Asphalt became a step down from coal tar pitch
Shortly after World War II, a United Mine Workers of America (UMWA) strike devastated the coal industry. The work stoppages effectively cut off the supply of coke to steel mills—and with it, the by-product of coal tar pitch. Roofing and waterproofing manufacturers and contractors were left without their only reliable source of pitch, which had served them so well since the 17th century. They were forced to switch to roofing asphalts, which were a by-product of the oil refineries’ distillation process.
Lloyd A. Fry, a roofing manufacturer in the Midwest, produced various grades of roofing asphalts, including those that were unblown—an oxidizing process to increase resistance to flow on steep roofs. In 1937, ASTM published the first consensus standard for waterproofing asphalt. It specified three types with varying degrees of softening points—Types I, II, and III. Type I, the least viscous, was defined as a soft, adhesive, “self-healing” asphalt suitable for below-grade waterproofing in moderate temperature conditions.
Waterproofing contractors used self-healing asphalt with varying degrees of success. The membranes employed asphalt-saturated organic felts, generally made from waste paper, for reinforcement. They lacked the strength of rag felts used with pitch due to the shortage of suitable rags and jute following the war.
Asphalt and coal tar pitch are chemically different; the former is an aliphatic and the latter is an aromatic. One of the differences includes the ability to self-heal—coal tar pitch is notably better in this regard and is capable of self-healing at lower temperatures. When designers changed from coal tar pitch to asphalt waterproofing, they did not consider the importance of self-healing until they were faced with a rash of failures. Wearing courses were applied directly to three- and four-ply reinforced asphalt waterproofing membranes, as was traditional for coal tar pitch membranes. Low ambient temperatures reduced the asphalt’s ability to self-heal. Leaking was common when the wearing slab that was bonded to the asphalt-based membrane moved differentially and ruptured it.
A concomitant number of factors combined to acerbate the waterproofing splitting problem that resulted in leaking. Basements that had been used solely for boiler rooms and storage spaces now housed moisture-sensitive auditoriums and server-computer rooms. These spaces were climate-controlled, which required insulation, sometimes installed on the soffit of the slab—this effectively reduced the beneficial warming from heat loss that permitted bitumen to self-heal. At the same time, advances in engineering resulted in thinner structural slabs, permitting greater deflections and creep that overstressed asphalt membranes’ tensile strength. (For more, see S.S. Ruggiero and Rutila’s work in ASTM STP 1084, Principles of Design and Installation of Building Deck Waterproofing, published in 1990.) Further compounding the situation, manufacturers reduced the amount of asphalt used to saturate the felts.
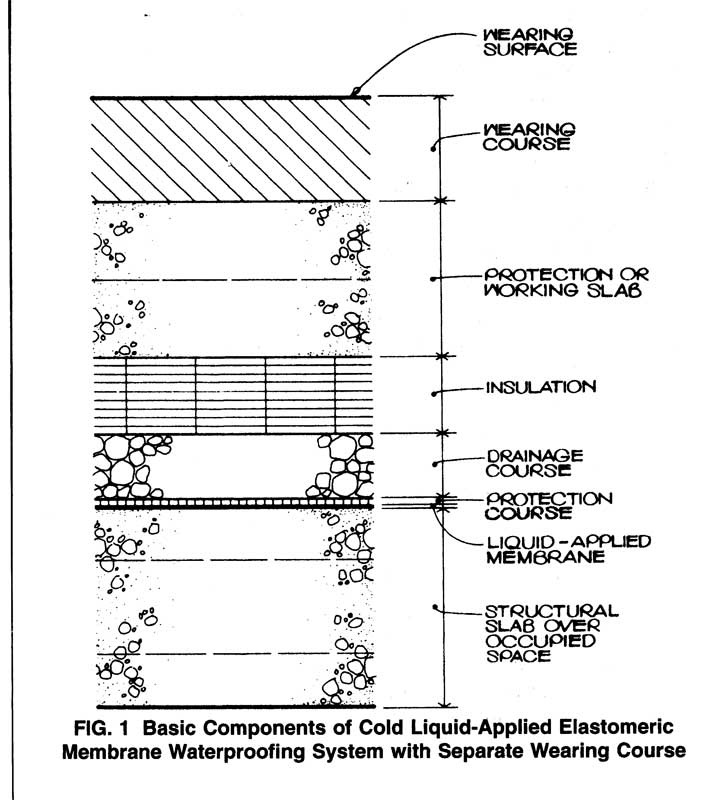
Image courtesy ASTM International
Design progress begins in the mid-1960s
Asphalt membrane splitting problems were greatest in Canada, where low ambient temperatures were the norm. The Division of Building Research of the National Research Council of Canada (NRC) had assembled a remarkable group of building pathologists who authored the Canadian Building Digests. One of these was G. K. Garden. In a March 1966 article about roof terraces, he advocated use of a drainage medium between the membrane and the wearing course. This drainage layer effectively divorced the membrane from the stresses associated with differential movement between membrane and wearing slab. He also noted the importance of sloping the membrane to drain.
Garden’s concepts were subsequently incorporated in Charles J. Parise’s 1971 book, Architectural Considerations in Plaza Membrane Waterproofing Systems. (Parise’s work appeared in the May 1971 edition of ASTM International’s Materials Research & Standards [vol. 11, no. 5].) The principles Parise espoused were eventually incorporated into ASTM C898 for liquid-applied waterproofing in 1978 (now titled Standard Guide for Use of High Solids Content, Cold Liquid-applied Elastomeric Waterproofing Membrane With Separate Wearing Course), under the jurisdiction of subcommittee C24.80, which he chaired. This was followed by C981, Standard Guide for Design of Built-up Bituminous Membrane Waterproofing Systems for Building Decks in 1983.
The plaza waterproofing assembly consisting of a structural slab sloped to drain, membrane drainage course, insulation, and wearing course was widely implemented in the industry (Figure 2). It markedly reduced incidents of leaking from differential wearing slab movement. Moreover, introduction of more robust flashing materials and movement joints at membrane terminations reduced failures that had been common with stripped-in metal base flashings.