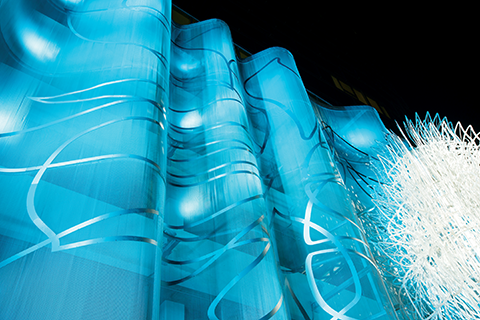
by Andrew Schoenheit
Some of the most attention-getting projects these days involve architectural coiled-wire fabric—a more affordable alternative to traditional woven mesh that delivers equal or superior aesthetics, as well as functionality and performance.
Traditional woven mesh is usually made from stainless steel, copper, or brass. It is handcrafted on industrial looms, custom-made, and found in both interior and exterior applications. It is often used as a design element, space divider, or exterior cladding—and is a heavyweight, durable product suited for large-scale projects.Woven mesh can shield windows and openings while still allowing air to flow through without completely obstructing views.
Architectural coiled-wire fabric, on the other hand, looks and performs in the same manner, but comes with a far lower installed cost made possible by its unique design: interlocked strands of wire shaped into a coil form. This spiraling imparts it with structure and spring-like characteristics that allow for greater degrees of tensions and compression without permanent deformation.
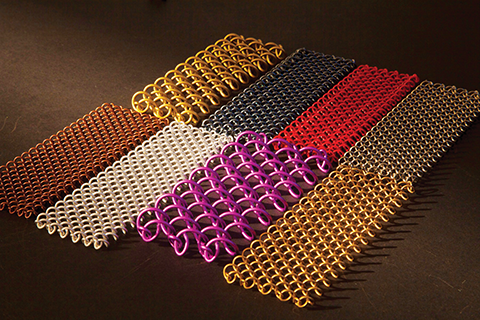
Why go coiled?
Architectural coiled-wire fabric systems can serve numerous functions, from diffusing light and aesthetic impacts to fall protection, screening, ventilating, and security. Interior applications appropriate for these assemblies include:
- media walls;
- barriers;
- ceilings;
- merchandising displays;
- partitions;
- curtains;
- security screens;
- infills;
- signage; and
- light diffusers.
Exterior applications include:
- awnings;
- living walls;
- canopies;
- claddings;
- partitions;
- curtains;
- façades; and
- water features.
In comparison to traditional woven mesh for the same applications, these assemblies are much lighter and have reduced structural embed requirements. The fabric is manufactured in
a wider range of metals, gauges, scales, finishes, and colors; further, its manufacturing method allows for panel sizes with unlimited width and
a coil length limited only by shipping restrictions.
Coiled-wire fabric provides color and texture, and reacts beautifully to light. Many architects and designers are embracing these systems, especially for the fact they—along with their engineered attachment systems—enable even projects with modest budgets to achieve unique design visions.
Traditional woven metal mesh
As for woven metal mesh, there are two broad types: rigid and flexible. Rigid (or flat) mesh contains wires running in the warp direction, combined with wires inserted in the fill direction. The material obtains its stability via the friction created between the warp and the fill, typically by a crimp created where the wires intersect. Any shape integrated into the material would be created via forming or bending. Fabrication is normally required to finish off the edges of the material, and there is more frequently a frame required around the perimeter. There are typically length and width limitations driven by the loom sizes.
There are two types of flexible woven mesh products. The first is fabricated via cable strands (running in the warp direction) connected to rods sitting between the cable strands. The other takes wire and forms a flat spiral which is then interconnected (typically via welding) with rods. These systems typically have length and width limitations determined by the tooling used in the manufacturing process. The material is flexible and can be bent or formed in one direction that is limited by the way the material is oriented.