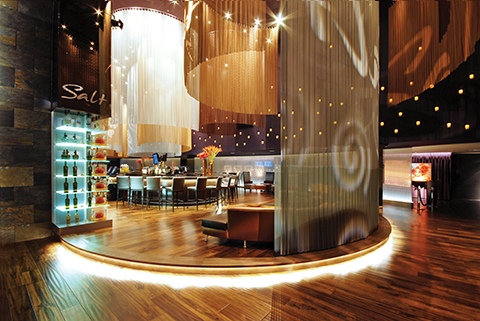
Reducing complexity and consumption
The U.S. Courthouse in El Paso, Texas, provides a telling example of how architectural coiled-wire fabric differs from traditional woven mesh. The building’s shimmering, multi-panel assembly adds intricate texture in keeping with the architect’s mission to mirror the local history and geology.
“One of the primary materials in the building is copper, so the system allowed us to use that material to shade the large expanses of glass near the building entry,” says Paul Fehlau, executive senior associate at Antoine Predock Architect Studio (Albuquerque, New Mexico). “It is not as rigid, and it is simpler.”
Fehalu further explains what he means by simpler.
“It hangs like fabric and has a very distinctive three-dimensional aspect that you really cannot get with woven meshes,” he says. “This allows you to suspend it from the top with a very simple detail and just let it drape, as compared to meshes that need additional support to keep them in place. There really isn’t anything else like it.”
Aesthetics aside, another advantage to installing architectural coiled-wire fabric is its positive impact on a building’s energy consumption through passive solar shading. As demonstrated by third-party engineering tests conducted by Interface Engineering (Portland, Oregon), coiled-wire fabric assemblies in exterior applications can reduce a building’s energy consumption by as much as 12.3 percent.
The testing also determined the coiled fabric system “significantly” improves thermal comfort when used as an exterior scrim in conjunction with standard-performance double-pane glazing. Further, the study found the system reduces direct sun penetration even in zero percent fullness mode.
The working definition of ‘fullness’ here is a measurement of the extra material needed to cover a given area when it is wave formed. A flat panel of coiled-wire fabric has zero percent fullness; a panel twice as wide as the area it covers has 100 percent fullness. Interior window curtains often employ increased fullness to increase shading, energy savings, and glare control.
It is also worth noting architectural coiled-wire fabric systems are 100 percent recyclable and part of the Living Building Challenge (LBC) Declare labeling program, which calls itself “the built environment’s most rigorous performance standard.” Demanding full materials transparency, it calls for the creation of building projects at all scales to operate as cleanly, beautifully, and efficiently as “nature’s architecture.”
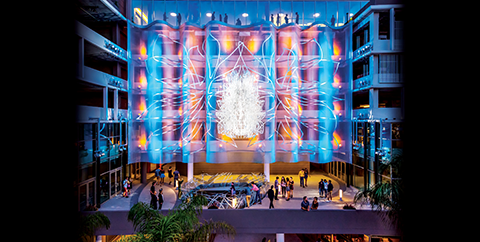
Material options
The options to specify this metal fabric begin with the selection of wire materials. Except where noted, all these materials are usually available in a wide range of wire gauges and scales.
Low-carbon, mild steel
Low-carbon, mild steel wire with a semi-bright finish boasts relatively high strength and durability, along with a lower price point. The wire conforms to ASTM A82, Standard Specification for Steel Wire, Plain, for Concrete Reinforcement, and can be painted almost any custom color. It is also available from some manufacturers in a softened, annealed version. The annealing, or stress-relieving process, reduces the wire hardness, making it more ductile. The wire has a smooth, bright finish with low memory, making it ideal for high-speed forming.
Galvanized steel
Galvanized steel wire is a mild steel wire with a layer of zinc applied during the wire drawing process. The zinc coating adds a protective, corrosion-resistant layer to the steel conforming to ASTM A641, Standard Specification for Zinc-coated (Galvanized) Carbon Steel Wire. Galvanized wire retains all the mild steel’s mechanical properties with a high resistance to atmospheric oxidization. The wire is ash-gray in color, but can form a white powder when wet. This wire works best for industrial applications, where relatively high strength and corrosion resistance are required.
Aluminum 5056–H18
Aluminum 5056−H18 is an ideal material for the coiled-wire fabric-weaving process. It features ease of formability, high resistance to corrosion, excellent strength-to-weight ratio, and natural aesthetic qualities. This aluminum wire is very ductile, making it relatively inexpensive to manufacture. Being non-ferrous, the material does not discolor or deteriorate in most climates.
At almost a third the weight of steel, aluminum weaves can cover more area while adding minimal mass to its supports, which further decreases the overall cost. In its bare state, aluminum wire is light silver in appearance, but can be painted any custom hue. Additionally, it can be polished to create a more lustrous finish.