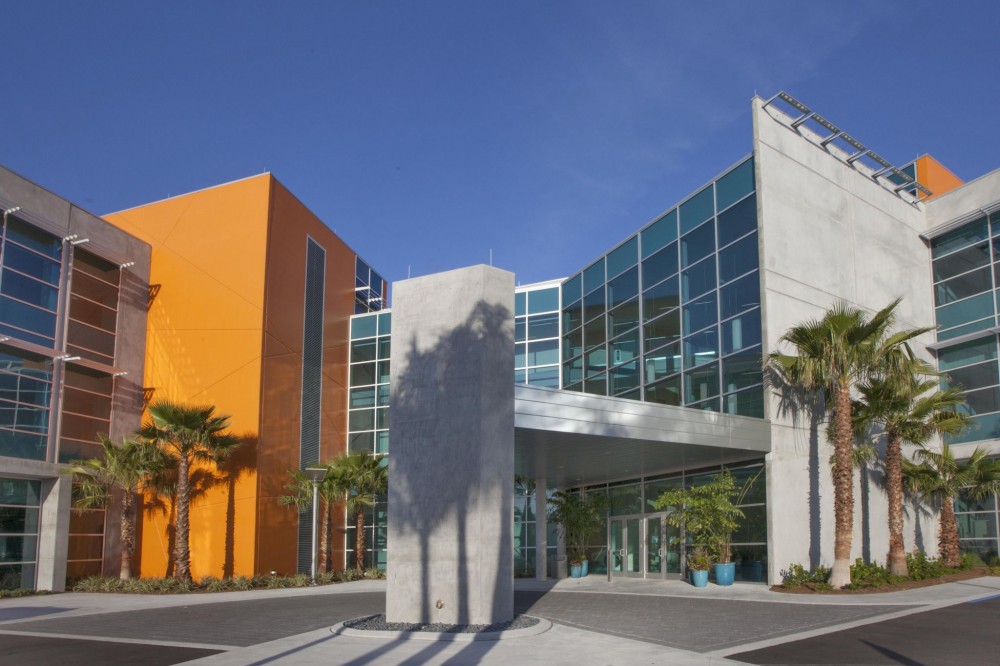
by Kristin Dispenza, CSI
Materials with origins in engineering or industrial applications often become embraced for their artistic or architectural potential. For example, weathering steel was developed in the 1930s for railway coal wagons, but eventually began appearing as cladding on high-profile buildings in the 1960s—its signature brand name, Cor-ten, is now universally recognized among designers.
Such break-out success is not uncommon in architecture. After all, experimenting with the aesthetic properties of an otherwise basic or practical building material has always been a hallmark of the discipline; this tendency only gained momentum in the 20th century when the concept of functionalism was introduced. In the modern and post-modern eras, the line between form and function has been frequently crossed.
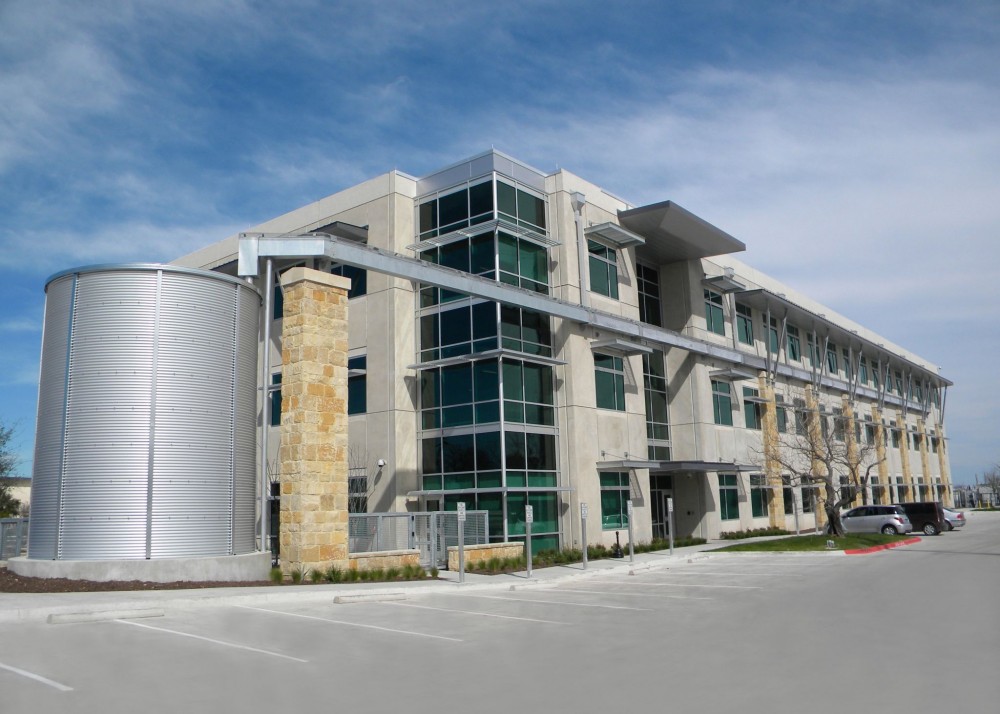
Surprisingly, tilt-up construction, a method regularly selected for industrial and other plain applications following its surge into mainstream building during the 1960s and 70s, did not begin as such a general construction solution. California architect Irving Gill pioneered the technique in the 1920s, reportedly inspired by factory assembly lines. In the true modernist tradition, he refined a planar, undecorated aesthetic based on engineering efficiency.
