Hail launcher
Historically, a roofing product’s hail resistance has been tested by dropping steel balls or darts onto it. The specific procedures vary between U.S., Canadian, and European organizations. In this country, two primary entities perform testing for code approval—Underwriters Laboratory (UL) and Factory Mutual Global (FMG). The respective standards are UL 2218, Impact Resistance of Prepared Roofcovering Materials, and FM Class I 4470, Approval Standard for Single-ply, Polymer-modified Bitumen Sheet, Built-up Roof (BUR), and Liquid-applied Roof Assemblies for Use in Class I and Noncombustible Roof Deck Construction.
UL and FM use steel darts to impact targets, typically at room temperature. Other organizations, such as ASTM, have developed impact tests that use steel darts (i.e. ASTM D3746, Standard Test Method for Impact Resistance of Bituminous Roofing Systems). Within the last few years, greater consideration has been given to impacting targets with ice spheres. Prior research by one of this article’s co-authors has also reviewed the issue of ice spheres versus steel darts. The use of the former, obviously, comes closer to replicating what occurs during a real hailstorm.
A key factor in performing the test is to have reproducible impact energies with each shot of ‘hailstone.’ The hail gun or launcher (Figure 3) propels ice spheres by employing the quick release of compressed air from a tank to a barrel. To achieve reproducibility, several factors have to be taken into consideration. Since consistent air pressure is required for each shot, it must be controlled to 70 Pa (0.01 psi).
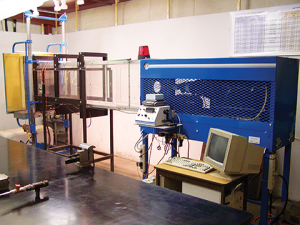
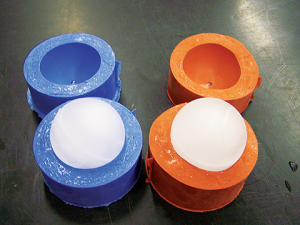
Molds for ice spheres are fabricated using precise-diameter steel spheres (Figure 4). Each ice sphere of a given diameter is then weighed to 0.01 g before each shot. Laboratory-grade barrels or tubes with precise internal diameters are also necessary to develop consistent impact energies. Basically, the charge (i.e. air pressure), the quick release valve, and the bullets (i.e. ice spheres) require precise fabrication to achieve reproducible impact energies.
The ice spheres are initially weighed to 0.01 g and then placed in the barrel, similar to a lead shot for a muzzle loader. As the ice sphere is pneumatically launched toward the target, the velocity is measured with a ballistics timer. The kinetic (or ‘impact’) energy is then calculated; minimum kinetic energies listed by NBS are maintained within a tolerance of minus zero, plus 10 percent.
Understanding the EPDM targets and impact procedures
Manufacturers provided a total of 81 test targets constructed with 1524-µm (60-mil) non-reinforced EPDM for impact testing (Figure 5). There were 25 ‘new’ samples and 20 samples heat-aged for 1440 hours at a temperature of 116 C (240 F) at Cascade Technical Services (Hillsboro, Oregon). The 36 samples for the field-aged/exposed category were collected from six states across the country, and they ranged
in age from five to 20 years (Figure 6).
Each target and substrate was vertically mounted. Hailstones measuring 38, 51, 64, and 76 mm (1 1⁄2, 2, 2 1⁄2, and 3 in.) impacted the targets at a 90-degree angle at velocities listed by NBS. To replicate severe weather conditions, such as cold rain during a hailstorm, the test targets were sprayed with water at 4 C (40 F). Prior research and experience has shown roof assemblies exhibit different levels of impact resistance depending on surface temperature.
