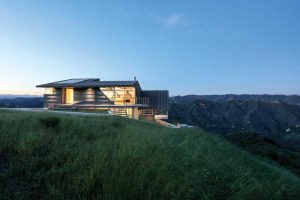
Composition, patination, and installation of architectural zinc
In North America, ASTM B69-21, Standard Specification for Rolled Zinc, is the primary reference document for type 1 and type 2 architectural rolled SHG zinc alloys and their expected characteristics.12 The zinc alloy composition determines the metal’s coloration. Type 1 tends toward blue-gray and type 2 contains slightly more copper (0.80-1.00 percent), which produces more of a graphite-gray coloration.
Untreated, architectural-grade zinc looks bright and shiny, and is light reflective. Over time, a natural matte patina develops, creating a dynamic appearance as the material ages. A patina’s formation is the process of zinc carbonate “freckles” gradually growing together. The rate of its formation is related to the slope of the surface. The patina will form more slowly on a vertical wall surface than on a slightly pitched roof. The patination speed varies between six months and five years or more, depending on climatic conditions. The more exposure to wetting and drying cycles, the quicker the patina will develop.
Some manufacturers offer pre-weathered zinc material that accelerates the patina formation under controlled conditions. Factory-finished options are also available to achieve an initial, uniform aesthetic. Typically, these finishes are painted or phosphate architectural coatings applied in the factory under environmentally controlled conditions.
Architectural zinc coils are unwound, cut, and fabricated into panels, tiles, and other formed exterior and interior architectural products. Sheets also can be perforated and fashioned into ornamental accents. Since zinc is a lightweight material, it can help reduce the structural load and associated materials on a building.
Qualified contractors can install zinc products as wall cladding and facade systems; on low-sloped, steep-sloped, flat, and mansard roofs; and as hip and ridge caps, drip edges, alleys, step flashing, dormers, cupolas, parapets, gutters, downspouts, and more. Fabricators can also customize seam profiles to the project’s requirements.
Meeting building projects’ sustainable goals, contractors, fabricators, and installers provide high-performance, low-carbon product solutions. Some are considering the environmental impact of their own practices. Federal agencies and other AHJs can require reports for operational, transportation, and equipment GHG emissions; “buy clean” energy and material sourcing, recycling, and landfill waste streams.