In short, tilt-up construction was identified as an efficient and effective method for raising a complex concrete façade without the tedious vertical forming process. Gill’s contemporaries capitalized on his method of erecting modern concrete façades with even greater efficiencies. Wartime economies, however, tipped the scale in favor of tilt-up construction’s ease of use, speed of erection, and low cost. By mid-century, it had come to be used almost exclusively for low-cost housing and big-box buildings—its reputation as a ‘warehouse’ material became entrenched.
Application evolution
There are good reasons for tilt-up construction’s dominance in the building of rigid-wall, flexible-diaphragm large-box structures. It is easy to use the vast floor slabs of these structures for casting wall panels, and simple for cranes to then hoist them into position on buildings that have relatively plain perimeters and uncomplicated wall envelopes.
Nevertheless, tilt-up construction also has the capacity to deliver multi-story, irregularly shaped, complex projects—a fact increasingly embraced by architects over the past two decades. The ability to easily and creatively deliver form is contributing to the resurgence of craft—essentially, because one of the greatest benefits of tilt-up is speed, there is more time to focus on quality.1
Tilt-up is now regularly considered for almost every project type, depending on the region, says Jeffrey Brown, AIA, of Powers Brown Architecture.
“From warehouses and functional origins, tilt wall has begun to transverse building types at an amazing rate,” he explains.
The Tilt-up Concrete Association (TCA) recently conducted its 23rd annual achievement awards, honoring projects representing an increasing diversity of building types constructed with site-cast tilt-up concrete. A select few, profiled in this article, provide an understanding of both the visual and functional possibilities attainable with this delivery method.
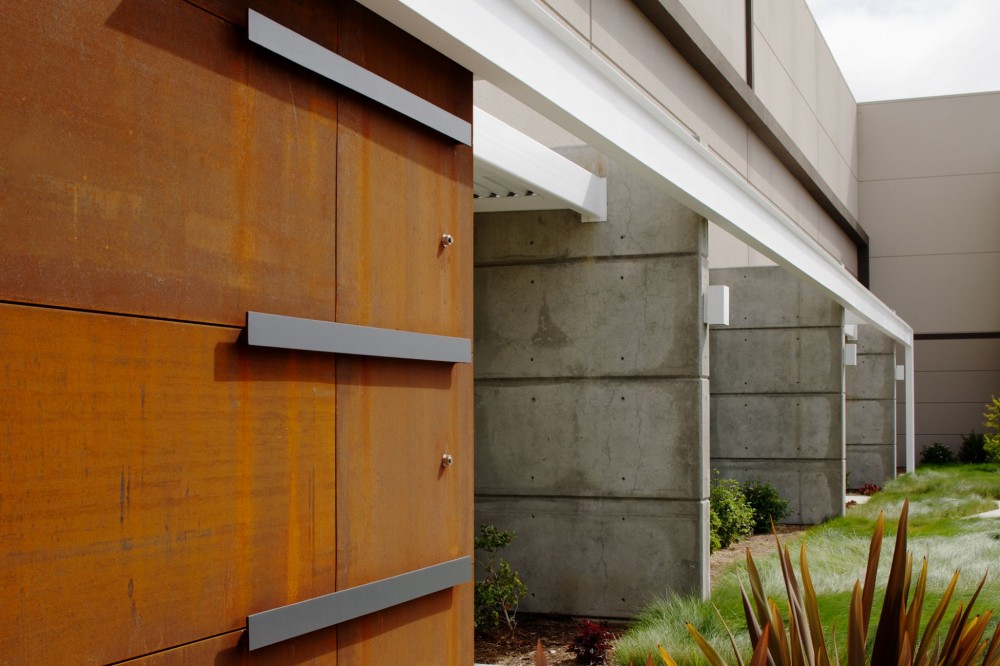
“Inherent to the material and construction method, tilt-up establishes an incomparable blend of structure and aesthetics,” says Jim Baty, TCA’s technical director. “Where tilt-up has been, and where it is currently headed, is a dynamic blend of architects desiring form and function that are unified, engineers capitalizing on the plasticity and componentry of the raw materials, and contractors visualizing the modification of both surface and space to produce buildings no longer constrained by the challenges of securely assembling material components at unsafe heights or in awkward positions.”
