Single plies
Producers of single-ply sheet roofing also marketed their sheets for use on plazas in the mid-1960s. A 1968 article in Concrete Construction lists membranes made of “natural and synthetic rubber, vinyl, neoprene,” as well as “asphalt reinforced with glass fibers bonded to high-strength backing.”
Synthetic rubber sheets, including butyl and ethylene propylene diene monomer (EPDM), and polyvinyl chloride (PVC), were manufactured by several companies. These products were used on roofs as well as under paved plazas and vegetative roofs. Subsequently, market forces and consolidations led to fewer single-
ply manufacturers.
Many products have been improved since their introduction. PVC membranes are installed loose-laid over bonded strips that provide compartmentalization to simplify leak detection. Moisture-resistance of EPDM adhesives has been improved, and redundancy is provided by cover strips over the seams.
Consisting of 1.4 mm (56 mils) of asphalt modified with reclaimed rubber and resin modifiers laminated to 0.1 mm (4 mils) of high-density polyethylene (HDPE), 1.5-mm (60-mil) thick self-adhering rubberized asphalt sheets were introduced into the United States from Europe in the 1970s. As they had factory-controlled thicknesses, were applied cold, and required only a single ply to perform satisfactorily, they rapidly dominated the market.
When the initial manufacturer’s patents expired, similar products with different modifiers and asphalts were marketed by more than a dozen firms. Some manufactured products, while others rebranded existing products. Thinner versions were marketed for through-wall flashing, shingle underlayments, and air/vapor barriers. Some producers of rubber-modified asphalt plies persisted and developed successful hot- and cold-applied built-up systems still used in new construction.
Plaza waterproofing today
Today, at least 60 waterproofing products are marketed in the United States for use under plazas. These include:
- more than 30 one- and two-component cold liquid-applied systems;
- nine hot-applied rubberized asphalt membranes;
- 15 manufactured sheet membranes; and
- at least five built-up membranes.
The majority of these do not list resistance to hydrostatic pressure as a physical property or claim they are suitable for below-grade use. Only a few manufacturers say they can be used in split-slab configurations in which the wearing course is cast directly over the membrane. However, most adhere to the principles espoused by Garden and Parise, requiring a drainage medium and/or insulation to divorce the wearing surface from the membrane.
More versatile polymer-based liquid-applied membranes have been developed. Many were first used in Europe. Increasingly stringent VOC requirements have forced many manufacturers to reformulate existing products or design new ones that conform. Water-based primers have supplanted their solvent-based counterparts. Epoxy primers are increasingly used on decks that are not as dry as moisture-sensitive membranes require. Membranes with shorter curing times have been developed in response to the demands of tighter construction schedules.
Some currently marketed hybrid sheet membranes and systems are factory-laminated, and others are applied as separate layers. In particular, polymer-modified sodium bentonite is laminated to ketone ethylene ester (KEE) membranes for loose-laid applications. Products that could not satisfy Leadership in Energy and Environmental Design (LEED) program proscriptions of environmentally hazardous materials have been withdrawn from the market or reformulated. Multiple-ply membranes previously applied with hot adhesives are now applied with cold adhesives. Torch-fused sheets and seams are rapidly giving way to robotic hot-air-fused seams, eliminating the need to maintain a fire watch after the last torch is extinguished.
Self-adhering membranes are beginning to dominate the field, although hot-applied rubberized asphalt is a strong competitor in some markets. Two-component sprayed or squeegeed liquid-applied polymers, such as polyester and PMMA, have recently become very popular.
