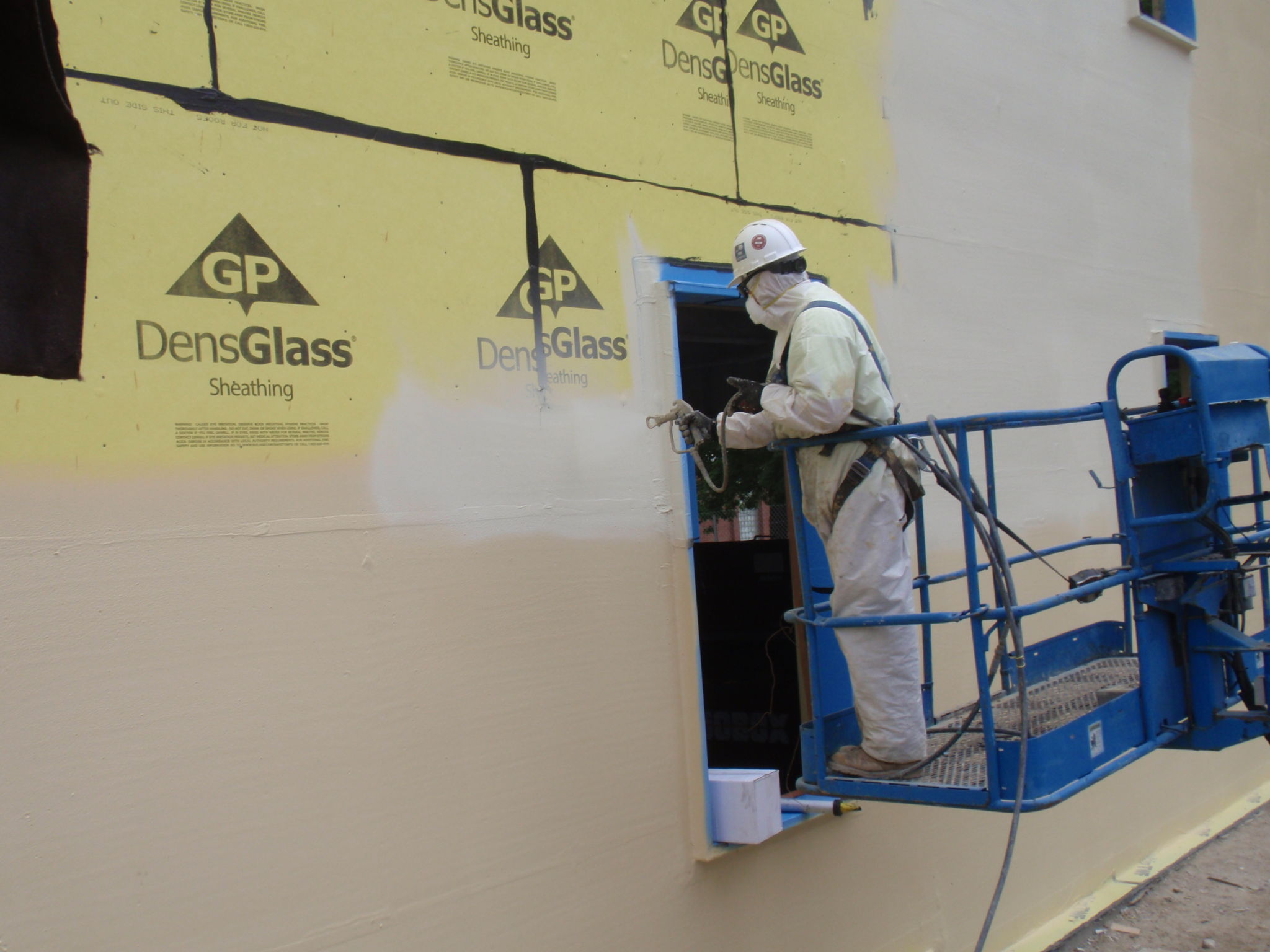
by Scott Wolff, CSI, CDT, and Todd C. Skopic, CSI, CDT, LEED AP
The fluid-applied air barrier (FAAB) concept was originally a Canadian-developed technology from more than 40 years ago. Back in the early 1970s, the genesis was an adhesive combining air- and vapor-retarding characteristics—eventually, this material would find its way into building codes.
