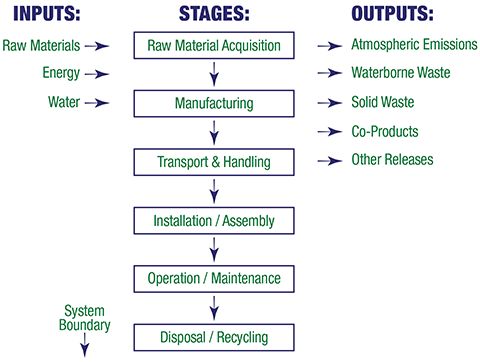
The product lifecycle
The assessment and measurement of the environmental impacts reported in an EPD are structured to include all aspects of a product’s lifecycle, from the initial acquisition of raw materials to the eventual removal and disposal of the product. This lifecycle typically is described in an EPD using a diagram similar to Figure 3.
The concept of the product lifecycle has been refined and expanded to include a number of important elements. It begins with inputs such as raw materials and energy before moving these inputs through a series of processes from initial material acquisition all the way to eventual disposal and recycling. In moving through these processes, one produces many different outputs in the form of emissions and wastes that impact the environment.
Another important element in this lifecycle chart is the system boundary. Essentially, it is a way to admit the user may not always capture every impact on the environment, but still needs to clearly state where the assessment begins and ends. Additionally, the system boundary is critical to ensure consistency and comparability among products.
To gain a clear understanding of the concept of environmental impact over the product lifecycle, it may be helpful to view the EPD as an estimated measure of net product impacts over time. Every product starts with a design concept, which may have little or no impact. However, as we acquire the raw materials, manufacture and ship the product, install and maintain it, and eventually remove and dispose of it, the air, water, and land are impacted in numerous ways.
Service life is also a vital factor. The longer a product’s useful service life is extended, the more its overall impact is reduced. An illustration of the concept of environmental impact over time is shown in Figure 4.
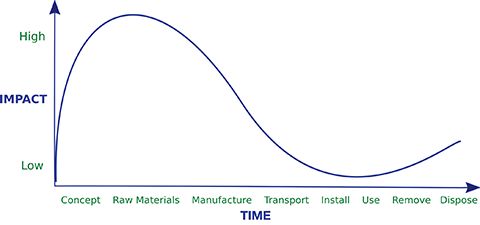
Common functional unit
As the standardized ISO foundation is so critical to EPDs, it is important to note the purpose or function of these tools is, according to ISO 14025, to enable comparison between similar products. This means the impact data of a particular product should be comparable to impact data for a similar product with the same function. To accomplish this, a functional unit most relevant to the impacts associated with a group of similar products must be identified. Frequently, the basic functional unit identified within the ISO process is a measure of mass or area, such as kilograms or square meters. Finally, the functional unit also involves a timeframe, typically related to the product’s service life.
There is the question of how exactly one gets quantified information that can enable comparison among similar products. A product category rule (PCR) is intended to ensure products with similar functions may be assessed in the same way using comparable measures. PCRs are developed in accordance with ISO standards, which call for the formation of a consensus body backed by third-party validation to develop each PCR.
To answer the critical issues of product comparison, the PCR establishes several key elements of how every LCA for a particular class of product should be conducted, including:
- the functional unit, including the time frame for the product;
- the system boundary; and
- the impact categories to be assessed.
By doing this, the PCR helps to ensure meaningful comparisons may be made among similar products.
An example of a PCR relevant to the construction specifier was developed recently by a broad coalition of insulation manufacturers under UL’s third-party stewardship. This PCR covers all building envelope thermal insulation, including fiberglass, mineral wool, expanded polystyrene (EPS), extruded polystyrene (XPS), and polyisocyanurate (polyiso).
This thermal insulation PCR uniquely defines the functional unit as a square meter of insulation with a metric RSI value of ‘1.’ This is very important because the thickness required to obtain this RSI value varies significantly between different insulations. In many cases, we really do not care about the exact thickness of the insulation because the material’s critical function is related to the ability to resist heat transfer, as measured in R-value. The PCR also identifies the service life to be 60 years—the current standard for typical building service life in the new International Green Construction Code (IgCC).
Unless damaged by unforeseen forces, most thermal insulations have a service life of 60 years or more when protected within a wall, ceiling, or roof. Finally, the thermal insulation PCR establishes the system boundary to be cradle-to-grave, which includes all processes leading up to the delivery of the insulation to the jobsite, its installation during construction, and its maintenance over the service life, along with its removal, disposal, and possible recycling at the end of its service life.