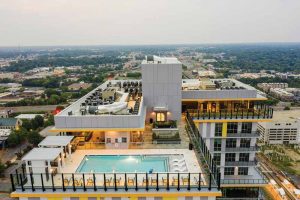
Structural engineering and column design
Starting from the lowest level, parking should be designed as efficiently as possible since below-grade parking spaces are the most expensive type of space. Moving up to grade, retail is sandwiched between parking and the residential floors above—now the coordination process begins. At this point, the process can be complicated or creative, and it is frequently both. Retail levels typically occupy the most volume due to desired ceiling heights and this can be an advantage. Looking at an unframed concrete high-rise, a very literal view of how early decision-making impacts design can be seen. If it looks like the parking levels are on their perfect grid, one might notice how the columns shift and angle by the time the structure gets to the residential floors. Columns can step, slope, and they can also be transferred, and in the end, this project utilized every available technique to achieve its goals.
In the earliest stages, design teams and clients will be focused on unit plans and resident usability. However, it is crucial to give the structural engineer a seat at the same table when conceptualizing unit plans. This provides active feedback that considers column width, while the designers focus on the resident experience. Think of this as an ongoing conversation. If this process becomes siloed, then the designer might have to scrap a layout that has already been approved. To keep those finer touches intact, teams must have the structural engineer designing and calculating early on in schematic design. Livable, valuable units start with structural details such as column placement.
Coordination and communication
The process of coordinating, even between members of the same team, can be a challenge on projects such as The Vermeer and The Ellis. Keep in mind, there are consultants and contractors who also need to be aware of the design. There are many members of the design team today, especially on complex high-rise projects, but thanks to tools such as building information modeling (BIM) and more, the coordination process has taken on a new form over the years.
From sharing REVIT models to Navisworks clash detection, to live Bluebeam sessions, members of these large coordination teams can stay connected. It does not stop at the coordination between consultants, as the ability to have live PDF mark-ups has streamlined a more efficient way to exchange comments, thoughts, and solutions between the design team and clients. These tools keep teams and the project on track. Critically, they also keep the coordination conversation flexible and ongoing as decision-making shifts onto other details such as materials.
Constructability is another factor that should be part of the discussion from the beginning, to keep costs on track and the final product true to the original intent. Coordination between the design team and general contractors must be a priority during design development to make the most effective use of the expert construction knowledge available. Pushing these conversations to a later stage or leaving them until after breaking ground causes construction delays and on-the-fly solutions. Getting the general contractors to the table early and often to provide essential feedback on cost, availability, and constructability is essential to an efficient design process and to success later in construction. Without this coordination, details may require redesign due to site conditions, costs, or construction.
Selecting the right materials
There are many different materials and construction systems to choose when building a high rise—each with its upfront and hidden costs and benefits. Steel and concrete are traditional choices, with light gauge steel becoming a more attractive option. It is important to consider the construction and delivery methods early on. Will there be panelized or modular components? If so, how will the team coordinate with the factory to get them delivered on time? Where will the materials be stored when the building is under construction? The question then becomes figuring out if the right choice has been made and then how to move forward in this process.