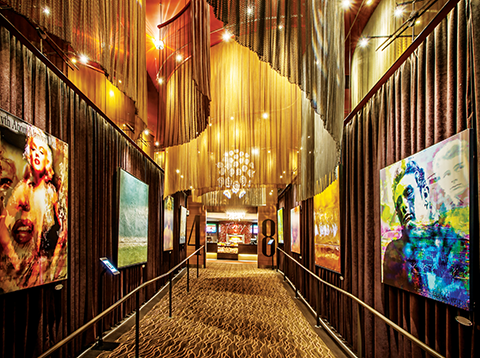
Aluminized steel
Aluminized steel wire is a corrosion-resistant steel material used primarily for exterior fencing. It is a cheaper, less-attractive alternative to stainless steel with a slightly duller finish and conforms to ASTM A809-08, Standard Specification for Aluminum-coated (Aluminized) Carbon Steel Wire. Typically, this is only available in specific scales.
Nickel-plated steel
Nickel-plated steel wire is standard mild steel wire coated with a thin layer of electrolytic nickel. The coating not only offers a brilliant chrome finish, but also helps in resisting corrosion. Typically, this material is used on interior applications where a high-gloss mirrored finish is desired.
Stainless steel
Stainless steel Type 304 is a slightly magnetic, highly corrosion-resistant material with a lustrous metallic finish. Its consistent wire surface quality, relatively high strength, and great corrosion resistance make it attractive for many applications. The wire can be drawn bare or with a black oxide surface. Stainless Steel Type 304 conforms to ASTM A313, Standard Specification for Stainless Steel Spring Wire.
Stainless steel Type 316
Type 316 exhibits the highest level of corrosion resistance when compared to all other stainless steel types. It has a slightly higher strength than Type 304 and can handle higher temperatures. In most cases, Type 316 is used for all exterior applications where relatively high strengths and high resistance to oxidation or eroding is required. The wire can be drawn bare or with a black oxide surface. In its bare state, Type 316 has a lustrous metallic finish. Additionally, the wire can be chemically treated to exhibit an ultra-black satin finish that metallically bonds to the stainless wire and does not deteriorate. Stainless steel Type 316 conforms to ASTM A313.
Silver tin-plated steel
Silver tin-plated steel wire is a mild steel wire with a shiny, brilliant silver tin-plated surface. The tin coating is Grade A and conforms to ASTM B339, Standard Specification for Pig Tin. Its relatively low cost and attractive finish make it a popular choice for interior draperies and the like.
Solid brass wire
Solid brass wire bears a natural golden color. Its alloy composition is 70 percent copper and 30 percent zinc, and is denoted as “half hard.” As bare wire, brass has a relatively high resistance to corrosion, but can oxidize over time. A clear-coat finish can be added to preserve its natural color if desired. The wire’s anti-magnetic and anti-spark properties, coupled with moderate tensile strength, make it a unique material for special applications. This material conforms to ASTM B36, Standard Specification for Brass Plate, Sheet, Strip, and Rolled Bar, and is typically available in just a select set of wire gauges and scales.
Copper-clad steel
Copper-clad steel wire is a mild steel wire with pure copper plating bonded to the wire’s surface. This wire material exhibits a brilliant-red, polished finish when first plated. However, if left bare and untreated, the wire’s appearance will slowly change to brownish hues before ultimately gaining a gray/green patina. By applying a thin layer of clear lacquer, the bright salmon color can be maintained if desired. Suitable for both interior and exterior applications, this wire conforms to ASTM B227, Standard Specification for Hard-drawn Copper-clad Steel Wire.
Solid copper
Solid copper wire, like copper-clad steel wire, exhibits a vibrant reddish color when first drawn, but slowly browns to a gray/green patina when left bare and untreated. A clear-coat finish can be added to preserve its natural color if desired. Copper wire has a considerably low tensile strength and is soft, conforming to ASTM B248, Standard Specification for General Requirements for Wrought Copper and Copper-Alloy Plate, Sheet, Strip, and Rolled Bar. This material is primarily used in ornamental indoor applications.
High-tensile-strength steel
High-tensile-strength steel wire (i.e. music wire) is a high-carbon, cold-drawn wire conforming to ASTM A228, Standard Specification for Steel Wire, Music Spring Quality. Its tensile strength ranges from 2172 to 2380 MPa (315 to 345 ksi) and comes bare, zinc-plated, or phosphate-coated. The wire is primarily used in applications requiring high tensile/shear strength, wear resistance, and fatigue strength. It can be painted almost any color, but due to its extreme hardness, can only be woven in certain wire gauges and scales.
Titanium
Titanium wire is used primarily in the chemical industry where extreme lightweight, high corrosive resistance, and low to moderate strength are required. It is available in several different grades—all governed by ASTM B863, Standard Specification for Titanium and Titanium Alloy Wire. In its natural state, titanium wire is a dark-silver color. Its specific physical and chemical properties make titanium a particular material type and can only be woven using certain wire gauges and in a few scales.
Good engineering saves time and money
The weaves for architectural coiled-wire fabric panels tend to share the same fundamental geometry, created by interlocking individual strands of spiraled wire. Various scale scan be chosen, but the thickness selection impacts the material’s:
- percentage of open area (from 40 to 85 percent);
- textured appearance;
- scale (from to 2.4 to 16 mm [3⁄32 to 5⁄8 in.]);
- wire gauge (from 14 to 21); and
- ultimate strength.
The process of specifying includes the selection of an engineered attachment system to install coiled wire fabric. A designer should be able to rely on the manufacturer’s judgment to specify the most appropriate one for any particular project.
Andrew Schoenheit is vice president of sales for Cascade Architectural, manufacturer of Fabricoil coiled-wire fabric systems, and a division of Cascade Coil Drapery Inc. He has more than 15 years of experience in the wire-forming industry including extruding and production, metallurgy, metal finishing, and coatings. Schoenheit is also highly involved in Cascade’s research and development, including projects in material testing for tensile and shear, bulk properties, blast and shock tube testing, and analytical modeling of formed-wire materials. He can be reached at andrew@cascadecoil.com.