Understanding thermal efficiency
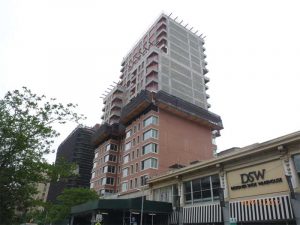
Every material used in construction can resist the transfer of energy—this is its R-value. The reciprocal of a material’s R-value is its U-factor, or its tendency to transfer energy. R-values of many common building materials can be found in ASHRAE 90.1 in, for instance, Table A9.4.3-1, “R-values for Building Materials.” Manufacturers are also good sources for R-values of specific products. However, it is always advisable to verify such claims by a review of test data supporting the published values.
The prescriptive requirements of the code for, say, opaque wall assemblies can be met in one of two ways. The first is the “R-value method,” where an exterior wall is deemed in conformance if insulation of a certain R-value is provided as indicated in IECC, Table C402.1.3, “Opaque Thermal Envelope Insulation Component, Minimum Requirements, R-Value Method.” This is the most straightforward path to compliance, but is not always possible or the most practical.
A second path to compliance is the “whole assembly U-factor” method. In this case, the thermal efficiency of the entire wall assembly is calculated to determine the overall U-factor, and that amount is, in turn, compared to the maximum values in IECC, Table C402.1.4, “Opaque Thermal Envelope Assembly, Maximum Requirements, U-Factor Method.” This is a more complicated path to compliance, as the thermal values used for the various wall components are strictly dictated by Normative Appendix A, “Rated R-Value of Insulation and Assembly U-Factor, C-Factor, and F-Factor Determinations,” of ASHRAE 90.1. However, this method often offers an advantage to designers when placement of the amount of insulation dictated by the prescriptive requirements of the code proves impractical.
The path to compliance
As discussed, the code provides prescriptive values for the building enclosure, minimum requirements components like roofs, walls, and fenestration must meet. Whether or not one can avail of those values depends on the amount of glass on the building. Section C402.4.1, “Fenestration (Prescriptive), Maximum area,” of IECC states (with some exceptions):
The vertical fenestration area (not including opaque doors and opaque spandrel panels) shall not be greater than 30 percent of the gross above grade wall area.
With the use of prescriptive values being the easiest path to code compliance, why would the International Code Council (ICC) restrict its use based on the amount of glass on a building façade?
As it turns out, most of the inefficiency that is experienced at the building enclosure is through the fenestration. The second law of thermodynamics states that energy flows from hot to cold, so, in the summer, windows, being the most thermally inefficient portion of the enclosure, will warm the cool, conditioned air of the interior, requiring more energy to achieve thermal comfort. This happens in two essential ways: through conduction and convection (the transfer of energy through and across the assembly), and via solar radiation. Glazed assemblies are made more energy efficient by reducing the amount of energy it can transfer by decreasing its overall U-factor and solar heat gain coefficient (SHGC). These performance improvements are achieved in a variety of ways, including thermal separations at metal frames, internal frame components such as warm spacers, glass coatings, and inert gases such as argon and krypton between the panes of insulating glazing units (IGUs).
Yet, fenestration is still a weak point in the quest for thermal efficiency and code compliance. There is documentation supporting the notion that limits to the amount of exterior glass in a room does not necessarily reduce the user’s well-being. The U.S. Green Building Council (USGBC), for instance, has stated, “window areas below 0.6 m (2.6 ft)” do not contribute to daylighting of interior spaces and [should] be excluded” (Get more information from the U.S. Green Building Council’s New Construction and Major Renovation Reference Guide.).
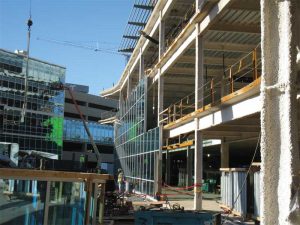
The code recognizes that glazed assemblies are inefficient when compared to the opaque portions of the building enclosure, and more glazing is often unnecessary to achieve a desired indoor environment. As a result, both IECC and ASHRAE 90.1 attempt to encourage the reduction of glazing by restricting the use of prescriptive values and requirements within the code. While this requirement is not new, large glass towers have not exactly disappeared from the landscape. So how do these buildings establish a path to compliance when they have more than the required percentage of vertical fenestration?
In such cases, compliance lies in the ability to ‘model’ the building to show it performs as efficiently as a building with the requisite percentage of glass (the ‘budget building’). This can be accomplished in several ways, but most often means following the requirements of Normative Appendix C, “Methodology for Building Envelope Trade-Off Option,” as further defined by Section 5.6, “Building Envelope Trade-Off Option,” of ASHRAE 90.1. This option enables designers to make up for inefficiencies in certain elements of the building enclosure (in this case, a preponderance of glass) by trading off with systems performing in excess of the code requirements, such as opaque wall assemblies, roofing, or lighting. Depending on the amount of vertical fenestration, such trade-offs could tax the abilities of these other systems to compensate in ways that fit the design requirements and do not become cost prohibitive.
The ramifications of having too much glass, and then having to employ alternative paths to code compliance such as the “Building Envelope Trade-Off Option,” do not end there. Starting in 2013, ASHRAE 90.1 included the following statement in Normative Appendix C:
C1.2.6 For Uninsulated Assemblies. All uninsulated assemblies (e.g., projecting balconies, perimeter edges of intermediate floor slabs, concrete floor beams over parking garages, roof parapet) shall be separately modeled.
Less than 30 words, and yet, it has significant implications in how the façade of a building is assessed for thermal performance. Under the prescriptive requirements, an opaque wall assembly’s ability to resist thermal transfer (its R-value or U-factor) has traditionally been established by an analysis of its ‘clear wall value.’ In other words, by assessing “a portion of the wall containing only insulation and a minimum of necessary framing materials at a clear section with no windows, corner columns, architectural details, or interfaces with roofs, foundations, or other walls.” The result is an optimal assembly presenting the best possible performance of that wall for energy.
However, this is not reality. What an analysis of this portion of the wall fails to consider are the host of conditions in a façade that can lead to thermal transfer: the linear and point transmittances. Examples include:
- parapets;
- uninsulated slab edges;
- window heads, sills, and jambs; and
- façade cladding anchors.
When these transmittances are accounted for, the actual insulative value of a wall can be reduced by as much as 60 to 70 percent (For more information, read British Columbia Hydro’s Thermal Envelope Bridging Guide, Version 1.1, 2016.).
By including C1.2.6 in Normative Appendix C, ASHRAE’s message is clear: reduce the amount of glass on buildings or switch to high-efficiency detailing to address all thermal inefficiencies on the building enclosure.
It should be noted the use of high-efficiency detailing to eliminate thermal transfer at façade transmittances can represent a net cost savings to owners. By establishing a more efficient building enclosure during design, the size of mechanical systems and subsequent utility costs could be significantly reduced.