
Cores from cans
Almost all wood panels are made with a thin veneer, selected for aesthetics or other characteristics, adhered to a core material. Published by Architectural Woodwork Institute (AWI), Architectural Woodwork Manufacturers Association of Canada (AWMAC), and Woodwork Institute, the 2009 Architectural Woodwork Standards (AWS) is a reliable reference for most architectural woodwork. It lists plywood, solid lumber, and composite wood products such as particleboard.
New core materials, however, are entering the market more rapidly than can be assimilated into consensus standards. Examples include non-wood bio-based materials, resinous and composite products, and sheet metal. In particular, aluminum has been proven in use around the world and offers many features not associated with wood-based cores. This innovation is the product of advances in metallurgy, adhesives, and digital fabrication techniques. (See the article, “Getting off the Rectangular Grid,” by Mercolino, Chusid, and Lee Eisner, in the May 2010 issue of The Construction Specifier. Visit www.constructionspecifier.com and select “Archives.”)
Aluminum weighs 2.8 and 4.4 kg/m2 for 1.02- and 1.63-mm (0.57 and 0.90 psf for 0.040- and 0.064-in.) thick sheet respectively, about a quarter the weight of 20-mm (¾-in.) thick wood-based cores. Weight savings cut dead load on the ceiling suspension system and the building structure. More significantly, lightweight panels are easier to handle; panels can be larger than wood-core panels, yet still lifted by just one or two people. Torsion spring clips for ceiling and lift-on brackets for walls allow non-progressive installation, and panels can be removed to commission or service equipment and utilities.
In addition to being non-combustible, aluminum cores are unaffected by moisture. This means they do not support mold and, because they do not warp or twist due to changes in humidity, they can be installed before a new building has dried out or even at exterior locations.
Veneered aluminum core can be digitally fabricated with high-speed equipment to produce curves and tessellations. Perforations, which provide both a design element and noise reduction, can be produced in an almost unlimited variety of perforation sizes, shapes, and patterns.
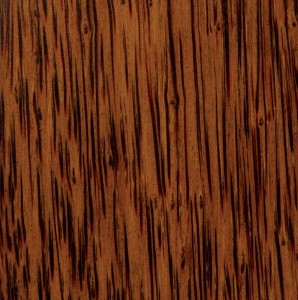
Photo courtesy Plyboo—Smith & Fong
An ever-green material
Intrinsic environmental qualities are part of wood’s natural appeal. People generally feel healthier and happier surrounded by natural materials—a phenomenon called ‘biophilia.’ Forests generate oxygen, control erosion, provide habitat for wildlife, and can be managed to sustain both the ecosystem and an economic system.
New methods of producing thinner veneer make increasingly efficient use of forest products—a cubic meter of wood can yield 1400 m2 of veneer (435 sf of veneer per 1 cf of wood), 0.7 mm (0.03 in.) thick or less.
Wood panels can help a project earn points within the U.S. Green Building Council’s (USGBC) Leadership in Energy and Environmental Design (LEED) program, including the following credits:
Materials and Resources (MR) Credit 3, Materials Reuse
Wood panels with traditional cores can be difficult to remove without damage for reuse in another building. However, the light weight and accessibility of wood panels with aluminum cores make it practical to salvage and reuse panels.
MR Credit 4, Recycled Content
Veneer from salvaged timbers and palms (discussed later in this article) may also contribute to recycled content. Panel cores can be 99 percent post-consumer aluminum recycled primarily from beverage containers. If it becomes necessary to remove a panel from a building, aluminum has the added advantage of being readily recyclable without loss of metallurgical value.
I am researching quonset homes and am looking at ceiling applications for a curved surface. I like the idea of flexible aluminium panels and would like more information on the size of the sheets and colors and designs, and of course the price.
Thanks,
Sharon