New levels of artistry
Tilt-up’s familiar planar panels lent themselves to early modernism because of their inherent ability to define sleek, machine-inspired forms. As tilt-up construction furthers its inroads into high design, it is this ability to shape a planar composition that is most often explored.
Chico’s National Store Support Center
Volumes made with tilt-wall panels can be interspersed with contrasting forms, as Gora/McGahey Architects did for the Chico’s National Store Support Center (Building 10), a 13,615-m2 (146,555-sf) office project in Fort Myers, Florida. The building’s exterior features cantilevered members, tapered panels and compound shapes.
The building also sports bright colors and a modern, smooth surface finish to emphasize its contemporary character. Panels were designed to remain in an ‘as-cast’ state to offer an exposed concrete look; nearly all were coated with a clear sealer, which required the panel surface to be flawless.
Dalchau Service Center Building D
Where tilt-wall panels are applied to structures having less differentiation in massing, they can be combined with different building materials, as was successfully done by STG Design on the Dalchau Service Center Building D, a 7335-m2 (78,952-sf) office building in Austin, Texas. Certified Silver under the Leadership in Energy and Environmental Design (LEED) program, the building melds tilt-up concrete with various metal and glass components to achieve visual balance.
Grandview Business Centre
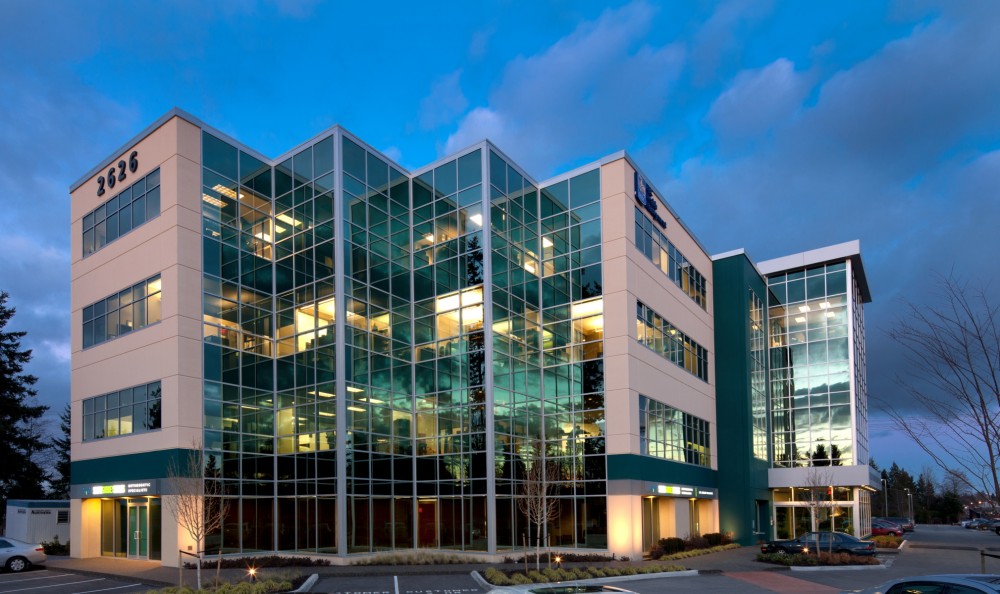
North of the border, the Grandview Business Centre in Surrey, British Columbia, also marries tilt-up concrete with various building materials. The 6689-m2 (72,000-sf) multi-tenant commercial office building was designed by Ionic Architecture. It is located two blocks from Grandview Corners, the largest unenclosed retail development in British Columbia.
