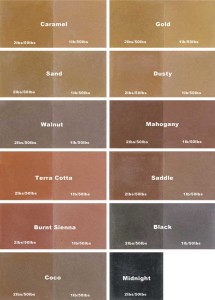
The floor is prepared by grinding off old mastic, underlayment, or any loose or crumbling concrete. Holes and cracks should be patched, with shallow problems often repaired using the same overlay material as for the floor finish. The slab should be tested for excessive water vapor emission. Depending on the manufacturer’s recommendation for the specific overlay being used, slabs with high moisture content may require special preparation, such as the use of an extra primer application of a moisture-insensitive epoxy before the regular sanded primer.
Epoxy primer is applied, and sand is broadcast onto it to provide a key for the mechanical bonding of the overlay. After it cures, excess sand is removed and the floor is ready for the topping.
The overlay can be used in its raw or natural state, or integrally colored. Color dosage can be varied to a degree, for more or less intense hues. Since overlay base color tends to be light, integral colors may be brighter and more saturated than normally seen in colored concrete. Some colorants are packaged in pre-measured quantities corresponding to a one percent dose in a single bag of overlay mix. One or two packages can be used per bag, depending on the floor’s desired look.
The ability to dose accurately, combined with general bag-to-bag consistency of premixed products, makes it possible to reasonably replicate a color from one location to the next. This is valuable when designing for consistent branding in multiple locations, such as a national store chain or franchise.
Integral color is usually made from mineral oxide pigments. These types of materials have a long track record, and are considered colorfast. They are compatible with both interior and exterior uses.
If a new concrete slab is being designed with integral color, substitution of a colored top layer may be more economical than pigmenting the slab’s entire depth. The choice would also depend on whether there is a desire for exposed coarse aggregate, a component of concrete generally absent in overlays. Special decorative aggregate can be seeded into the surface of either concrete or overlay, and ground off for interesting effects.
Pour on the floor
Once the material is mixed, it is poured onto the floor and spread. Thin layers can bond effectively and are durable. Some products can be applied as thin as 3 mm (1/8-in.) over the slab’s highest point.
It is also possible to pour multiple colors on a single floor. Areas are dammed off with adhesive-backed foam weatherstripping applied to the floor. Overlay is flowed up to the stripping. After the topping cures, the foam is removed, and the second pour can be butted-up against the first. This technique allows for smooth curving lines of contrast and elaborately colored designs.
The curing time of overlays varies. Some are based on fast-setting cements such as calcium sulfo-aluminates, and can cure to polishing strength in 24 hours or less. Others may cure hard enough to walk on—17 MPa (2500 psi) within 24 hours—but not be hard enough to polish for 28 days.
Certain overlays form a polymer cap on the surface, designed to aid curing. Before the regular grinding and polishing sequence can begin, this tough skin must be ground off the cured overlay with aggressive abrasives.
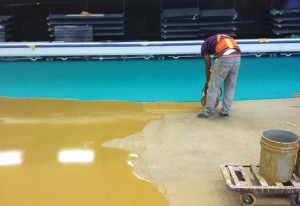
Not the same as concrete
The chemistry of self-leveling overlays is different from concrete. There are varying degrees of polymer modification. Products based on non-portland cements may produce little or no calcium hydroxide (i.e. lime) by-product—an important factor in the chemical densifying treatment associated with polishing.
Due to these differences, materials formulated for working with concrete may not perform as expected with overlays. Colorants have been observed to shift hue because of the difference in chemistry. Conventional densifiers may not properly react.
However, materials specifically formulated for compatibility with overlays are emerging. Dyes are the colorant of choice for polished concrete, and can be used the same way on an overlay, or in addition to integral color in the overlay. A dense overlay may not accept conventional acetone-based concrete dyes. Specialty dyes have been developed using an alternative, non-flammable, low-volatile organic compound (VOC) solvent that penetrates more effectively and deeply. For OPC, dye is usually applied after the 200-grit grind before densifying, but with the speciality dye, due to its unusual depth of penetration, the standard sequence of operations should be altered and the surface densified before dyeing.
Densifiers are surface-applied as a liquid. They react with lime in the concrete and grow additional cementitious materials that fill in the pore structure and harden the surface, improving the ability to take a polish. Densifiers formulated for concrete may not react effectively with some overlays. To ensure proper reaction between materials, and promote more predictable results in coloration, it is wise to specify colorants (integral color and dye) and densifiers tested for compatibility by the overlay manufacturer.
Similarly, although concrete polishing is the model for overlay polishing, following a similar sequence of ever-finer diamond abrasives, the operator techniques may be different. An overlay-experienced applicator is recommended.