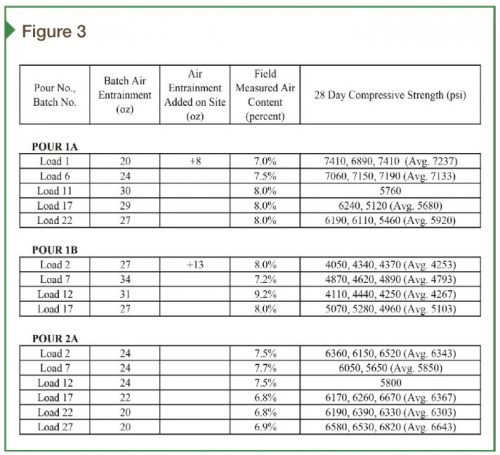
Supplementary cementitious materials
In general, supplementary cementitious materials (SCM) increase the fineness of the cementitious materials content, requiring an increased amount of air-entraining admixture to produce the same air content as a similar concrete mix containing no SCMs. The concrete mix design, used for all elevated slab pours on the project, contained 20 percent Class C fly ash and 15 percent slag cement, both of which were noted in the petrographic analysis of the hardened pour 1B samples. This suggests the excessive air content of pour 1B was not a result of the SCM content, but other factors.
Excessive air entrainment
As previously stated, with air-entrainment admixtures, a little goes a long way. Compressive strength can vary substantially with minor adjustments in air-entrainment admixture on the order of ounces per cubic yard of concrete. Unfortunately, in the field, air-entrainment dosages are heavily reliant on trial and error and the direct effects of varying dosages on compressive strength will not be known until cast cylinders are tested. Figure 3 shows reported air-entrainment dosages, field reported air content, and compressive strength results from pours 1A, 1B, and 2A (showing only batches in which cylinder samples were collected and tested for compressive strength). There is a significant drop in compressive strength with air-entrainment dosages starting in the 800 to 900 ml (27 to 30 oz) range per 7.6-m3 (10-cy) batch, and all dosages for pour 1B were 800 ml or higher. Starting with pour 2A, dosages were reduced to the 600 to 700 ml (20 to 24 oz) range with 650 ml (22 oz) becoming typical after 2A, resulting in improved compressive strength results.
Why was excessive air content not recognized during field testing? Operator error and sampling procedures are possible contributing factors, but the key reasons involve the limitations of the testing procedures. The 40 MPa mix used for pour 1B had a specified air content of 6.5 percent, with a +/- 1.5 percent tolerance. ASTM C231 has a stated multi-operator precision of +/- 0.8 percent up to an air content of 7 percent. For the latter part of pour 1A and into pour 1B, air content measurements were reported to be near or above 8 percent, which was at the high end of the specification, but also over the 7 percent threshold above which the amount of error becomes unknown. Compared with the 9 to 15 percent air content determined from the hardened concrete samples, it appears the field air tests were reading inaccurately low.
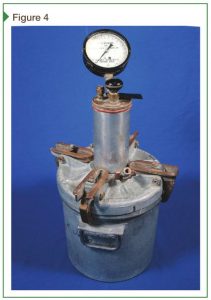
The pressure test used for pour 1B (Figure 4) has a key limitation: smaller entrained air voids are less compressible than larger voids, and a higher proportion of smaller voids go unaccounted for during the pressure stage of the test, thus the test becomes increasingly skewed toward inaccurate low readings with increasing amounts of entrained air.6 K.C. Hover describes this limitation in his article “Some Recent Problems with Air-Entrained Concrete,” and presents several case studies where the measured air content of hardened concrete was well above the field measured air content of fresh concrete, as was the case with pour 1B.
It is the authors’ opinion the low-strength results from pour 1B are attributable to high air content from excessive amounts of air-entrainment admixture, a condition not recognized during the pour.
Conclusion
This case study demonstrates the importance of field quality control and understanding the limitations of field testing procedures. Design professionals must consider these limitations when specifying concrete. The usage of admixtures and water should be controlled and air dispersions must be monitored. Thorough documentation of test results is necessary to not only demonstrate the concrete meets specification, but also to provide data for analysis in the event something goes wrong requiring remediation and prevention. Although examination of the hardened concrete is certainly helpful for investigative purposes, the properties and initial constituents of fresh concrete cannot be fully discerned by looking at the hardened concrete alone.
The various parties involved in this case have reached a settled agreement.
Notes
1 Read Design and Control of Concrete Mixtures by H. Steven Kosmatka and L. Michelle Wilson, published by Portland Cement Association (PCA).
2 Consult the American Concrete Institute (ACI) Committee 318, Building Code Requirements for Structural Concrete (ACI 318-11) and Commentary.
3 Read “Loss of Air Content in Pumped Concrete” by James Yingling, G.M. Mullings, and R.D. Gaynor from the October 1992 issue of Concrete International.
4 For more information, read “Concrete Pumping Effects on Air Entrained Concrete” by William Elkey, Donald J. Janssen, and Kenneth C. Hover for the Washington State Transportation Center (TRAC), June 1994.
5 Read “Effectiveness of Used Engine Oil on Improvement of Properties of Fresh and Hardened Concrete” by Nasir Shafiq, Muhd Fadhil Nuruddin, and Ibrahim Kamaruddin and from the proceedings of the sixth Asia-Pacific Structural Engineering and Construction Conference (APSEC 2006), held in September 2006, in Kuala Lumpur, Malaysia.
6 More information can be obtained from K.C. Hover’s “Some Recent Problems with Air-Entrained Concrete,” published in Cement, Concrete, and Aggregates in 1989.
Robert C. Haukohl, PE, is a senior engineer at Raths, Raths & Johnson, a national engineering, architecture, and forensic consulting practice. He has more than 25 years of experience in the investigation and repair design of a range of structural, material, and building enclosure non-performance issues. Haukohl is accomplished in all phases of repair design and construction administration, from development of drawing and specification packages, onsite observation of construction, and close coordination with contractors for the implementation of repair designs. He has provided litigation support services in the areas of job history reconstruction, document reviews, construction delay claims, and cause/fault determination. He can be reached via e-mail at rchaukohl@rrj.com.
Colin P. Rueb, PE, is an engineer at Raths, Raths & Johnson, with experience in structural investigations and material analysis related to concrete and prestressed concrete construction. With his knowledge of concrete deterioration issues, he has developed repair designs to address corrosion, strengthening, spalling, and other problems. Rueb’s background includes condition surveys, field testing, structural analysis, and finite element modeling of distressed façade systems, building components, and various structures. He can be reached at cprueb@rrj.com.