This retail project needed a design that was volumetrically dynamic, so the structure’s basic rectilinear form was stepped back at the southwest corner. Glass and steel were used on this portion of the building, as well as on the entrance tower, enriching the material palette. The tilt-up structure interfaces seamlessly, both functionally and aesthetically, with the glass and steel.
Gordon Holdings Building
Tilt-up planes on a building’s façade interface well with curtain walls, ribbon windows, spandrel panels, and punched openings. Consequently, there are many opportunities to employ a complex architectural vocabulary. Intergroup Architects, designers of the Gordon Holdings Building, used tilt-up panels to break up large wall surfaces. For the 11,092-m2 (119,397-sf) industrial building in Englewood, Colorado, a 7.6-m (25-ft) long spandrel panel frames a dramatic glazed cantilever at the entry.
Metropolitan Van & Storage
Tilt-wall panels are not limited to defining closed volumes of space; they can be overlapped or applied as freestanding elements, helping to further differentiate a building’s massing. RMW Architecture and Interiors designed large wing-wall panel extensions to create shadow and relief along the façade of the Metropolitan Van & Storage building, a 9980-m2 (107,424-sf) warehouse building in Napa, California. The wing walls are finished to resemble cast-in-place concrete and are further enhanced with 0.6-m (2-ft) edge returns and Cor-ten weathering steel accents.
North Fraser Corporate Centre
For the North Fraser Corporate Centre, an 11,584-m2 (124,693-sf) office building in Burnaby, British Columbia, tilt-up panels were used as façade elements to divide the building’s massing. Despite the technical challenge of having to construct the building on 23-m (75-ft) piles—more than 900 were used in its overall construction—Beedie Development Group was able to include detailed architectural features that are not standard for industrial buildings.
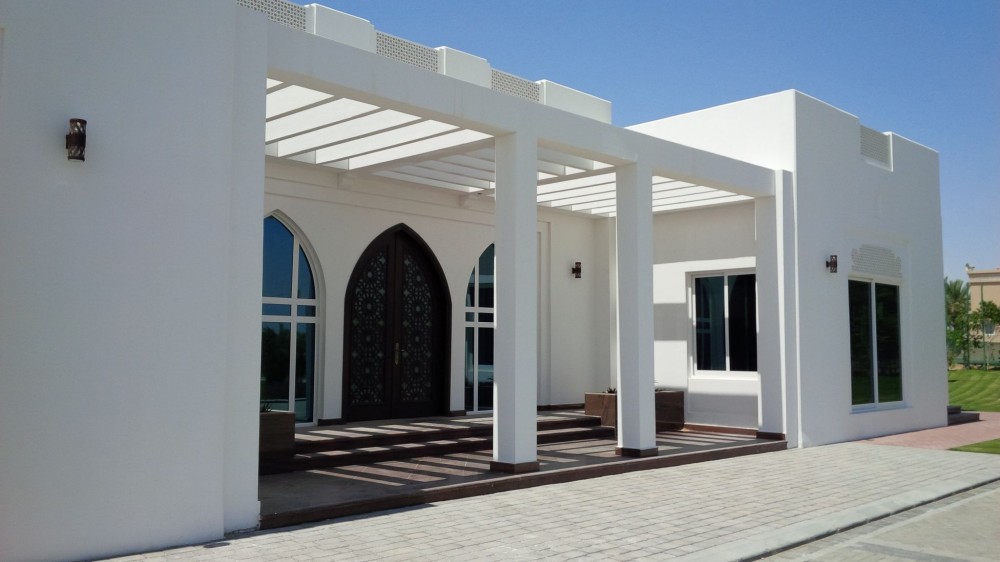
Angled tilt-wall panels extend outward from the building and articulate a series of bays. These vertical wedges of concrete are counterbalanced by window units, which form horizontal projections within each bay. Architectural detailing—such as reveals, recesses, and colorful projecting steel channels—complete the composition.
Beyond planes
Tilt-up is a form of precast concrete construction. However, unlike the constrained modularity of plant-cast panels, it is adaptable to non-modular dimensions. Not only have designers used it to clad irregularly shaped building envelopes, but they have also employed tilt-up construction methods to create architectural elements such as pilasters, achieving looks often associated with steel framing but with improved economy.
It is even possible for highly sculptural building forms to be executed using tilt-up construction. The contour of a tilt-up panel can be manipulated in plan, elevation, or both. Consequently, curved and shaped panels have come into common use, offering designers flexibility not economically practical on most projects.
