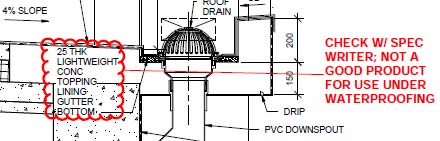
Management tools
Some management tools can assist you in your quest for perfection.
Checklists
One method for starting your own quality-control checklist is to document the items that have been problematic for your firm, organize the list, and use it to check current and future projects. We did this at my former firm, with my “Quality Control Coordination List” as a start. The chief contract administrator added the items he had accumulated over the years, organized the combined list, and put it into a spreadsheet separated by discipline. We were then able to disseminate the subconsultants’ lists on projects, so they understood what we expected of them to avoid repeating past challenges.
There are numerous problems with using checklists as the primary quality management tool. If the checklists are not comprehensive enough, items will be missed. If they are too comprehensive, your colleagues may just roll their eyes and check everything as ‘OK,’ without actually looking. The checklists may also include items meaningful to the author, but unintelligible to anyone else. They may also cause the person performing the document review to look only
at the checklist, and consequently miss items.
I use checklists after I have completed my detailed review of the documents. I have to perform an additional partial review of the documents, but I find this method frees my powers of observation during the original review.
Insurance carriers
One’s professional liability insurance carrier is also a good source for recommendations, based on its knowledge of issues causing lawsuits and losses for its clients (i.e. you). As a little additional incentive, efforts to formalize a quality control program can, in some cases, earn a discount on next year’s liability insurance premium.
Real-life experiences
It can be beneficial to lead your project production team, including subconsultants if appropriate, on a ‘lessons learned’ walkthrough of the construction in progress. You should discuss things that worked, as well as things that could have worked better. On-the-job training in contract administration for a project they helped produce can be a mutually beneficial professional development opportunity for staff and management. Also beneficial are presentations at brown-bag lunches in your office, with photos or videos.
AIA and CSI resources
Other tools for quality control management can include AIA D200, Project Checklist, and the association’s Best Practices, specifically Chapter 12 (“Quality Management”), which includes:
- “Less rework equals more productivity and quality” (12.01);
- “When more is less: Why do we draw so many sheets?” (12.01);
- “Risky business: Managing the top 5 risks” (12.01);
- “Keeping tabs: Using document audits/peer reviews” (12.01);
- “Managing quality in the design development phase” (12.03); and
- “Schematic design phase quality management” (12.03).
The Spring 2008 edition of AIA Practice Management Digest also includes some excellent papers on quality management, including one on ISO 9001.
As mentioned, quality is also discussed in CSI Project Delivery Practice Guide, Section 8.9 (“[Design] Quality Assurance/Quality Control Requirements”).
The ideal quality manager
Certain attributes are important for a quality manager, but experience in production is among the most critical. To gain the respect of the project team, they must believe the person reviewing the documents knows what they are talking about. They also need to have a thorough knowledge of your production standards to enforce them.
Quality managers also need experience in writing specifications. To be a good specifier, you often have to know the right questions to ask the project architect, or even make some of the required decisions yourself. Specifications are the contract administrator’s field manual, and CA experience is where the rubber meets the road, and where all the hopes and dreams of the designer meet the practical limitations of the contractor.
The ideal quality manager has a tendency to be detail-oriented—this is not a role for someone who is going to gloss over small mistakes. (Ultimately, it should be the project team’s responsibility to decide which items get corrected, based on the magnitude of the item and the timeframe to make the corrections.) He or she also requires a sense of ‘design appropriateness.’ Although it is not my job to be a design critic, there have been times when I asked the team if they really knew how something was going to look.
How do I work?
When I review a set of documents, I review the architectural in detail, the civil fairly thoroughly, and the structural, MEP, and landscape for mainly coordination items. Everything I review, I check off with a yellow marker; items I comment on receive a red marker. When there is reference to a detail, I go to that sheet/detail and yellow-mark the number after reviewing the detail. When I have finished reviewing a set, all unmarked detail references need to be cross-referenced.
I begin at the cover sheet and ‘read’ the set like a newspaper to the last page. Where there are references to the specifications, I follow that reference and confirm the coordination. I do the same with all references to another discipline. I check the Drawing Index against the actual sheet titles to ensure they match, and I do the same with the Specification Table of Contents. My goal is to mentally build the building.
When my review has been completed, I meet with the architectural project team and go through the entire red-marked set. I believe it is important to debrief the entire team (at least the architectural team) to gain the most from this educational opportunity. Frequently, some team members are unaware how their work affects the rest of the CDs. The team is responsible for copying and distributing the subconsultants’ red-marked sets to them. If I do a subsequent review on the same project, I request the previous mark-up back to back-check the corrections and provide a base for the next review.
About two years ago, I began using software to review the documents and summarize my comments. The program provides many tools allowing great markup flexibility, and the comments are easily summarized. Both the marked-up drawings and specifications are in pdf format, and the comment list is hot-linked to the drawings. This feature allows rapid access to locate the comment on the drawing. The program also allows for many windows, so I can start with the site plan sheet, window in the floor plan sheet, then the door schedule sheet, and then the door details sheet. The particular software program provider I chose also allows users to create a digital copy of the review set by simply renaming it, speeding up the process of distributing comments to subconsultants.
Conclusion
A quality control program for construction documents takes some planning, effort, and dedication. Time must be allocated for this task in the project schedule, and money must be budgeted for staff or third-party reviews. All other aspects of quality should be positive—for the client, the contractor, the project, and the members of the design team.
The opinions expressed in Specifications are based on the author’s experiences and do not necessarily reflect those of The Construction Specifier or CSI.
Alan L. Atkinson, CSI, CCS, AIA, is a registered architect in Hawaii and Washington. He is a Member Emeritus of the American Institute of Architects (AIA) and a member of CSI’s Honolulu Chapter. After retiring as a senior associate with Architects Hawai’i Ltd., he started his own firm, Atkinson Quality Control, and has been in business for the last seven years. He has more than 50 years of experience in all phases of architecture, with a special emphasis in quality control. Atkinson is experienced in construction administration, project management, and the preparation and coordination of construction drawings and specifications. He has written specifications and performed quality control reviews for a variety of residential, commercial, hotel, medical, industrial, and institutional projects. Atkinson can be reached via e-mail at atkinsonalan@hawaiiantel.net.