Alternative membranes come of age
Some manufacturers of atactic polypropylene (APP) and styrene-butadiene-styrene (SBS) modified bitumen roofing felts marketed their multiple-ply systems for use as waterproofing systems on plazas. Those proved to be unsuitable because the cut edges of the sheets allowed water to wick into the reinforcing, causing swelling and subsequent disbonding. Some manufacturers now use a non-woven polyester reinforcing that avoids this problem.
Built-up, hot-applied asphalt and glass fiber felts disappeared from the market because of labor intensity and high water absorption under ponding conditions. Built-up coal tar pitch membranes with glass fiber felts failed when the glass fiber reinforcing migrated to the bottom of the membrane, leaving little or no interplay pitch between the felts. Restrictions regarding volatile organic compounds (VOCs) eventually caused their complete demise. That paved the way for an influx of single-ply and liquid-applied membranes.
The success of reliable single-ply roofing systems encouraged their use as plaza waterproofing membranes, which proved to be far superior to the built-up asphalt and felt membranes they supplanted. In addition to the use of single-ply membranes, liquid-applied waterproofing membranes were introduced in the 1960s. These included cold-applied, coal-tar-modified polysulfide single-component membranes, and hot-applied rubberized asphalt. The former proved
to be too sensitive to temperature extremes and was subsequently abandoned in favor of one- and two-component urethane-modified bitumens. Although the polyurethane-modified bitumens were not temperature-sensitive, they were extremely moisture-sensitive.
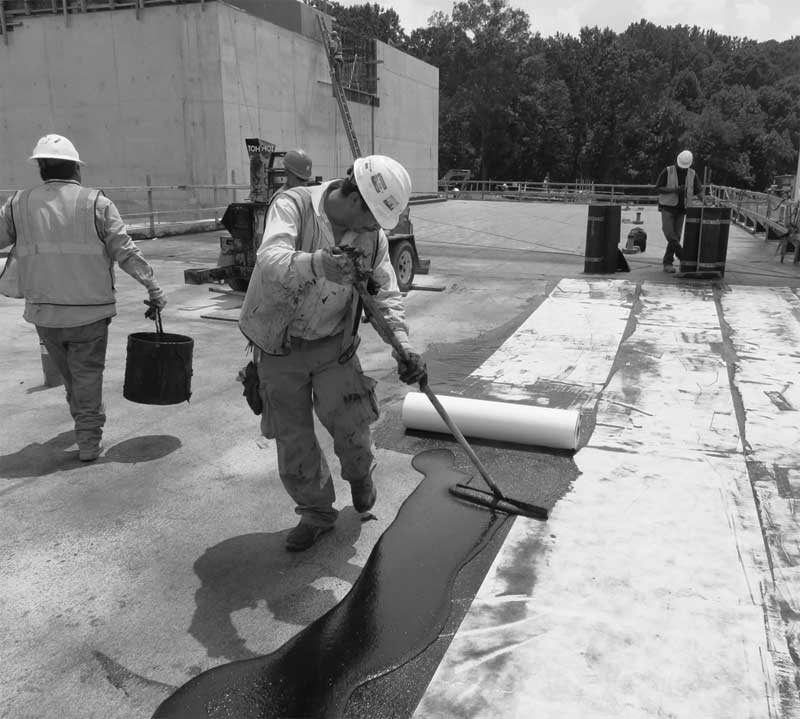
Photos courtesy Henshell and Buccellato Consulting Architects
Liquid-applied membranes
Subsequently, a host of liquid-applied elastomers, including polyesters, polyethers, one- and two-component synthetic rubber and asphalt emulsions, and polymethyl methacrylate (PMMA and MMA) were marketed for plaza waterproofing. These elastomers cured by exposure to air (one-component membranes) or by chemical reaction (two-component membranes), as shown in Figure 3.
Hot-applied rubberized asphalt was another liquid-applied plaza waterproofing membrane. It was introduced from Canada by a number of rubber companies in the 1960s and 1970s. These products were polymer-modified asphalt mixed with rubber crumbs and clay, applied hot over a primed deck. They formed a membrane as soon as they cooled. They also adhered better to slightly damp concrete substrates. (For further information on hot-applied rubberized asphalt waterproofing membranes, see Tim Barrett’s articles in the February 2000 and November 2013 issues of RCI’s Interface magazine. In addition to Parise and Garden, no discussion of plaza waterproofing would be complete without mentioning two pioneers instrumental in influencing its development: Dorothy Lawrence, FASTM, and David Spalding. Lawrence compounded a neoprene-modified asphalt sheet with the addition of carbon black applied to a woven-glass carrier in 1949. The membrane system consisted of these sheets interlayed with a compatible adhesive applied cold in two plys. It required no primer and adhered to moist concrete. This membrane was installed on Cobo Hall in Detroit in 1959—it still performs satisfactorily. Spalding marketed a hot-applied rubberized asphalt imported from Canada in 1977. The product, composed of polymer-modified asphalt with rubber crumbs and clay, was heated in a double-jacketed kettle and squeegeed over a primed concrete deck. It ‘cured’ as soon as it cooled, in contrast to polyurethane and other cold-applied waterproofing membranes. Spalding’s singular contribution to this product was to reinforce it with a polyester fabric in the 1980s. This required two coats at a total thickness of 5.5 mm [215 mils], which provided redundancy and solved the problem of pinholing and cratering that had plagued other producers. It also solved the problem of heating resin-type formulations to the degree it impaired adhesion.)