by Rick Duncan, PhD, PE
Use of sprayed polyurethane foam (SPF) insulation has steadily become more widespread. Used in residential and commercial structures of various types, SPF is a high-performance option for the building envelope. When applied in ceilings, walls, and floors, the material boasts numerous benefits, including ease of installation, durability, energy efficiency, and improvements in indoor air quality (IAQ).
The rise in the use of SPF, coupled with the onsite procedures for mixing the chemicals comprising the foam and applying the material to the structure, has increased the need for education and installer certifications to ensure best practices and product performance.
Industry leadership, including the Spray Polyurethane Foam Alliance (SPFA), are committed to providing installers with the knowledge and programs that help ensure success and safety. This two-part web series highlights the benefits of SPF in insulation applications, and outline technical descriptions for the product’s proper and safe installation.
Sprayfoam in insulation applications
As an insulation material, SPF boasts both versatility and durability. Due to its light weight, installation is easy. It can also lend increased strength to the building envelope, and once installed, requires no maintenance. Among its many benefits, SPF can be used across all geographic regions and climates.
The material provides thermal, air, moisture, and sound barriers. SPF enhances and maintains the structure’s interior comfort. These barriers protect the structure against mold and water damage, maintain indoor temperatures for dramatically reduced energy costs, and even lower the amount of allergens and pollutants able to enter the structure and disturb residents.
All types of SPF develop a fine network of cells that create pockets of still air (i.e. open-cell SPF) or insulating gas (i.e. closed-cell SPF). Unlike fibrous insulations, the fine cellular structure renders the material impermeable to air movement, providing consistent thermal performance over a wider range of temperatures; this qualifies SPF as an air-barrier material at typically installed thicknesses. An air barrier is defined as a material with an air permeance of less than 0.02 L/(s•m2) at a pressure differential of 75 Pa, as per ASTM E283, Standard Test Method for Determining Rate of Air Leakage Through Exterior Windows, Curtain Walls, and Doors Under Specified Pressure Differences Across the Specimen, or ASTM E2178, Standard Test Method for Air Permeance of Building Materials. As an air-barrier material that forms and adheres in place, SPF can substantially seal the building envelope from energy-robbing air leakage, infiltration of pollutants and allergens, and unwanted noise.
Closed-cell SPF adds additional benefits to the building envelope. Closed-cell SPF is water-resistant, and is resilient to moisture movement in the material. It can be used in damp or wet areas such as basements and crawlspaces. At a thickness of about 25 mm (1 in.), closed-cell SPF meets building code requirements for a Class II vapor retarder by having a moisture permeance of less than 1.0 perm per Method A of ASTM E96, Standard Test Methods for Water Vapor Transmission of Materials, as required in colder climates. In addition to moisture resistance, the ridged cellular structure and tenacious adhesion of closed-cell foam can add structural strength to framed buildings. Closed-cell SPF sprayed between stud cavities of framed walls can achieve racking strengths exceeding 2267 kg (5000 lb) per ASTM E72, Standard Test Methods of Conducting Strength Tests of Panels for Building Construction, which is close to that of certain wood sheathings. Closed-cell SPF under a roof deck can withstand Category III hurricane winds, while also providing a secondary water barrier if the roof shingles are lost.
Since insulation performance is not measured by one factor alone, the assembly’s success is properly assessed by reviewing combined considerations for air movement, moisture control, health, safety, durability, comfort, and energy efficiency.
The International Building Code (IBC) recognizes the ASTM tests in Figure 1 to measure the performance of building products like SPF.
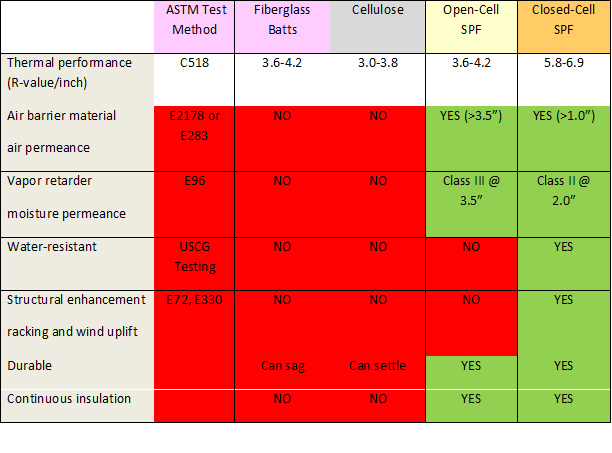
Proper foam installation
The benefits of SPF are optimized with the product’s safe and proper installation. As SPF is essentially formed onsite during installation, there are specific guidelines, techniques, and measures that need to be taken to maximize the product’s lifetime performance and to ensure safety for both the installer and structure end user.
