be done to determine temperature in sunlight on rooftops. A fact-finding investigation conducted by Underwriters Laboratories (UL) intended to provide technical data for the proposed changes to portions of Section 310.15 of the 2014 NEC to include all cables, raceways, and other wiring systems. The study measures the safety aspects of installing raceways and cables exposed to direct sunlight on or above rooftops.
UL determined the test regimen and directed the particulars for the research, carried out in Las Vegas, with UL supervision and staff preparing the final report.
For this study, every possible rooftop wiring method was examined to record conductor temperatures that resulted from exposure to direct sunlight at various heights above the roof. The investigation took place at an outdoor testing facility and included experiments on 17 different types and sizes of electrical wiring systems, with conductors ranging from 12 AWG to 500 Kcmil, each of which were installed at four different elevations above the flat roof.
For cables, metal-clad (MC) types in several sizes were chosen to represent metal-clad and metal-sheathed cables and conduits, ranging in diameter to represent small, medium, and large sizes. Service entrance (SE) and tray cable (TC) types were also selected to represent jacketed cables. For conduits and tubing, rigid metal conduit (RMC) and electrical metallic tubing (EMT) were used to represent circular metal raceways while polyvinyl chloride (PVC) was chosen to represent the non-metallic category. For other metal wiring systems, metal raceways were used in 101 x 101 mm (4 x 4 in.) and 203 x 203 mm (8 x 8 in.) sizes.
Climate played an integral role in site selection. The city of Las Vegas was used to conduct the testing due to its broad range of daily solar radiation intensity and numerous cloudless days. Each wiring system was tested on rooftops of different colors, and at distances of 12.7, 89, and 304 mm (1/2, 3 1/2, and 12 in.) above the roof.
For wire testing conducted directly on the roof and 12.7 mm above the roof, the asphalt roof surface was painted black to account for additional heating from solar absorption. For systems tested greater than 12.7 mm, the asphalt roof surface was painted white to account for additional heating from solar reflection of the roof.
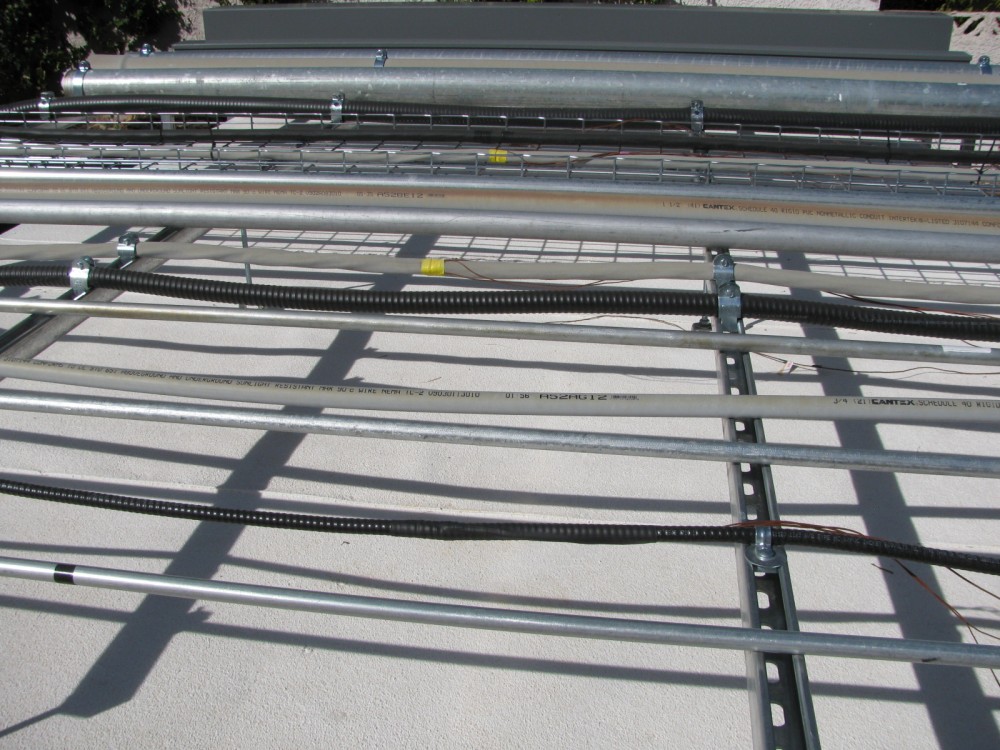
Each roof structure containing the test wiring system measured 3 m (10 ft) long and was mounted between 914 and 1524 mm (36 and 60 ft) from the ground. The ends of each wiring system were capped with surgical cotton to eliminate air flow. The systems were not energized, since the purpose was to determine the temperature within the raceway or cable surface, the ambient under which it operates.
In addition to temperature measurements on the wiring system conductors, the outdoor temperature, wind speed, and solar irradiance were recorded. Temperature measurements were logged at one-minute intervals throughout the day, resulting in 12 recordings hourly. Wind speed and outdoor temperatures were documented using instruments in close proximity to the test samples. Solar radiation was measured on the same plane of the roof surface.
