The air barrier pre-installation meeting
by Corey Zussman
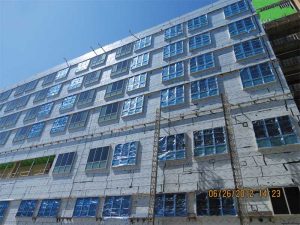
The air barrier installing contractor has sent in their submittal package for review, the building envelope coordination meeting has been held, and installation will begin in a few short weeks. Now, it is time for the air barrier pre-installation meeting where the installation of the specified product is discussed with all contractors associated. It provides the broader team an opportunity for open discussion regarding the air barrier and its complexities to ensure a successful installation.
The air barrier is one of the most significant items on any building exterior. The installation and process should reflect the importance of the system and its intricate installation and integration of non-air barrier system components, such as waterproofing, structural elements, windows, and roofing systems.
The air barrier pre-installation meeting should be designed to:
- review and confirm job-specific product data, shop drawings, and the job-specific quality plan (JSQP);
- review building envelope meeting minutes and contract document details and specifications;
- review and confirm product warranty, testing requirements, and protocols;
- provide a clear understanding of expectations from the installer and adjacent trades;
- review and verify installation sequencing, equipment to be used/logistics, and compatibility of the air barrier and adjacent trades;
- discuss weather concerns, exposure limits, and installation constraints;
- discuss lessons learned from previous projects and experience;
- mockup a description and timetable with building envelope trades;
- provide first work in-place review guidelines; and
- review and verify on-going job site quality control (QC) procedures.
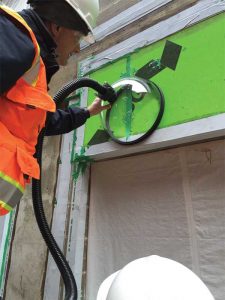
It is essential to review shop drawings and other relevant submittals at this meeting, ensuring that all the product data is submitted and the details are coordinated with the final building plans, taking into account any modifications that might have come with the building envelope coordination meeting and final shop drawings of the adjacent areas. A team should prepare to allocate two to three hours for this meeting depending on the complexity of the project.
The team for this meeting should consist of:
- architect/architect’s on-site observer;
- general contractor–project manager, superintendent/foreperson, and quality team member;
- subcontractor foreperson (a must) as well as the project manager;
- manufacturer representative;
- owner/owner’s testing team;
- optional participants depending on complexity of the project; and
- substrate, waterproofing, window, exterior cladding, and roofing contractor(s).
Crucial moments to consider for cross-contractor communication
The author had a project where the air barrier contractor only submitted the main air barrier components. They did not submit the sealant and primer, which turned out were incompatible with the masonry flashing, resulting in a failure with the systems installed. So, even though some architects do not require the contractor to provide documentation on all components of the air barrier system, it is good practice to submit all items being installed to adequately review the system. Without having each component with updated installation instructions, latest manufacturer technical bulletins, and weather procedures, the air barrier system could be installed incorrectly or have a compatibility issue with adjacent materials.
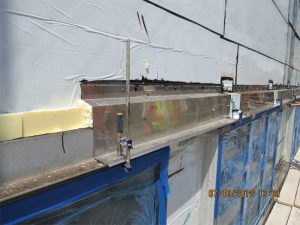
When going into the air barrier pre-installation meeting, the team must be open to hearing the requirements of installation, which are sometimes new to the installer, for the exact product and procedure that is being installed or installed adjacent to the air barrier. Having an open mind is imperative for a successful meeting. Treat each meeting like it is the first time these products and adjacent components are being installed. Adopt the mindset that materials change over time; installation instructions will be modified periodically by the manufacturer to include updated concerns and information from the field on other projects. As well, adjacent materials are typically different on every project.
Even if this is a Phase II installation, having a new pre-installation meeting with the same intense scrutiny as the first meeting, the team will learn from Phase I lessons learned and make sure the manufacturer, architect, and other subcontractors have not changed materials or procedures. The author recently had a project where the discussion revolved around installing the liquid air barrier with rollers; even the mock-up was installed with a roller. When it was installed on the building, spray equipment was used, creating issues with the installation that were never addressed. Therefore, always make sure the specific installation procedures are discussed and agreed upon. An installer having no experience with a new product happens often and so it is important to identify this early before installation mistakes occur. One of the first questions to review is ensuring the installers have installation experience with the specified product or system on the same type of construction and weather conditions. The air barrier contractor could have a great deal of experience with the manufacturer and similar products, but not this specific installation. Also, getting ‘lessons learned’ from the entire team and identifying top concerns for the installation will help set the agenda and make sure all questions get identified and answered during the meeting.