Reviewing for compatibility and adhesion
Compatibility and potential adhesion concerns of adjacent non-system products should always be reviewed and confirmed. Having a chart of compatibility at the meeting, as well as the manufacturer’s technical bulletins on compatibility, will provide the team with a good understanding and give direction on what needs to be verified before the start of installation or the sequence of installation of materials. One item to review for compatibility and adhesion is fireproofing. In some cases, one may see fireproofed beams, and floor deck extends out as a soffit. Typically, air barrier cannot be applied over fireproofing, which creates a condition where one might need to add a soffit to apply the air barrier. Fireproofing is rarely discussed in the air barrier manufacturer’s manuals and often missed during the initial review of construction, which is why it is important to assess all the architectural details, including the plans identifying such installations.
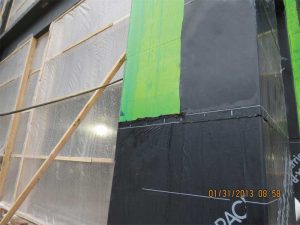
When reviewing for compatibility, the team should consider the substrate to which the products are being applied, including the sheathing product, requirement for the concrete finishing, and the masonry mortar joints. These items should be reviewed to make sure the corresponding contractor is aware of the finish expectations as soon as possible.
Protecting the air barrier is important. Define how many days of exposure are acceptable for the air barrier material. It is also useful to understand the project size and what cladding material will be installed in front of the air barrier system. There will likely be some lag between a masonry 10-story building if the entire building is installed with air barrier. Sequencing the timing of the air barrier to better correlate with the masonry installation would reduce the exposure time of the system. Protection should also include substrate before the installation of the air barrier. Some questions to consider include:
- how is the team going to keep the masonry dry on the backside before the installation of the air barrier;
- what procedures will be taken at the top of the parapet at the backside of the roofline to prevent moisture from getting into the system; and
- who is going to maintain the protection after rain or snow.
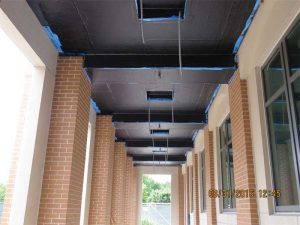
Finally, once the building envelope is complete, there are still a few items to be reviewed to maintain air barrier integrity. Signage installation, which typically follows the completion of the building envelope, should be identified. Notes and procedures should be documented and given to the final trades, such as the signage contractor and the owner so they understand the system installed behind the cladding and how to accommodate their installation without compromising the integrity of the air barrier system installed.
During the meeting, notes and details will be taken and will need to be followed up on by different parties. A responsibility matrix should be made to make sure all items are properly addressed over the coming weeks.
Among the most significant challenges installers see today is the use of different materials with uncertain compatibility to form a durable and continuous air barrier. It takes a team to properly review and confirm installation of an air barrier system. Having the opportunity and taking the proper amount of time ahead of initial installation to discuss these and other cladding challenges are key to a successful air barrier installation.
A forensic architect registered in several states, including Wisconsin, Corey Zussman has been practicing in the construction industry for more than 30 years. He specializes in building envelope, restoration, preservation, life safety and interior finishes. While working on an average of 50-75 projects a year, Zussman conducts constructability reviews, pre-installation meetings, comprehensive envelope meetings and construction observations. He has also become known for providing educational opportunities in the industry and has produced more than 150 “lessons learned” papers. Topics include building envelope and life safety concerns, enabling Zussman to proactively address issues during design review, pre-construction and construction.