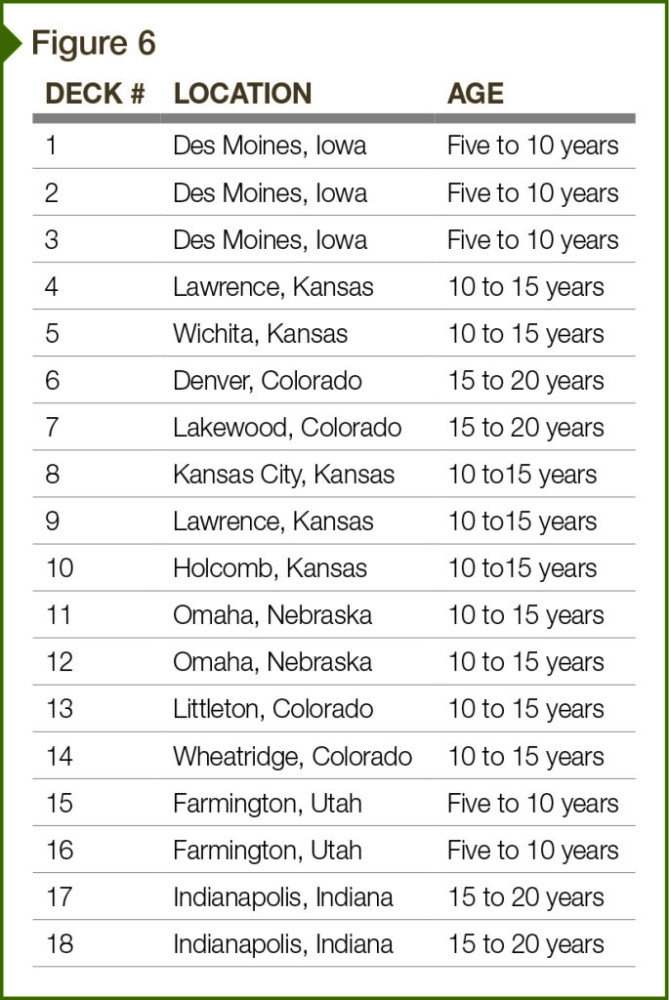
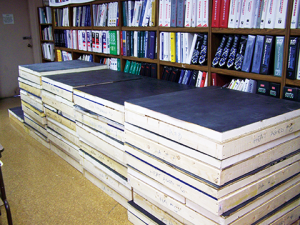
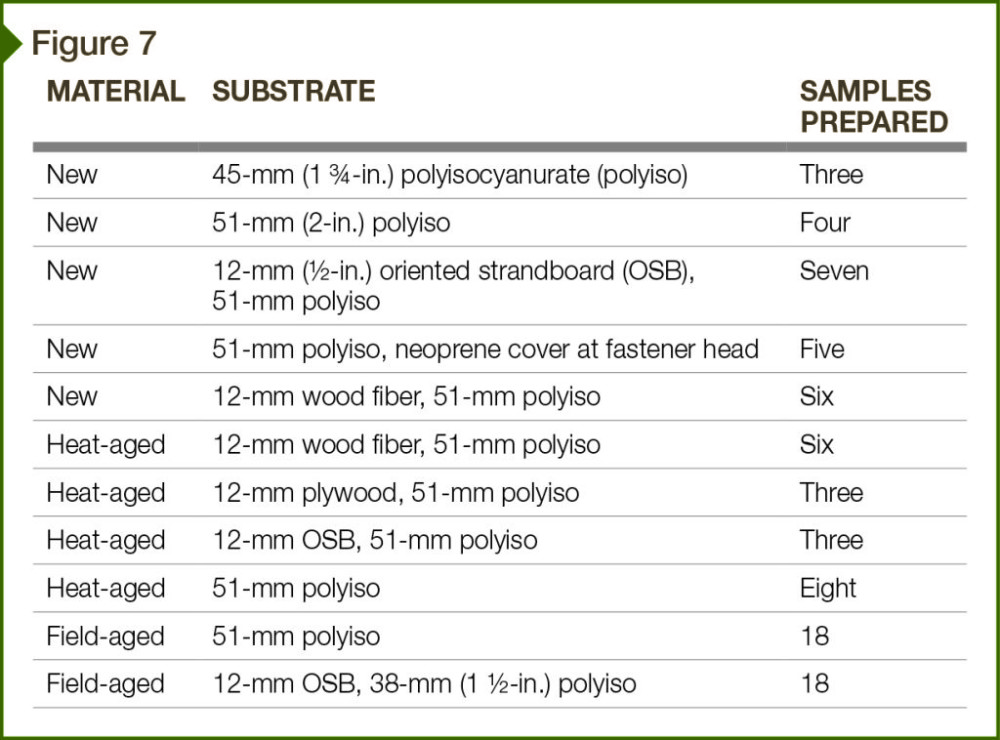