The evolution of fluid-applied membranes
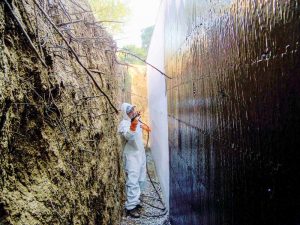
Single-component polyurethanes are generally cost competitive with other waterproofing systems. The simplicity of installation, and versatility in both vertical and horizontal applications, make it an attractive option for most projects. Maintaining the proper thickness and applying multiple coats if necessary are critical to the success of these systems. Two lifts may be necessary on vertical surfaces to achieve a 1.5-mm (60-mil) thickness. For more robust horizontal waterproofing, many single-component polyurethane products can be applied at 3 mm (120 mils) with non-woven reinforcement sheets.
Another newer, single-component technology, moisture-cure, silyl-terminated polyether (STPE), materials combine the solvent-free advantages of a two-component polyurethane with the simplified installation of a one-component product. Other names for this chemistry include silyl-modified polyurethanes, polyether, silyl-terminated polymer, silicone-modified polyester (SMP), and MS polymer. There is no flammability risk or odor, and they are lower in VOCs. These products also contain significantly higher solids content, meaning little to no shrinkage as the product cures.
However, this technology is susceptible to the challenges of a moisture-cure. The membrane cures from the exposed edge inward, meaning the surface ‘skins over’ very quickly, while the interior remains a liquid for longer. When the concrete substrate is heated by the sun, water vapor from within the concrete will push its way through the still liquid portion of the membrane, creating bubbles and blisters on the waterproofing surface. Proper installation of these membranes includes application at the correct time of day and only over substrates that have low moisture content. Many manufacturers recommend the use of a primer in situations likely to produce blistering. This recommendation may be written into the specifications, if necessary.
One response to the bubbling challenges of moisture-cure membranes is the recent development of polyurethane water-cure technology. These products are only applicable for horizontal surfaces and must be water-saturated to cure. Moisture-cures set slower in comparison because the required moisture absorption from the air is gradual, curing from the edge-inward. With water-cure technology, the entire membrane cures simultaneously. Water-cure membranes set extremely quickly, some in as little as two hours, before escaping water vapor can create blisters or bubbles in the membrane.
Acrylic resins
PMMAs are two-part acrylic resins offering quick cure times through use of a catalyst. First synthesized in the 1930s, PMMAs did not become a viable waterproofing product until the early 1970s. When compared to asphaltic polyurethane membranes, these resins exhibit tremendous hardness as noted in their Shore Hardness data. The high-achieving abrasion and impact resistance of PMMA resins can be found in the manufacturing of aircraft windshields, safety glasses, dental fillings, and even contact lenses. Additionally, their water and chemical resistance and tolerance to heat and cold make these membranes applicable to a wide-range of construction applications. PMMAs provide the base to most traffic coatings, although polyurethanes can also be used for this purpose.
Around the turn of the millennium, a variant of PMMA was developed with the addition of polyurethane. PUMA couples the elastomeric properties of polyurethane with the durability of PMMA. The resulting PUMA membrane adds three to four times the elongation over a typical PMMA membrane. This is particularly important in northern climates where temperature extremes are greater than southern climates. Reinforcement material may be required at penetrations and transitions to ensure the material is applied at the specified thickness, but PUMA membranes are strong enough to forgo fleece reinforcement fabric that is common among PMMA membrane systems.
With the use of an epoxy primer, both resin versions feature the advantage of green concrete application approximately
72 hours after form removal. Substrate and ambient application temperatures are accommodated as low as –6 C (20 F). PUMA membranes require careful understanding of ambient conditions. Application must take place at not less than –15 C (5 F) above the dewpoint. Installers are advised to be trained and authorized by the manufacturer. These waterproofing systems are generally designed for horizontal applications such as split-slab, paver systems, planters, and vegetated roofs.
While these technologies are extremely effective, PMMA/PUMA systems are estimated at up to twice the cost of an SBS, hot-fluid-applied rubberized asphalt system. However, quick production times and the elimination of protection course, termination bars, and other accessories are to be considered.
Conclusion
While fluid-applied waterproofing products have recently surged in popularity, fluid-applied materials have existed in various forms for centuries. Instead of new technologies replacing previous products, new fluid-applied technologies are added to an expanding portfolio of waterproofing chemistries. Almost all fluid-applied waterproofing technologies that were ever developed are still offered in some form today. With numerous options available, selecting the right system can be confusing. Balancing durability, material cost, and difficulty of installation, as well as construction schedules and budgets can seem overwhelming. However, the best waterproofing material is a well-installed one. No matter which product is selected, a knowledgeable installer will have the greatest impact on the success or failure of the waterproofing system. Concise specifications to communicate product information and quality standards, along with comprehensive detailing to provide explicit installation guides to the installer, will set the groundwork for a quality installation of any fluid-applied waterproofing system.
Isaac Sorensen, CSI, is architectural specialist, New York and Northeast Region, W.R. Meadows. He can be reached at isorensen@wrmeadows.com.
Roger Smith, CSI, ICRI, is architectural specialist, Southern California, W.R. Meadows. He can be reached via e-mail at rsmith@wrmeadows.com.
Stacey Bogdanow, CTR, is responsible for outside sales, Toronto and Eastern Ontario, W.R. Meadows. Bogdanow can be reached at sbogdanow@wrmeadows.com.
Russ Snow, CSP, CTR, BSS, LEED AP, is product group manager–building envelope, W.R. Meadows. He can be reached at rsnow@wrmeadows.com.
Conleigh Bauer, CSI, is architectural specialist, Texas, LA, OK, AR, W.R. Meadows. She can be reached at cbauer@wrmeadows.com.
Scott Wolff, CSI, CDT, BEC, is architectural specialist, Upper Midwestern States, W.R. Meadows. He can be reached via e-mail at swolff@wrmeadows.com.
Patrick Raney, CSI, ICRI, is architectural specialist, Northern CA and Northern NV, W.R. Meadows. Raney can be reached at praney@wrmeadows.com.
Taylor Wodzinski is the architectural specialist for Illinois, W.R. Meadows. She can be reached at swodzinski@wrmeadows.com.