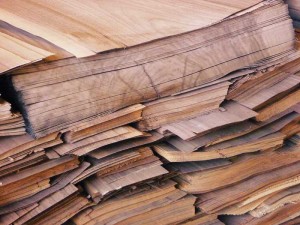
Other suppliers assemble layers of lumber into a log that is then sliced into veneer. Layers of darker and lighter wood are evenly distributed so the overall visual character is more harmonious, from panel to panel and from one end of a panel to the other. The same process can also be used to create a multi-colored, striped effect by interspersing several species that have a range of tones.
Techniques for creating faux wood continue to improve; some printed ‘veneers’ now have a dimensional texture that comes close to looking like real wood, and have been reformulated to be free of polyvinyl chloride (PVC). They can be used to provide greater uniformity than natural veneers, or as an economical alternative to an expensive wood. However, real wood, even if highly engineered, still has a luster and dimensionality that cannot be matched by a faux product; wood fibers interact with light in a way only a natural material can.
Cutting and slicing
The appearance veneer is strongly influenced by the plane, relative to the axis of the trunk, along which it was cut or sliced out of a log. Each thin slice is called a flitch or, once it has been trimmed to size, a leaf.
Pattern matching
Flitches and leaves are typically bundled in the order in which they occurred in a log. This allows them to be matched, edge-to-edge, in sequence to create the required pattern. The orientation of leaves in relation to adjacent pieces determines the veneer pattern.
Faces
Leaves are then assembled into sheets, called ‘faces,’ that can more readily set into place over a core. Veneers must be selected and assembled to create a harmonious composition in keeping with the specified pattern and the designer’s intent. The face becomes the visible surface of a panel; while specialized machinery is used throughout the process, no robot can replace the trained eye of someone that understands and appreciates wood.
The process begins when skilled inspectors sort incoming bundles of flitches by color and figure. Selected leaves are arranged into the required pattern and fed through a machine that carefully glues the thin edges of veneer together; strips of tape are applied to one surface to help hold the fragile faces together. After final visual inspection, faces are sent to panel manufacturers.
There, faces are adhered to a core and held tightly in place until the bond cures. Tape strips are left on the exposed surface to avoid their telegraphing through the thin veneer. Sanding removes the tape and excess glue, levels the surface, and leaves the wood ready for finishing.
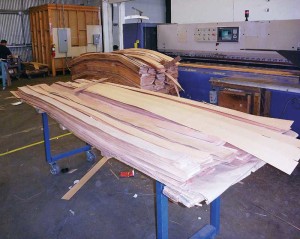
Finishing
While any wood finish can be applied, factory production allows the use of ultraviolet (UV)-cured clear coatings that contain no volatile organic compounds (VOCs) and provide a durable, low-gloss finish. If desired, wood can be stained before coating or a colorant can be put into the coating. Wood darkens as it ages, as can be seen in the rich patina of antique wood. Specifiers should allow for this when matching new construction to existing woodwork.
Some assembly required
Wood is a natural product, and variations in appearance are part of its beauty. Specifiers must communicate how much variation of color and figure is acceptable within an installation. It is difficult enough to find closely matching veneer for a piece of cabinetry or a small feature wall; the task becomes daunting to do so across a large ceiling or wall. Leaves within each panel must have an attractive composition, as must the array of panels throughout a space.
Ironically, randomly matched panels can be most challenging in this regard. In theory, dark heartwood and light sapwood randomly installed across a surface should be evenly distributed. However, a viewer’s attention is invariably drawn to distracting locations where a cluster of light-colored wood ends up next to a cluster of dark wood. These distractions can be minimized by specifying a ‘pleasing match’ with veneers selected for uniformity of color without regard to grain pattern, and working with a veneer supplier and panel manufacturer willing to work with the project team to understand and satisfy project requirements.
I am researching quonset homes and am looking at ceiling applications for a curved surface. I like the idea of flexible aluminium panels and would like more information on the size of the sheets and colors and designs, and of course the price.
Thanks,
Sharon