By calculating the difference between the temperature on the wiring system conductors and the outdoor temperature during the period of peak solar irradiance (during selected days of full sun and minimum wind), inferences could be made about the effects of solar heating on these wiring systems. For the purpose of the test, researchers reviewed and analyzed data from a 10-day period in which solar radiation was greater than 1000 Watts for a prolonged time and the wind speed was relatively low.
Results
Statistical data analysis also provided general insights into how solar heating affects all wiring systems when installed on or above a rooftop. For analysis purposes, the 90th percentile of the maximum temperature rise were used. For all wiring systems mounted directly on the roof, the study found the 90th percentile of maximum rise above outdoor temperature would be 16.7 C (62.2 F). For all wiring systems mounted at a distance above the roof (i.e. 12.7 mm [1/2 in.] and greater), the maximum rise above outdoor temperature would be 10.7 C (51.4 F).
These results can be used in determining ampacity corrections required to meet NEC. This has implications when designing electrical systems for industrial, commercial, and other flat-roofed buildings. Cables repeatedly operating above their design temperature for prolonged periods can suffer insulation breakdown and subsequent failure.
The study was important because there is no data on temperatures to which conductors were exposed. The results of this temperature study affect copper and aluminum wiring the same way. While aluminum and its alloy are used for various electrical applications, copper building wire was shown to be efficient, reliable, and economical because of its durability, easy installation and maintenance, and lower lifecycle cost.
The NEC requires ampacity adjustment of wires and cables installed in ambient temperature conditions that are higher than those upon which the listed ampacities of NEC Table 310.15 are based. For conductors in raceways, the ambient to which the insulated conductor is subjected is the air temperature inside the raceway.
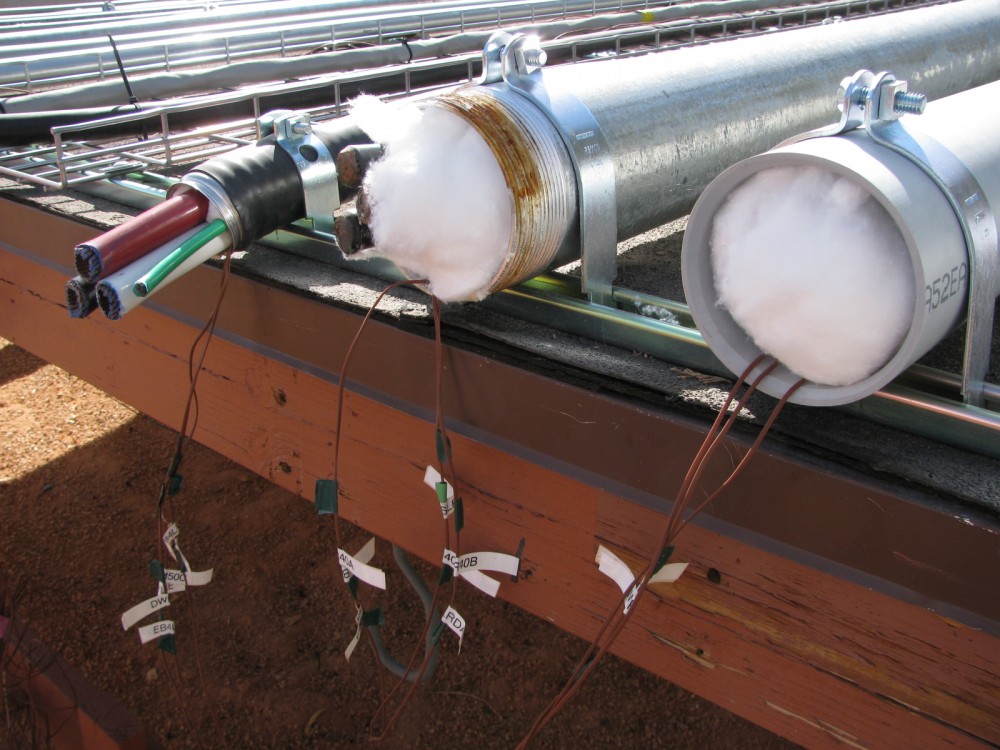
A second round of tests
A year after the first study was concluded on the ampacity temperature adjustments needed for rooftop raceways and cables exposed to sunlight and installed at distances up to 305 mm (12 in.) from the surface, a second test was completed to evaluate modifications necessary for elevations greater than 305 mm.
The additional testing was necessary as an NEC panel rejected part of the code proposal, as supported by the fact-finding investigation report. With the direction and supervision of UL staff, new research was therefore conducted to measure temperature rise for various types and sizes of wiring systems to ensure safe operation. In particular, elevations of 914 and 1524 mm (36 and 60 in.) off the roof were examined.