The earliest FAABs were heavy-bodied products with predictably thick wet film/dry film applications. As it turns out, thicker membranes would have many advantages. Industry organizations such as ARCOM’s MasterSpec created the “fluid-applied membrane air barriers’ specification for these membranes with “not less than 40 mils dry film thickness (DFT),” that is,
1 mm (0.04 in.).
It is important to acknowledge all other ‘sides’ of the building enclosure ‘box’ similarly employ thicker membranes in the prevention of water and air infiltration. Foundations are commonly covered with 60-mil (i.e. 1.5-mm [0.06-in.]) styrene butadiene styrene (SBS) self-adhered sheet waterproofing (e.g. rubberized asphalt) or single or two-ply fluid-applied waterproofing. These are commonly in the 60 to 120 mils (i.e. 3-mm [0.12-in.]) DFT range. Roofing membranes, such as single-ply membranes, are also applied in larger thicknesses—typically in the 60 to 80-mil (i.e. 2-mm [0.08-in.]) DFT range or higher.
Enter the ‘thin-film’ era of air barriers. This phenomenon began approximately 15 years ago and was born out of the exterior insulation and finish systems (EIFS) industry. EIFS manufacturers provide single-sourced water-resistive barrier (WRB), insulation, and finished exterior wall assemblies. All may be well and good, but within the past 10 years, MasterSpec eventually addressed this new class of FAAB with a new specification titled “Air Barrier Coatings.”
In this specification, DFT values are listed at 14 and 17 mils (i.e. 0.35 and 0.43 mm [0.014 and 0.017 in.]) for vapor-retarding and vapor-permeable ‘coatings,’ respectively. Absent in the air barrier coatings specification language for DFT are the words “not less than.” Essentially, these ‘coatings’ can be even less than 14 mils.
