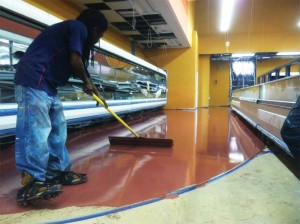
Local color
Dye can be spray-applied to both natural and integrally colored overlays; it is then allowed to soak into the surface. If added over integral color, dye can deepen existing color, add darker accents, or subtly alter its tint.
In a recent residential project in Florida, for example, the color sample was a piece of steel-gray stained glass. The manufacturer was able to match it with a combination of a one percent dose of integral black mixed into the overlay, and a blue dye application during polishing.
Dyes can also be selectively applied using adhesive-backed stencils. Intricate designs are possible with multi-layer, registered stencils, including graphics and detailed pictorial effects. (This technology’s full possibilities are beyond the scope of this article.)
Dyes may be degraded by long-term ultraviolet (UV) exposure, and are not considered suitable for exterior applications.
After densifying and dyeing, the polishing process is continued to very fine abrasives, often up to 1500 grit. When properly performed, a floor can be brought to high gloss with mirror-like reflections.
Specifying protection
One property common to exposed cementitious floors—polished concrete and overlay—is the need for stain protection. This class of product is a breathable sealer applied at the end of the polishing process. It deposits a thin polymer layer on the surface that resists liquid penetration, but allows water vapor to exhale from the slab. It tends to slightly deepen colors and enhance a wet look in the polish.
Stain protector’s liquid resistance minimizes staining. It can also temporarily shield against spills of acidic substances—pickle juice on a supermarket floor is the classic example—that can chemically etch the surface, spoiling the polish and potentially altering colors. However, a stain protector is not a total shield; it is only designed to provide a window of opportunity to remove spills. Manufacturers typically recommend a maximum of 30 minutes before cleanup.
Stain protector also helps keep dye color in the slab. If the protector wears out and is not renewed in a timely manner, dyes can be gradually washed out of place, lowering the saturation of color in the surface. Often mistaken for dye fading, this color loss has been observed in concrete floors, and may also occur in polishable overlays. However, these materials are still too new for most original stain protection applications to have worn off.
Prudence would suggest using experience with concrete as a guide. For concrete, manufacturers typically recommend re-application every two years, and more frequently in high traffic areas; it is reasonable to expect the same performance
on overlays.
Owners need to be informed that stain protection should be inspected yearly, either by the original applicator or other qualified professionals. Maintaining stain protection is the single most important factor in keeping a colored, polished cementitious floor looking and performing as designed.
Conclusion
Polishable overlays offer a cost-effective solution for re-finishing damaged concrete floors into new, decorative, exposed concrete surfaces. They are sufficiently ‘concrete-like’ to provide similar performance benefits, but have a range of subtly different looks. Due to the ease of pigmenting them before application, overlays bring the special qualities of integral color to existing slabs, an option previously unavailable. Combined with dyeing and polishing options, this system has quickly evolved into a durable way to make any floor into a designable surface.
One of the most intriguing aspects of the recent development of polishable overlays is the speed with which new techniques are being discovered and explored. Three years ago, these products were used as substrates. Now, they are a medium for creating permanent graphic art on floors. Like a great deal of the advances in decorative concrete, this is being driven by the imagination of applicators. It is a field worth watching, both for the new techniques being pioneered and materials being developed to enable creativity.
Les Davis is president of the AmeriPolish Inc. (formerly American Decorative Concrete Supply Company), manufacturers of products for coloring and polishing cementitious overlays and polished concrete. He can be contacted via e-mail at les@ameripolish.com.
Gary Vidal is inside sales manager for AmeriPolish Inc. He is a veteran concrete polisher, and was the first contractor to field test the first acetone-based concrete dye before it went on the market. Vidal can be contacted at gvidal@ameripolish.com.
Steven H. Miller, CDT, is an award-winning writer and photographer, and a marketing consultant. He specializes in issues of the construction industry. Miller can be reached at steve@metaphorce.com.