SPECIFICATIONS
by Juste Fanou
The terms ‘air barriers’ and ‘vapor retarders’ (or ‘vapor barriers’) are perhaps some of the most poorly understood concepts in the construction industry. Most building professionals know they are needed, but often struggle to locate them correctly within wall assemblies. Also, the consequences of installing these materials improperly can result in failures. This lack of understanding of the functions of these assemblies has resulted in simplistic rules-of-thumb prone to misapplication (e.g. the vapor barrier is always on the inside and the air barrier is always on the outside). As manufacturers introduce materials with new properties and attempt to push the boundaries of building envelope construction, it is crucial the industry agrees on terminology for communicating the specific functions and purpose of these materials to avoid confusion and costly errors. In this regard, the term ‘air/vapor barrier’ is misleading and should be replaced with more appropriate terminology.
A brief history
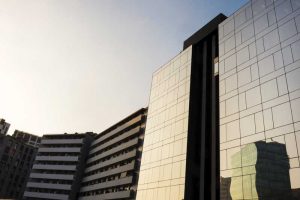
Initial attempts to increase the thermal comfort of occupants in modern North American wood-framed construction date back to the 1800s. The introduction of ‘building paper’ in the form of asphalt-impregnated felt—also known as sheathing membranes or weather-resistive barriers (WRBs)—represented an early effort to reduce wetting of wall assemblies and air leakage (Refer the 2017 book Building Materials: Product Emission and Combustion Health Hazards written by K. Hess-Kosa). The industry made further advancements in the field of envelope performance in the 1930s with the rise of insulation in framing cavities and attics (For more information, read the article, “Heat, Air and Moisture Control in Walls of Canadian Houses: A Review of the Historic Basis for Current Practices,” by M. Koniorczyk and D. Gawin, published in the April 2008 issue of Journal of Building Physics). However, the undesirable effects of moisture in insulated cavities soon surfaced. The traditionally painted wood façades began to suffer from peeling, blistering, and other coating failures. As is the norm in the building industry, a ‘blame game’ quickly ensued with insulation manufacturers blaming the paint producers and vice-versa, while the building paper manufacturers were caught in the middle (Consult the paper, “The rise of the diffusion paradigm in the US,” by W.B. Rose, published in the 2003 book, Research in Building Physics: Proceedings of the Second International Conference on Building Physics, edited by G. V. J. Carmeliet, H. Hens, and G. Vermeir). It was not until the late 1930s that scientists began investigating moisture movement in building assemblies. Their findings—considered controversial or even biased by some—concluded the transfer of water vapor by diffusion (a process explained later in this article) was responsible for the paint peeling off the siding (Many argue Frank Rowley’s theory of vapor diffusion, which led to the introduction of vapor barriers in wall cavities and ventilated attic spaces, was not grounded in sound science. This study is considered biased by many in the field, because it was funded by the insulation industry as a way to defend itself against claims insulation was responsible for condensation in cavity spaces and peeling paint). These conclusions resulted in regulation that mandated the use of low-vapor permeance membranes in construction projects in the early 1950s. It was the birth of the ‘vapor barrier,’ and the industry celebrated its solution to the moisture problem by lining walls with polyethylene (PE) plastic. Ostensibly the issue of peeling paint was resolved, or at least it seemed so.
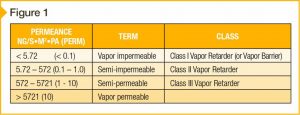
Image courtesy J. Lstiburek
Nonetheless, moisture problems persisted. Further research in the mid-1980s suggested that uncontrolled air infiltration, and not vapor diffusion, was the largest contributor to moisture accumulation in cavity spaces. However, by that time the popularity of the now ubiquitous ‘6-mil poly’ inspired methods to seal the already familiar vapor barrier. The purpose was to turn it into an effective air barrier.
These attempts to seal the vapor barrier may be characterized as the genesis of the ‘air/vapor barrier,’ both as a concept and term. Conceptually, the ‘air/vapor barrier’ was a material purported to address both air infiltration and vapor diffusion issues. Its proponents believed in sealing the joints of PE sheets to create a dual-purpose material ascribing the additional properties of air infiltration control to the already popular ‘6-mil poly.’ This popularity was perhaps responsible for its great appeal and wide adoption in the industry. As time passed, however, the idea of ‘sealing PE was quickly abandoned, and construction practitioners explored other materials to provide airtightness. It was clear PE was not a sufficiently durable material to resist the effects of wind gusts and pressures. Moreover, this lack of durability was further undermined by the intrinsic difficulties associated with installing PE in a continuous fashion.
Even if the concept of the PE ‘air/vapor barrier’ slowly faded, the term continued to be used. Coincidentally, as time passed it also appeared as if the general understanding of the functions of these air and moisture control elements was further clouded by this conflated term. These once-distinct materials slowly transformed into abstract dotted lines everyone knew were required on construction details, but no one fully understood where or why.
No doubt, improper use of terminology can be a big problem in communication about construction detailing, just as it can be about other aspects of our industry such as BIM and general computer-related issues. As a senior architect, I strive to use and educate others on the proper terms to address what we are implementing and what we are learning about. In this case, I do take issue with the chart that compared architects’ understanding of some of those terms to engineers’ as I would like to think our profession is on a little higher level of knowledge than what that figure implies. Thank you very much for this good contribution to the discussion!
There are still some controversy about the location of the water resistive barrier (WRB) in an exterior wall assembly when a continuous insulation (ci) is used. There are some wall systems that suggest the installation of the WRB behind the (ci) and over the exterior sheathing. In the other hand other exterior (ci) wall systems included an integral aluminum foil at the interior and exterior faces of the (ci) using the exterior face as both, WRB and air barriers, when the seams and penetrations through the (ci) are properly sealed. The exterior aluminum foil face become the drainage plane of the wall assembly. This wall assembly in many instances does not even require installation of any exterior sheathing. The only other topic that requires attention is the exterior wall dew point calculations to determine if a vapor barrier is required or not and where is the correct location. Agreed, terminology may create issues, but in many cases all different approaches to install (ci) make this topic even more complex.
Thank you very much for this detailed content on air and vapor barrier. A useful and great content, your blogs are always great and I love reading them. This is a really informative article to share. Keep posting more. Well, I have visited another site moisturebarrier.co.nz having some wonderful and similar information.