by Robert C. Haukohl, PE, and Colin P. Rueb, PE
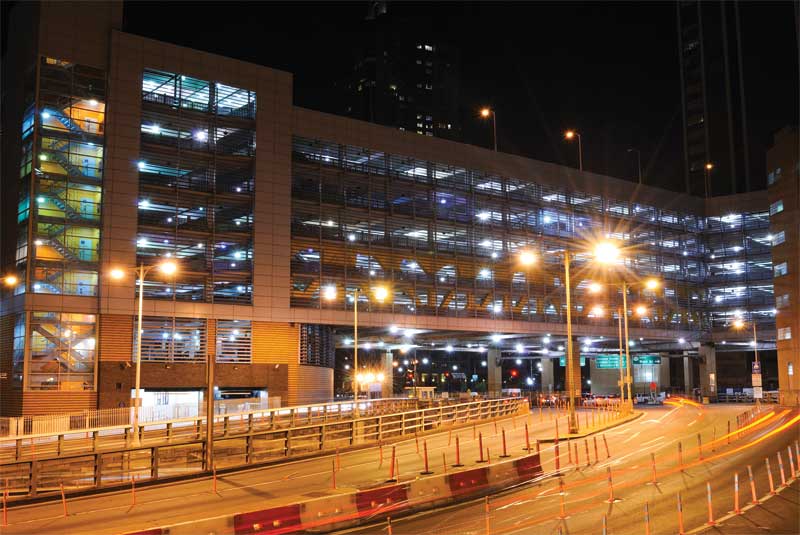
Photo © BigStockPhoto.com
Concrete slab pour 1B was supposed to be routine, occurring early in the construction of a parking garage in the Midwest. However, low compressive strength issues led to lengthy and costly project delays, as well as some interesting theories about the causes.
Due to its extensive use as a construction material, ready mixed concrete is intensively studied and tested. The American Concrete Institute (ACI), ASTM International, and the American Association of State Highway and Transportation Officials (AASHTO) have well-established standards covering mix design, batching, transporting, testing, pumping, placing, finishing, curing, performance, and even forensic investigation of concrete. Yet, sometimes strange things happen with a batch that leave people scratching their heads.
The base recipe for concrete is deceptively simple: coarse and fine aggregate, Portland cement, and water. Modern concrete mixes introduce various pozzolans and admixtures to reduce cost, extend workability, and add durability. Altering the proportions of the various materials will, expectedly, change the properties of the finished material, but these characteristics are also affected by a host of variables including:
- mixing methods;
- sequence in which components are added;
- transportation time;
- environmental conditions, and
- placement and curing methods.
Consider the chocolate chip cookie: even with the most tried and true recipes, small differences in ingredient proportions and mixing methods can dramatically change the cookie’s flavor and texture. An experienced baker makes adjustments throughout the process to steer toward the desired outcome. Similarly, in concrete mixes, alterations can be made throughout the batching, mixing, and placement processes, affecting the quantity and dispersion of air and water in the concrete, thereby changing the properties of the final product.
The importance of air and water
Testing of slump, air, and water content of fresh concrete are considered routine field quality control measures. Since compressive strength testing takes place in a laboratory days or weeks after the concrete has hardened, several pours may take place on a project before any low-strength results are known and can be addressed. Rejection of a batch or two of fresh concrete may be somewhat disruptive. Rejection of in-place concrete months after placement may require removal and replacement of large sections of the structure, resulting in project delays and increased costs.
Air
Air entrainment of concrete is intended to provide freeze-thaw durability in northern climates. Air-entraining admixtures are added early in the mixing process. These admixtures congregate at the interface between air and water, effectively reducing the surface tension and allowing the formation of microscopic air bubbles during mixing (Figure 1).1 They work to stabilize the produced bubbles, but do not generate bubbles on their own. Therefore, the agitation and thoroughness of the mixing process is critical to form and distribute the bubbles throughout the mixture. A non-uniform distribution of air, or too little of it, reduces the freeze-thaw durability of the concrete. Further, too much air reduces the compressive strength of the concrete.
With air-entrainment admixtures, a little goes a long way. Typical dosages range from 7 to 180 ml (0.25 to 6 oz) per 45 kg (100 lb) of cementitious material, translating to roughly
the size of a large soft drink cup from a convenience store
for the average 7.6-m3 (10-cy) load. Minor variations in
the dosage can have a drastic effect, and the amount and distribution of air is affected by many factors including:
- water content;
- temperature;
- other chemical admixtures;
- alkalinity;
- mixing time;
- delivery methods (e.g. pumping); and
- finishing methods.
Due to these variables, admixture manufacturers do not make dosage recommendations, other than saying “start out low” and “build a relationship with the customer.”
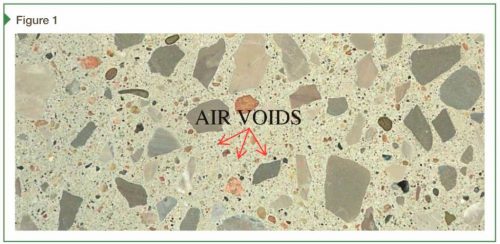
Images courtesy Raths, Raths & Johnson
Water
Water is required not only as a component in the chemical processes forming concrete but for workability during the mixing, pumping, placement, and finishing processes. As with air, too much water can lead to low strength and large voids; if water is inadequate, hydration will be incomplete and the concrete unworkable. A certain dosage of water is added directly to the concrete mix, but the amount needs to be adjusted in consideration of other mix components that can bring water with them. Aggregates have varying moisture contents depending on their absorptivity and storage conditions (e.g. Did it rain the night before? What part of the pile did the aggregate come from?). Also, most admixtures are water-based, especially corrosion inhibitors. Addition of water at the jobsite is prohibited or discouraged as it is detrimental and not well controlled or monitored. As the water content of aggregates is variable, the amount of water added to the mix is adjusted to meet a target water-to-cementitious materials (w/cm) ratio with a specified maximum. Field estimation of the w/cm of fresh concrete is performed in
one of two ways:
- using data from the batch tickets, tallying all sources of water and cementitious material (e.g. cement, slag, fly ash, and other pozzolans), and calculating the ratio; or
- using a method such as AASHTO T318, Water Content of Freshly Mixed Concrete Using Microwave Oven Drying, to measure the water content of a sample of fresh concrete, then dividing that by the design amounts of cementitious materials.
The latter method is performed as an independent check on the batch ticket method. The batch ticket depends on reliable reporting by the ready mix plant and accounting for all sources of free water.