Abu Dhabi villas
Showcasing this fact, 2013 TCA award-winners included vernacular buildings styles and even traditional church architecture, complete with domes and arches. SiteCast Construction Corp., built two model villas in Abu Dhabi, United American Emirates (UAE); the 510-m2 (5500-sf) single-story homes feature traditional UAE architecture, but were constructed using load-bearing tilt-up. This effort at reproducing local design was accomplished by paying special attention to forming techniques, panel joint locations, and interior wall treatments.
“Tilt-up allowed the local architecture to be enhanced by the durability and versatility of the concrete,” said the firm’s president, Shawn Hickey.
Saint Mary Coptic Orthodox Church
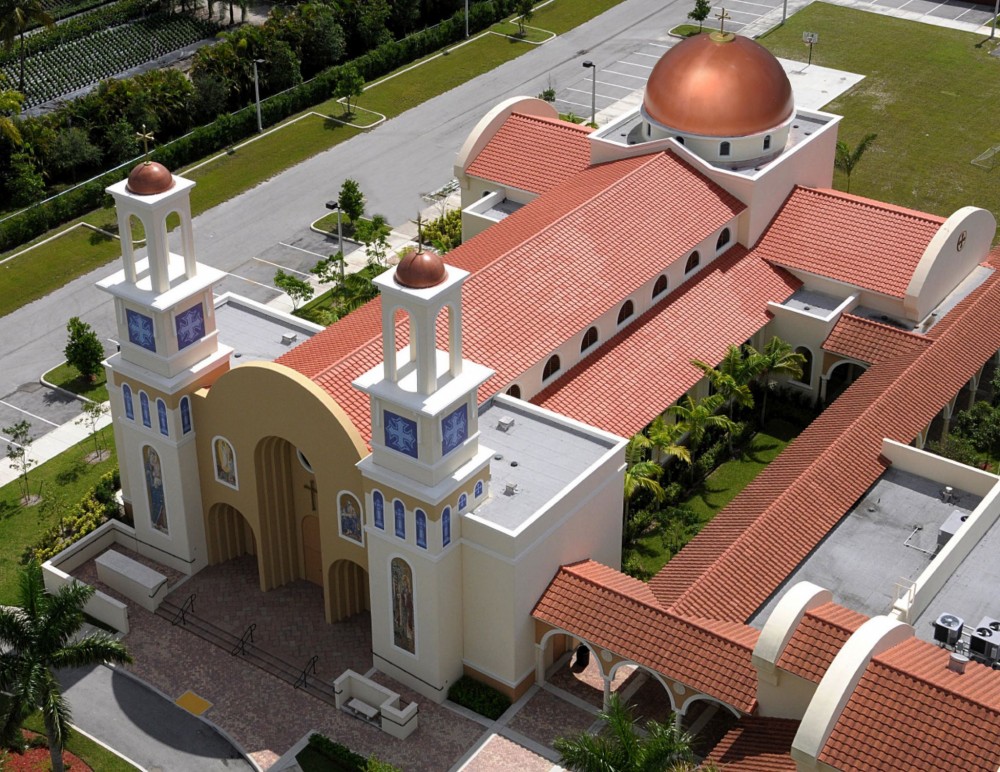
For the Saint Mary Coptic Orthodox Church, a 1277-m2 (13,750-sf) church in Delray Beach, Florida, api Group Architecture took a design that originally combined a reinforced masonry structure with metal-gauge framing, lath, and stucco at the façades, and converted it to use tilt-up construction.
The church features a full dome—9 m (29 2/3 ft) in diameter and with a weight of 46,221 kg (101,900 lb)—that was cast monolithically and lifted using tilt-up systems. Tilt-up panels also form the two church towers. Layered panels are employed to create traditional building elements such as the stepped-down, vaulted archway at the church entrance. This project demonstrates the creativity of form that can be developed using site cast panels and layering as well as structural variety to deliver intimate spaces and dramatic open spans.
Finish treatments
The varieties of finishes possible with tilt-up concrete also provide a wide range of opportunities for making a building distinctive.
Tooele Applied Technology College
Architects with MethodStudio modified the thickness of cast panels used on the Tooele Applied Technology College to achieve a more craftsman-like feel. Materials specified for this 6852-m2 (73,751-sf) educational building in Tooele, Utah, included reclaimed wood from the Great Salt Lake, corrugated metal panels, mineral rocks, and hanging pendant lights—all with symbolic importance to the community.
Tapering the panels and beveling their edges, as opposed to leaving the panels at a uniform thickness, lent a handcrafted feel to the architecture. The architects also used form-liners to impart the appearance of cedar boards to some of the panel surfaces.