The results provided NEC additional technical data to eliminate safety concerns with regard to installing wiring systems mounted above 305 mm from the surface of a rooftop. This is vital information for any contractor designing electrical systems on industrial, commercial, and other flat-roofed buildings.
The team providing oversight for the study returned to the original Las Vegas testing lab and thoroughly reviewed all experiments and dates in the same fashion as the study a year earlier. To make similar comparisons, wiring systems mounted 305 mm off the roof were again tested and recorded.
In total, two rounds of testing were performed, with the first phase commencing in June and the second in August and September. In the first round, one roof was painted white (for wiring systems tested at distances of 305 and 1524 mm [60 in.] above the surface), and the other black (for wiring systems tested at a distance of 914 mm [36 in.] above the surface), to make comparisons between the effects of solar reflection and solar absorption.
In the second round, the roof was painted white for the wiring systems tested at distances of 305 and 914 mm. The recorded temperatures were lower than the wiring systems tested at 1524 mm from the white rooftop surfaces. This showed when wiring systems are installed further from the roof, solar reflection becomes more of a factor than the solar absorption.
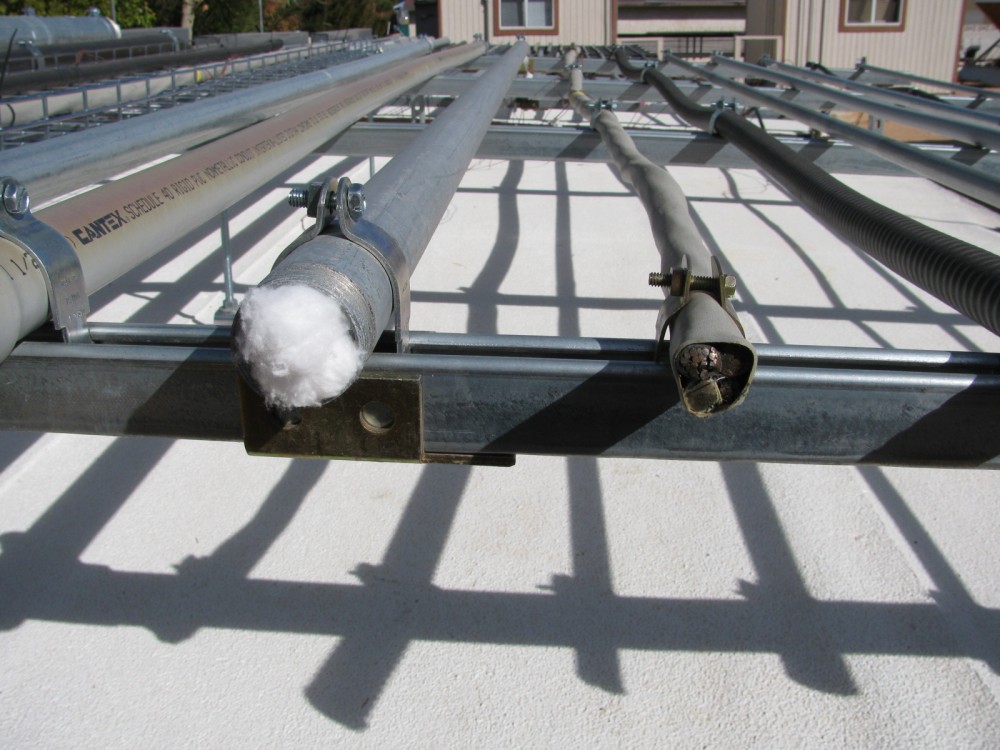
Using similar data analysis techniques, the new testing proved for all wiring systems mounted 914 mm above the roof, the 90th percentile mean temperature rise above outdoor ambient for the time each day where the solar irradiance was greater than or equal to 1000 W/m2 was 1.3 C (34.4 F) with a standard deviation of (3.3 C [6 F]). In this case, the maximum temperature rise above outdoor ambient for all wiring systems mounted 914 mm above the roof with a 95 percent confidence interval would be 7.8 C (46.2 F).
For all wiring systems mounted 1524 mm above the roof, the 90th percentile mean temperature rise above outdoor ambient for the period of time each day where the solar irradiance was greater than or equal to 1000 W/m2 was –1.1 C (30 F) with a standard deviation of (3 C [5.4 F]). In this instance, the maximum temperature rise above outdoor ambient for all wiring systems mounted 1524 mm above the roof with a 95 percent confidence interval would be 4.7 C (40.6 F).
Conclusion
Safe design practice requires adjustment of the ampacity of conductors in direct sunlight, and the study report provides guidance in applying adjustments in the conditions of installation cited.
David Brender is national program manager for the Copper Development Association (CDA). He directs and manages the electrical programs at CDA, including Power Quality Initiatives, research activities, and National Electrical Code (NEC). Brender is a principal member of Panel 5 of NEC, and directs the copper industry participation on four additional panels. He can be contacted via e-mail at david.brender@copperalliance.us.