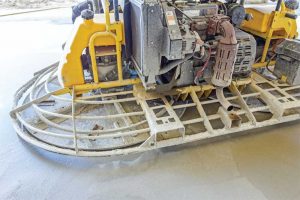
Installation
With a flooring adhesive, the correct method over a porous surface may be as simple as an application rate and open time difference versus a non-porous surface, instead of a change in the product. Installation data sheets for flooring adhesives generally include a table or chart recommending trowel size, application rate, and “open time” or “flash time” for both porous and non-porous surfaces. The working time of the adhesive may be reduced as the flash time increases, so the floorcovering installer will need to manage it accordingly. The non-porous surface flash time of the adhesive is greater than the duration for a porous surface (i.e. another 10, 20, or 30 minutes), and is influenced by concrete surface temperature, ambient relative humidity and temperature, and airflow. This is regardless of whether the adhesive is being applied over a porous or non-porous surface. This flash time facilitates the evaporation of moisture from the adhesive, and if flash time is insufficient, the moisture could be trapped when installing an impermeable floorcovering. This can compromise adhesive cure and strength development, thereby jeopardizing the integrity of the floorcovering bond to the subfloor surface. Adhesive migration may also develop between the seams and transition areas to the surface of the floorcovering.
The importance of evaluating substrate surface porosity is not limited to adhesives, and can encompass many other products, such as primers, thin sets, and cementitious underlayments. For such products, and even for some adhesives, a concrete surface profile (CSP), as described within the International Concrete Repair Institute (ICRI) Technical Guideline No. 310.2R-2013, of CSP 1 or more may be required if the pre-existing substrate tests as “porous.” When this occurs, the generally accepted method for preparing the substrate surface is by mechanical means. ASTM D4259, Practice for Preparation of Concrete by Abrasion Prior to Coating Application, is a good resource in which such mechanical methods are described in detail. In some cases, it may also be possible to install a primer specifically designed for non-porous substrates that might preclude the need to mechanically prepare the substrate surface. Also, there may be other products that do not require a porous substrate. If such products are available, they should be given significant consideration as it would reduce labor and time costs for surface preparation, and perhaps, more importantly, minimize the production of respirable silica dust, a material regulated by the Occupational Safety and Health Administration (OSHA).
The role of the architect
As the author of the specifications constituting part of the contract documents, the architect (and their consultants) has considerable impact on this issue. All too often, under which adhesive to use—buried within various 09 Divisions—the phrase, “as recommended by flooring manufacturer,” is embedded into the specs. Though seemingly in the best interest of the project, that short phrase may actually limit the options for addressing a non-porous substrate surface, and end up causing the project significant schedule delays and cost overruns, especially if the manufacturer of the specified flooring does not offer an adhesive product that can be used over both porous and non-porous surfaces.
This recently occurred with an 18,581-m2 (200,000-sf) hospital project in central Florida. The project specification for resilient flooring required, in part, the use of an adhesive as recommended by the manufacturer. The manufacturer, unsurprisingly, recommended one of their adhesive brands. Upon closer analysis, their adhesives were only for porous substrates. The flooring manufacturer’s installation instructions said that if the concrete substrate surface was non-porous per ASTM F3191-16, the concrete substrate would need to be bead-blasted and self-leveled, so their porous substrate-only adhesive could be used. Upon discussion with the architect, that initial adhesive specification language was changed to “… an adhesive compatible with flooring material backing and suitable for substrate conditions.” Seemingly a simple word change, but had that change not been made, the entire project may have required bead-blasting and self-leveling. Such a process would likely have necessitated a change order on the magnitude of $600,000 to $700,000 and weeks of additional time. By thinking through the ramifications of the initial specification language in conjunction with the specified flooring, the design team was able to proactively address this potentiality through a slight alteration of the specification language. This directly and materially contributed to construction team being able to stay on budget and schedule; and all applicable warranties conveyed to the project.
Success is achievable
If the submitted floor system material that will be in direct contact with the substrate surface—irrespective whether the material is a primer, adhesive, thin set, or cementitious product—is unsuitable for direct installation on a non-porous substrate surface, the project may face extra costs and time during substrate preparation; thereby creating a delay in overall project delivery. Due to this, it is advisable to research the installation requirements for such products as it relates to substrate surface porosity, and perhaps alter any corresponding specification language to allow for the selection of alternative products because, in many cases, such alternatives are readily available without compromising warranties. Regardless of the approach, the importance of assessing concrete substrate porosity before installing flooring system materials cannot be overstated and has reached the level of being balloted for inclusion within ASTM F170, Standard Practice for Preparing Concrete Floors to Receive Resilient Flooring.