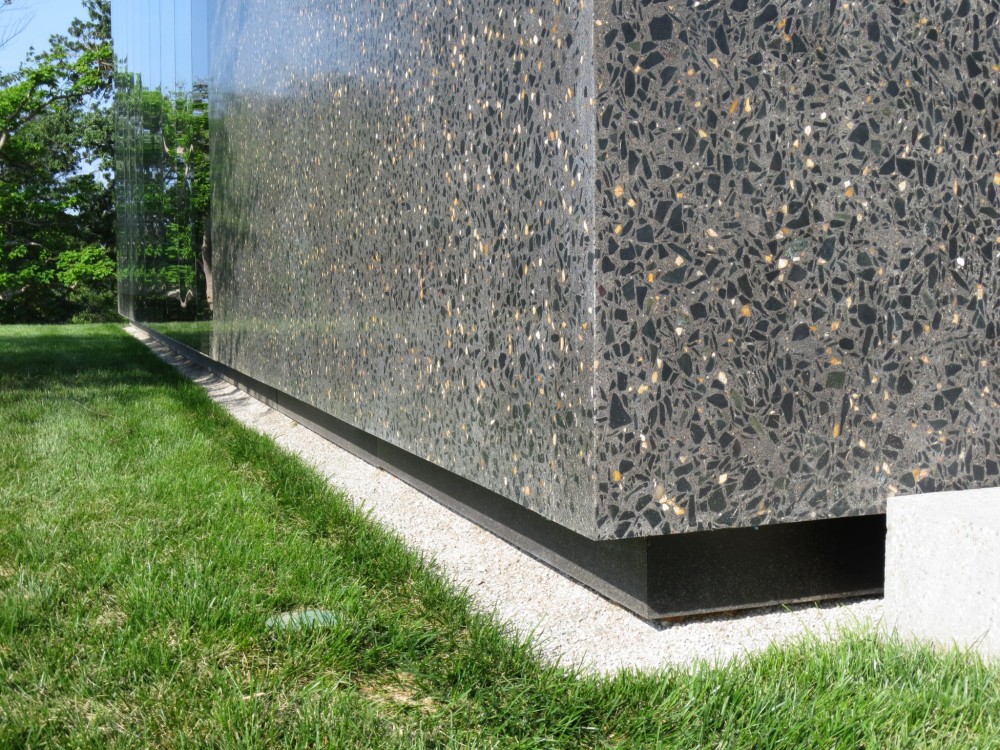
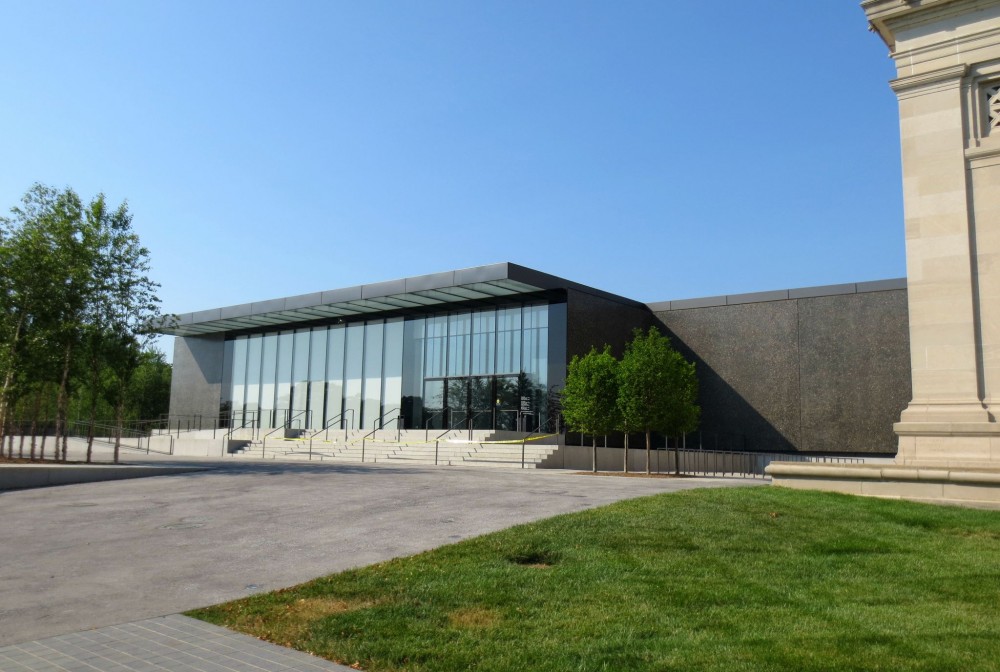
St. Louis Art Museum New East Building
Panels have often been finished using sandblasting or retarders to expose the aggregate. However, to achieve a final finish similar to granite for the St. Louis Art Museum New East Building—a 19,974-m2 (215,000-sf) addition in St. Louis, Missouri, designed by David Chipperfield Architects—the panels needed to receive a polished finish.