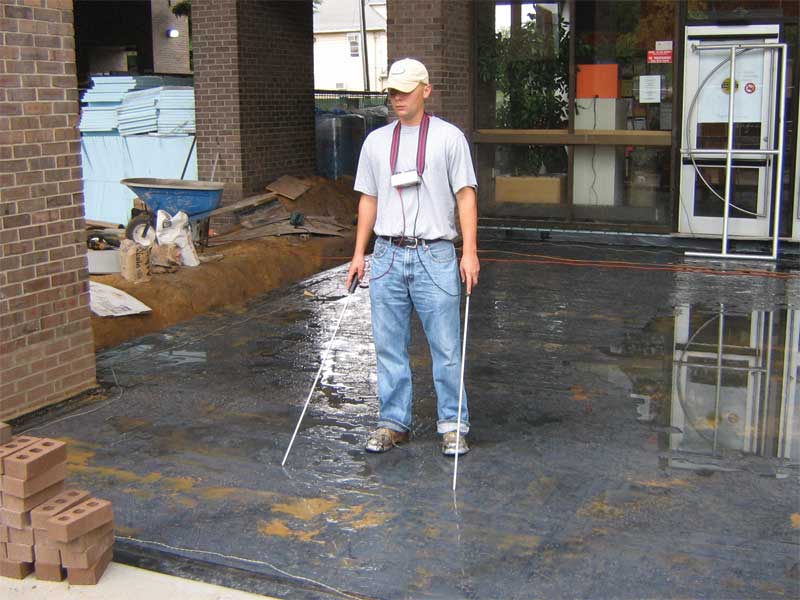
New developments and industry challenges
This look at the past of waterproofing leads us to the present and immediate future of the industry and its product development. Bentonite manufacturers are modifying their clay with polymers and producing many hybrid systems. PVC manufacturers are modifying their sheets with greater amounts and more sophisticated forms of KEE plasticizers. Manufacturers are continuing to replace hot-applied adhesives with cold-applied adhesives. New fluid-applied products continue to appear as manufacturers try to improve performance. The industry is adopting electronic testing to verify membrane integrity in lieu of flood testing (Figure 4). Plastic drainage composites have completely supplanted aggregate drainage courses.
Manufacturers are struggling to develop primers and systems permitting application of their products on concrete decks containing injurious amounts of moisture. Lack of adequate adhesion has become a greater concern than tensile failures. In this author’s opinion, the greatest single problem facing the industry is substrate moisture. Design/construction professionals still need a reliable test for moisture in concrete slabs, along with a universally acceptable definition of what ‘dry’ means. (The definition of cured concrete is when it reaches its design compressive strength in seven days. Concrete is ‘dry’ when the percent of vapor transmission rate, in lb/1000 sf/24 hours is less than 75 to 80 percent, as per the 15th edition of the Portland Cement Association’s (PCA’s) Design and Control of Concrete Mixtures (Steven H. Kosmatka and Michelle Wilson), which is available at www2.cement.org/pdf_files/eb001.15.pdf. This definition is generally agreed on by the floorcovering industry, but not accepted by the roofing/waterproofing industry.) Simple, economical methods for reducing elevated moisture content are also necessary.
This problem is not limited to adhered waterproofing systems. Manufacturers of loose-laid sheets find difficulty with adhering compartmenting strips to concrete substrates. Adhesive seams can disbond from water under the membrane. Bentonite coatings can become pre-hydrated.
Parise, Garden, and their colleagues overcame the splitting problems. Now, it becomes our hope contemporary problems can be as easily solved by the next generation of plaza waterproofing systems.
THE ROLE OF ASTM INTERNATIONAL |
ASTM Subcommittee D08.22 on Waterproofing and Dampproofing Systems was formed in 1993 by Charles Pratt of Koppers Co. and Dorothy Lawrence of Laurenco Waterproofing. Currently it has more than 20 standards under its jurisdiction. In 2000, James Strong of WJE, who chaired subcommittee C24.80, was instrumental in transferring the standards for liquid-applied waterproofing under its jurisdiction to D08.22. In addition to standards for waterproofing materials and applications, this committee has developed standards for drainage media and concrete preparation, and test methods for membranes’ physical properties and integrity. Currently it is developing a new standard for hot-applied rubberized asphalt to replace the Canadian standard that was withdrawn several years ago. |
Justin Henshell, CSI, FAIA, FASTM, is a principal in the firm of Henshell & Buccellato Consulting Architects, specializing in moisture-related issues in the building envelope, since 1974. His focus includes roofing, masonry walls, waterproofing, and condensation. Henshell has authored more than 40 technical articles and papers, presenting them in the United States, Canada, and Europe. He wrote The Manual of Below-Grade Waterproofing (Routledge, 2016). Henshell can be contacted via e-mail at justin.henshell@verizon.net.