These include:
? care of equipment;
? maintaining proper temperature of materials during storage;
? safety precautions and formal attire;
? surface evaluation;
? selection of appropriate products;
? preparation and priming; and
? installation of protective coatings and coverings.
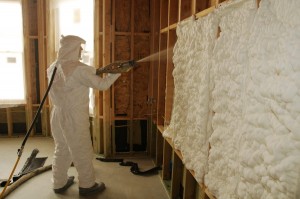
Equipment care
The care of professional SPF installation equipment is imperative to ensure the material’s safety, proper installation, and optimal performance. Regular inspection, cleaning, and repair are essential for installation equipment. Likewise, the proper storage and maintenance of the equipment is critical to ensuring it works properly and effectively.
Contractors should have a supply of spare parts in each vehicle to minimize downtime should equipment failure occur during foam insulation installation. A spare parts inventory should include spray-gun parts (or a backup gun), extra hoses, a second set of drum pumps, and key wear-parts for the proportioner, compressor, and generator.
A high-pressure SPF system is typically used for installation of insulation and roofing systems. This equipment, along with SPF chemicals, is transported to the jobsite in a box truck or large utility trailer.
Maintain proper material temperatures
Sprayfoam chemicals must always be stored within the manufacturer’s suggested temperature range. Storing product outside of these temperature parameters can lead to a reduced shelf life, making the product difficult to apply correctly. During installation, proportions should be set to the manufacturer-recommended temperatures and pressures to produce ideal SPF. Properly stored SPF chemicals typically have a six-month shelf life.
Safety precautions and attire
SPF is formed on the jobsite by mixing equal volumes of two liquid components: the ‘A-side’ and ‘B-side.’ The ‘A-side’ contains polymeric isocyanates (pMDI), while the ‘B-side’ consists of proprietary blends of polyols, blowing agents, catalysts, fire retardants, and surfactants. Manufacturers of high-pressure SPF often provide a set of A-component and B-component as a pair of 208-L (55-gal) drums. A typical drum set produces about 10 and 32 m3 (4000 and 14,000 board feet) for closed and open cell SPF insulation, respectively.
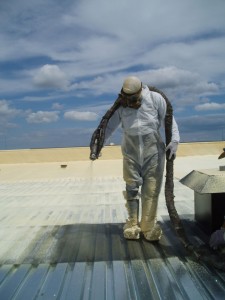
Consideration must be made to protect against contact with chemical vapors and aerosols from SPF developed during and shortly after application. It is imperative appropriate protective measures be employed to minimize the risks associated with exposure through inhalation, skin, and eye contact. These measures include spray zone containment, adequate ventilation during installation, safety training for all those involved, personal protective equipment (PPE) for the full duration of the install, and a medical surveillance program for field crews.
PPE for chemical protection includes a full body suit and headsock covering skin, along with nitrile gloves, and eye protection. Respiratory protection for interior insulation requires use of a supplied air respirator (SAR). In accordance with Occupational Safety and Health Administration (OSHA), all insulation contractors, like any other construction trade, must employ proper fall protection as well as safety programs that include using ladders, scaffolding, and working in confined spaces like attics and crawlspaces.
Additionally, overspray from SPF insulation applications must be controlled to prevent it getting on unintended surfaces. Finished surfaces, as well as window glass, need to be properly covered and masked to prevent damage from overspray.
Rick Duncan, PhD, PE, is the technical director of the Spray Polyurethane Foam Alliance (SPFA), an organization representing contractors, material and equipment manufacturers, distributors, and industry consultants active in the SPF industry. Before joining SPFA in 2008, Duncan held the positions of senior marketing manager for Honeywell’s SPF business and global program director for Certain Teed/Saint-Gobain. He holds a PhD in engineering science and mechanics from Pennsylvania State University, and is a registered professional engineer in the state. Duncan can be contacted by e-mail at rickduncan@sprayfoam.org.
Good analysis. Sprayed polyurethane foam (SPF) insulation is better in all though I would highlight water resistance as the most crucial of all.
Spraying is the easiest way for spraying something without affect human body and also it spread the liquid even.
It sounds like SPF is able to boast to versatility and durability. I’ve heard spray foam insulation is actually better than using batting. Though it sounds like this application method needs to be done by a professional if you want to prevent it from getting on unintended surfaces.