Panels were therefore cast with the exterior face up to facilitate higher quality grinding and polishing prior to erection. Lifting inserts installed on the exposed face of the panel had to be patched to match the surrounding finish. Building corners with 90-degree return legs were cast monolithically, requiring a 12 mm (1/2 in.) of material to be saw-cut from the finished face to expose a cross-section of the aggregates.
Panel joints were unique for a tilt-up envelope as they were designed without joint sealant and intentionally exposed at the edges. Panels had to be poured oversized and cut to exact dimensions in order to effectively reveal the aggregate. At (¾ in.), the gap left open between panels accents their rectilinear form to produce the appearance of ‘floating’ panels—they are not set on a foundation, but rather attached to the building’s structural steel. The museum addition achieved LEED Gold certification.
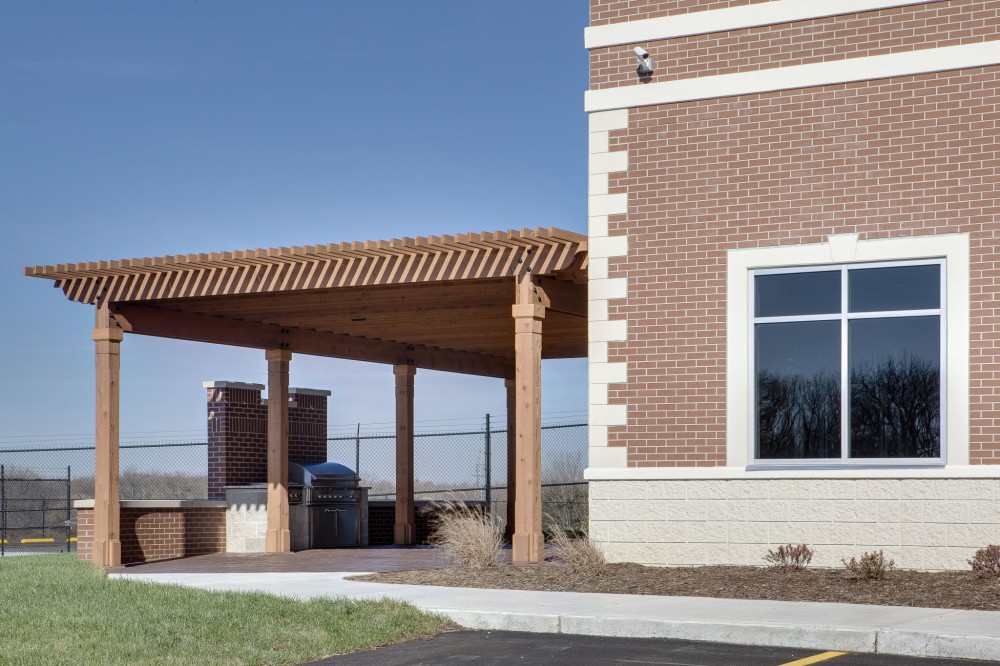
Renaissance Charter School of Manatee
Form-liners are often relied on to impart texture to tilt-up panels, including the look of modular building materials such as stone, brick, or even quoins. For the 5960-m2 (64,146-sf) Renaissance Charter School of Manatee in Bradenton, Florida, a form-liner was used to create the look of brick veneer with reveals at section borders. This provided the client with the desired look of a traditional school..
Strathman Sales Warehouse
For the 5290-m2 (56,950-sf) Strathman Sales warehouse (Topeka, Kansas), a form-liner representing split-face block was used along with formed quoins to achieve a classic look.
Grenville Mutual Insurance
The use of shapes and graphics embossed into panels can also be used to reinforce a client’s corporate identity. This can be done in a literal way, by replicating a company logo, or it can be as subtle as establishing, on the larger canvas of a building façade, a recognized, brand-associated pattern.
