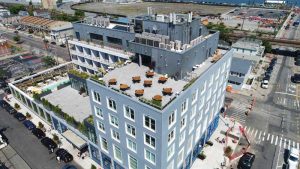
Carbon-reduced, high-quality zinc to address the carbon footprint
As a natural metal, zinc is the 24th most abundant element in the Earth’s crust and the fourth most used metal in the world.5 The International Zinc Association (IZA) estimates the world’s zinc use at 20 million tonnes (19.6 million tons) per year. Both mining and recycling are necessary and available to meet anticipated zinc demands. Globally, 12.8 million tonnes (12.6 tons) of zinc are mined and 7.6 million tonnes (7.6 tons) recycled annually.6
Mining, extracting, and refining metals can be an energy-intensive process. As material demands and energy costs rise, energy-efficient production maximizes both economic and environmental resources. Since zinc has a low melting point of 418 C (784 F), it takes less energy to process it than other metals and materials. For comparison, aluminum melts at 660 C (1,220 F) and steel at 1,370 C (2,500 F).
A recent study calculated 65 percent of zinc production’s carbon footprint could be attributed to smelting. Choosing zinc manufacturers that have minimized their already low carbon footprint is one more step toward reducing overall GHG emissions.7
For architectural applications, raw zinc material is smelted, cast as a material of uniform and certified quality, and wound as a coil in one continuous operation. Rolled zinc sheet is produced by alloying special high-grade (SHG), 99.995 percent pure zinc with minute quantities of copper, titanium, and aluminum. The alloy composition provides the material the necessary strength, while allowing the architectural product to be easily shaped.
IZA provides practical guidance on calculating the carbon footprint for SHG zinc, in compliance with the International Organization for Standardization (ISO) 14040 and 14044, and the Product Life Cycle Accounting and Reporting Standard by GHG Protocol.8 As a global average, the IZA calculated the carbon footprint GWP for primary SHG zinc production to be 3.64 kg (8.02 lbs) CO2eq per 1 kg (2.2 lbs).9 Many IZA member companies have committed to climate change policies to reach net-zero Scopes 1 and 2 GHG emissions by 2050. An increasing number also are working on Scope 3 targets.10
One IZA member has further lowered the carbon footprint of its SHG zinc product to achieve a 100-year GWP of 1.85 kg (4.08 lbs) CO2eq per 1 kg (2.2 lbs).11 This savings was gained through energy-efficient production practices that rely on electricity largely generated from renewable sources, including water and wind power. In addition, its product uses recycled zinc material. This investment reduced the product’s impact by 54 percent and saves more than 36,000 tonnes (3,5431 tons) of CO2eq each year, equivalent to the GHG emissions of a small town with 5,400 people. Quantifying this to size and area, a standing-seam roof would have 12 kg (26.5 lbs) CO2eq. This low-carbon architectural zinc material is now available in North America.