Step 6: The glass customization process
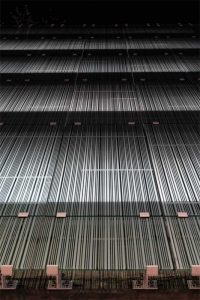
The strength and thickness of glass for exterior point-supported applications is determined by the maximum allowable deflection and wind loads. The allowable deflection equals the length of the glass lite divided by 60 (L/60). In this case, the glass panels are as large as 1 m (3 ft) wide x 3 m (10 ft) high. The maximum allowable deflection is 50 mm (2 in.), and the wind loads reach up to 2.4 kPa (50 psf) at the corners of the building.
The glass for the parking façade at 727 West Madison was engineered to the maximum allowable deflection and highest wind loads. The manufacturer determined the optimal glass makeup for the application was 20-mm (¾-in.) tempered-and-laminated glass. The tempering process involved reheating the cut-to-size lites to approximately 680 C (1200 F), then rapidly control-cooling them to increase their tensile strength. Lamination followed, sandwiching two tempered glass panels together, and creating the specified decorative designs.
The resulting safety glazing meets the requirements for the American National Standards Institute (ANSI) Z97.1, Safety Glazing Materials Used In Buildings – Safety Performance Specifications And Methods Of Test, and the Consumer Product Safety Commission (CPSC) Standard 16 Codes of Federal Regulations (CFR) 1201, Safety Standard For Architectural Glazing Materials. While the glass is not located in a safety condition, the tempering and lamination processes add strength and security. Additionally, the position of the ventilated glass façade—above a busy pedestrian thoroughfare and retail outlets—favors the use of safety glass for added peace of mind. A glass thickness of 20 mm is maintained consistently throughout the façade for ease of installation.
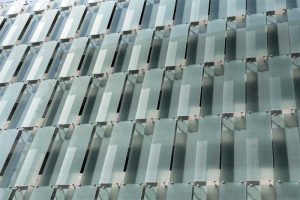
Photos © Kelly Drake Photography
Once the technical requirements for the glass were established, the façade supplier collaborated with the architects to develop several decorative glass designs. The ‘in-and-out’ north and south façades were constructed with 546 translucent, white laminated glass panels in two levels of opacity. The glass lites that punch forward are a more transparent shade of white, while the background ones are a denser tone. The tonal offset visually enhances the sense of depth. On the west, the ‘flat’ façade comprises 406 fritted glass panels featuring a custom linear pattern. They provide solar shading, while maintaining occupants’ visibility to the exterior. The patterned glass effectively screens the parking decks, creating a chic monolithic appearance when viewed from the street. True to the design-assist process, the architects collaborated closely with the façade supplier in order to manufacture the budget-friendly, non-repetitive fritted pattern. Three unique screens were produced, then rotated and mixed to achieve visual variability without increasing the cost.
Step 7: Execution
The most standout element of the ventilated glass façade’s construction is how it attaches to the building. As mentioned, the glass system supplier developed a method to mount the cladding directly to the parking structure’s concrete walls and slabs through embeds. To accomplish the money-saving design, the system was engineered with generous 50 mm (2 in.) tolerances in all directions. Wherever two metal components meet to create the necessary movement, both are serrated to lock securely into place. Building all the necessary tolerances into the cladding system facilitated installation and eliminated the use of unsightly shims, creating clean exposed structural details.
Close collaboration and precise drawings from the manufacturer for all cladding components, including embeds, were critical for the success of the installation. The glazier was instrumental in ensuring the approved layout was implemented by all involved construction teams.