The potential for panel finish customization was fully explored for the Grenville Mutual Insurance building in Kemptville, Ontario. Architect Gerry Shoalts (Shoalts and Zaback Architects Ltd.) wanted to create elevations that would reflect the site’s natural setting. Therefore, in addition to a façade featuring handset natural stone, the building team created a customized embossed ‘forest’ pattern.
The form-liner pattern was developed from a still image, repeated to achieve a similar appearance. The customized panels are on the building’s exterior as well as being carried into the office’s open-air courtyard. To add depth and shading, building panels for the 1672-m2 (18,000-sf) office were treated with natural multi-depth paint tones. The tilt-up concrete construction technique also complements the building’s traditional metal-sloped roof and chimney.
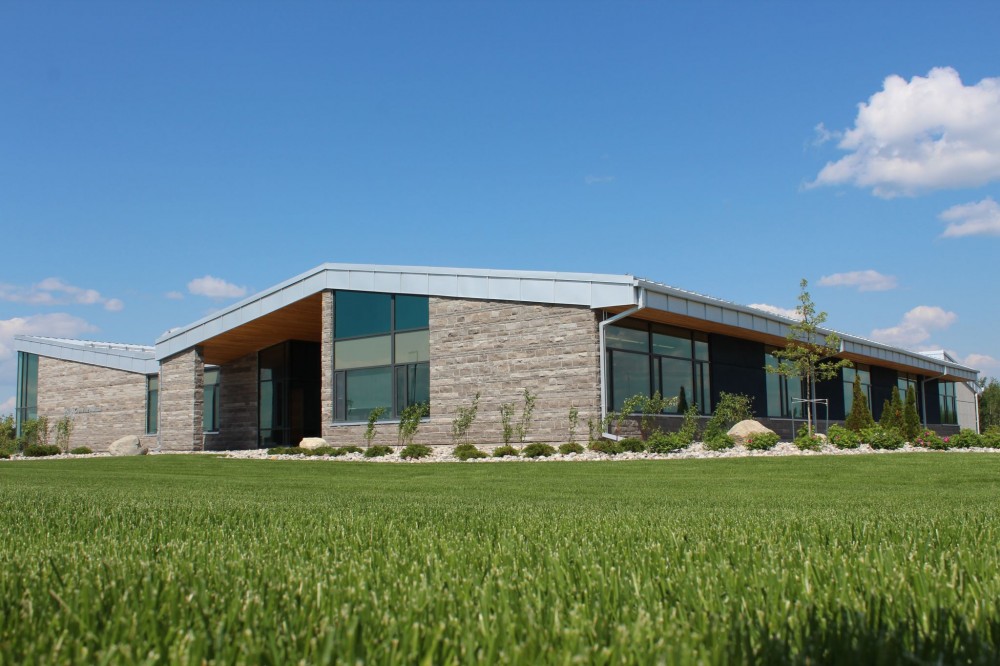

Beyond traditional aesthetics
Whether embossed, embedded, layered, or attached, the creativity of form manipulation with tilt-up is expressed in an ever-broadening palette of opportunity for designer and contractor. Visual enhancements like grooves and reveal patterns rank high on the list of popular techniques for using tilt-up construction to serve the architectural goals of a project. Metals and natural materials such as stone often enhance the building aesthetic, introducing warmth and smaller scale with the added benefit of reduced maintenance over painted features.
Tilt-up panels also serve as the canvas for graphic expression through the use of exterior insulation finish systems (EIFS). A concrete panel establishes a monolithic structural surface for the attachment of these systems in various ways. Projects featured in the TCA’s award program express banding, layering, and highlighting created by these applied techniques to further define the building’s look.
This year’s TCA Achievement Award winners show efficient, time-saving building methods like tilt-up construction support, not hinder, great architecture. The delivery method offers the benefit of cost-effectiveness combined with material plasticity, so designers will continue to push the envelope in using it to explore the making of forms.
Notes
1 For more on this line of thinking, see the cover story from the June 2013 issue of The Construction Specifier—“Tilt-up: An Opportunity for the Resurgence of Craft,” by Mitch Bloomquist. (back to top)
Kristin Dispenza, CSI, is an architectural/engineering/construction editorial specialist with Constructive Communication. She has more than 20 years of writing and editorial experience with industry trade publications. Dispenza holds a bachelor’s of science degree from the Ohio State University College of Engineering/School of Architecture. She can be reached at kdispenza@constructivecommunication.com.
I didn’t know the tilt-up panels could be used to improve aesthetics. That’s kind of fascinating. It also sounds like a great way to get a unique finish.