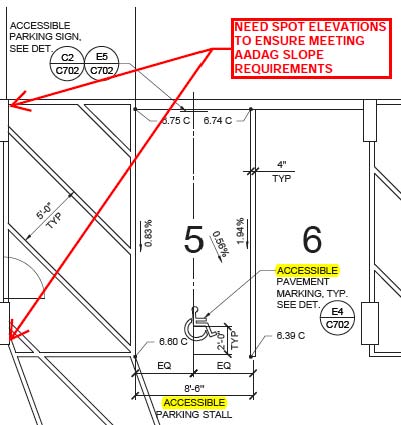
Managing coordination
Coordination, or discrepancies due to lack thereof, is the most difficult quality element to manage. Every time you think you have checked all the things that could go wrong, something new occurs.
The first level of coordination involves the usual standard coordination exercises. These include confirming:
- electrical has provided the correct power characteristics for mechanical equipment;
- structural has provided supports for mechanical and electrical equipment loads;
- mechanical has taken into consideration the heat load from electrical equipment;
- electrical has provided a power source for landscape irrigation controllers and fire alarm control panels; and
- civil or mechanical has provided a water supply stub for landscape irrigation.
The second level of coordination involves items such as confirming civil pipe sizes and locations for water, sewer, and drainage going into the building match those shown by mechanical and plumbing coming out of the building. Sometimes, coordination appears to be more along the lines of wishful thinking, when one consultant includes a “See XYZ” on the drawing, and nothing is shown on the consultant’s XYZ drawings when you go to find them. Anytime I see “See Specs” or any other reference, I always check first to see there is actually information there, and then whether it matches or coordinates with the reference document.
The next level of coordination is a combination of coordination, constructability, and usability. These items are difficult to catch prior to construction, but effort should be made to think about how we design buildings to prevent these coordination issues.
In one concrete high-rise residential condo project, the entry to a U-shaped kitchen was an opening through a concrete shear wall, with the refrigerator/freezer located on the opposite side. During construction, the width of the kitchen was slightly reduced to accommodate plumbing. When the appliances were installed in the lowest-floor unit (floors were still being poured above), it was discovered the refrigerator was 927 mm (36 ½ in.) wide, but the kitchen opening was only 914 mm (36 in.) wide. So the contractor turned the refrigerator sideways and pushed it into the kitchen. However, when he tried to turn it to move into place, the distance between the countertops was less than the diagonal dimension of the refrigerator. The contractor ended up having to widen the kitchen opening by chipping concrete for a large number of units. He also discovered because the refrigerator doors would only open just past 90 degrees, and because of the shelves on both the refrigerator and freezer doors, it was almost impossible to remove the drawers for cleaning.
In a hospital renovation project, a large air-handler was located above the ceiling in a 2.44-m (8-ft) wide corridor. Both corridor walls were fire-rated and had to extend to the floor above. The ceiling design was a 0.61-m (2-ft) square grid, and almost every single ceiling panel was fixed, because of registers, downlights, fire sprinkler heads, speakers, or strobe lights. To access the air-handler for service, a fire-rated access door needed to be added through the corridor wall above the ceiling in a room adjacent to the corridor.
In this same project, the new first-floor emergency room was being installed in a former administrative area that was part of the oldest wing of the hospital. We coordinated the removal and relocation of all utilities shown on the original mechanical/electrical/plumbing (MEP) drawings, including renovation drawings. When the contractor was demolishing the existing partitions, he discovered a 9.5-mm (8-in.) cast-iron roof drain located right in the middle of the new 2.44-m (8-ft) wide corridor.
Fortunately, the floor-to-floor height to the second floor was tall, and the contractor was able to transition over to miss the corridor. Unfortunately, he could not move the line in the basement operating room. He had to remove the recessed operating room light fixture, and have the plumber (who luckily had a slight build) crawl on the plaster ceiling framing after operating room hours to install the transition back to the original pipe. We discovered it was common practice at the time this wing was designed for the architectural, not the mechanical, to show all roof drainage lines. When we reviewed the original architectural drawing, we found the roof drain.
Organizing and managing quality in your firm
The ideal results of a successful quality program should be to have the quality built in by your team, including your subconsultants. The goal is to have the review completed with adequate time to make corrections. You should strive to achieve a commitment by your staff and subconsultants that quality is everyone’s responsibility.
I firmly believe success is enhanced by having a ‘quality champion’ in your firm. That person may be responsible for designing the program and implementing it, or the designated quality manager actually performing document reviews. There are several factors affecting your decision on program organization. If your principals manage their own projects, and they have distinctly different project types and clientele, and you do not have a staff person with the experience or inclination to be a quality manager, then you should establish the requirements and quality expectations, and enforce consistent quality among the principals.
However, if there is a staff person with the experience and inclination to be the quality manager, and the principals are willing to accept this second-party review of their projects for the sake of improving quality consistently firm-wide, the program should be organized along these lines. Another alternative is to use a third-party reviewer.
A quality program should be based on a set of production standards. All of the production standards I have worked with were adapted from what was then the Northern California AIA Chapter’s Recommended Standards on Production Office Procedures created in the early 1970s. If your firm does not have its own standards, I recommend you adopt or adapt the nationally recognized NCS as your own. (If you do not agree with portions for your practice, you can always modify them.)
Once you have adopted a set of standards, you should disseminate them to your staff for everyone to follow. You should also hold training sessions with newly hired staff. Undoubtedly, there will be disagreements over certain aspects of the adopted standards. For example, I believe it is important to give the contractor some dimensional flexibility during construction by leaving open
a secondary or tertiary string of plan dimensions. You should leave out an unimportant dimension from the standpoint of design or room function. At my former firm, there was one person who argued strongly to close all dimension strings. He had encountered a situation in construction that supported his opinion.
You also need to devise a way of measuring your quality level, and to establish a goal for all projects, firm-wide. At a previous firm at which I worked, the chief contract administrator kept track of project change orders by source. With the information segregated in a spreadsheet, he was able to tally the total cost of all changes by their sources at the end of a construction project, thereby measuring the quality of the CDs. The source categories he used were:
- Owner-initiated;
- Found or unforeseen conditions (common with renovation and weather delays);
- Code-required;
- A/E-initiated;
- Omissions;
- Errors; and
- Other.
The guideline the firm used was if the total change cost of A/E-initiated, Omissions, and Errors was one percent or less of the original construction cost, then we had produced a ‘good’ set of CDs. If that combination exceeded two percent, we considered the set to be ‘inadequate.’ These three categories are controllable by the architect/engineer. As a start, I suggest you could analyze a number of your recent projects to measure how well you have done against this guideline. You could then determine, based on your practice and your experience (and the number of return clients), whether you want to adjust this goal.