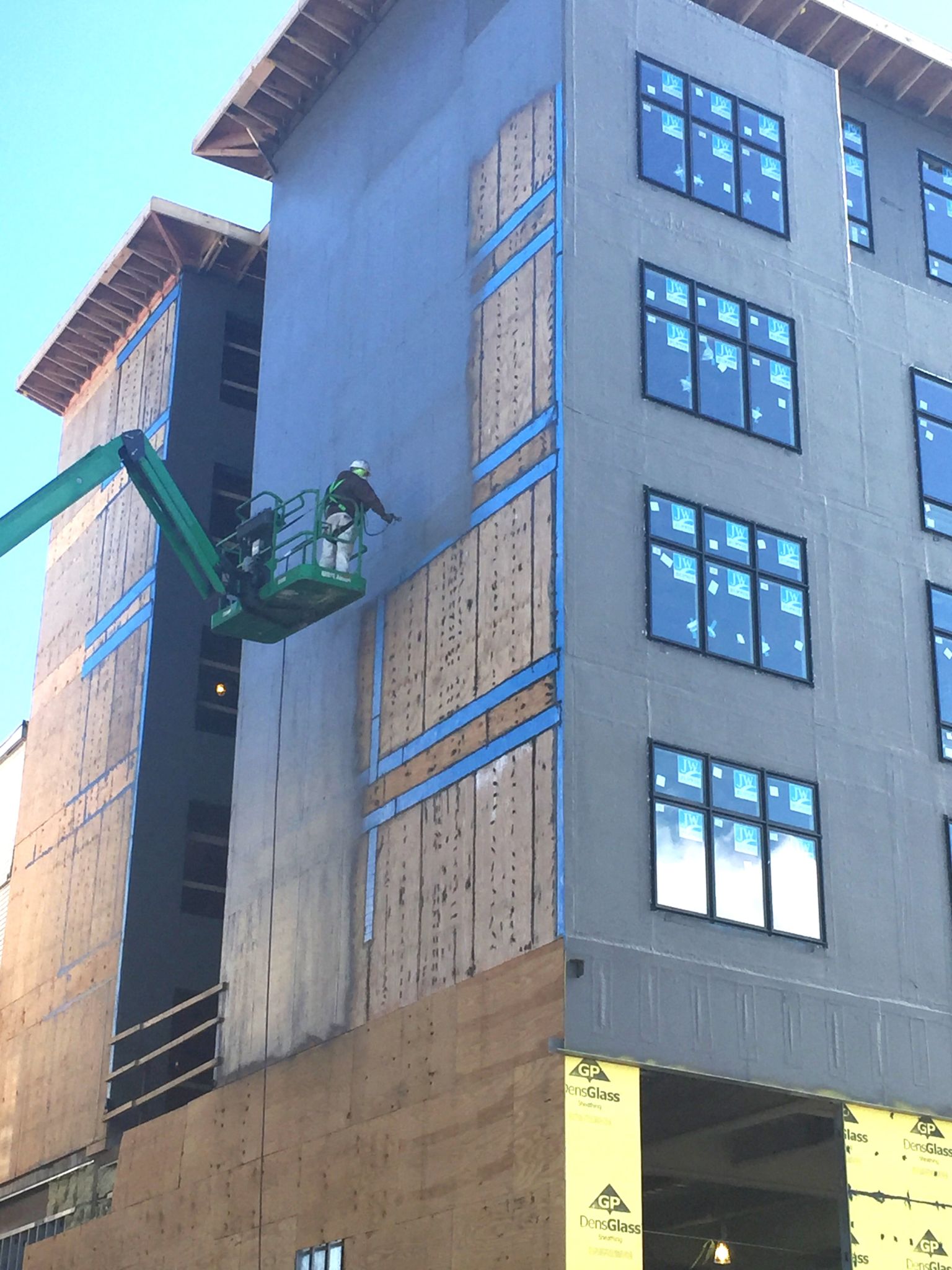
In 2015, MasterSpec decided to combine the two specifications into one. Gone is the “Air Barrier Coatings” title while the “Fluid-applied Membrane Air Barriers” remains. This new version contains three sections in Part 2−Products and Part 3−Execution for different thicknesses:
- low-build;
- medium-build; and
- high-build.
MasterSpec has provided a demarcation line for a minimum of 35 mils (i.e. 0.9 mm [0.035 in.]) DFT for the high-build FAAB. Conversely, low-build FAABs are held to not less than 6 mils (i.e. 0.15 mm [0.006 in.) DFT.
Differences in thickness
The commonalities of all FAAB types include meeting respective industry requirements for maximum air water vapor permeance based on:
- ASTM E2178, Standard Test Method for Air Permeance of Building Materials;
- ASTM E2357, Standard Test Method for Determining Air Leakage of Air Barrier Assemblies; and
- ASTM E96, Standard Test Methods for Water Vapor Transmission of Materials.
This is, however, where much of the similarities end. Pointing to the obvious fact buildings move brings this discussion to performance and long-term membrane durability. The disparity begins with the singular performance aspect MasterSpec does state—ultimate elongation (ASTM D412, Standard Test Methods for Vulcanized Rubber and Thermoplastic Elastomers−Tension). Only the high-build vapor-retarding FAABs are currently held to a minimum of 500 percent ultimate elongation. Both medium- and low-build FAABs are held to a minimum of 350 percent ultimate elongation—essentially, this shows thin-film FAAB are held to a lower performance standard.
The discussion points that must be considered by the specifier for what is lacking in thin-film membranes are summed up in the paragraphs that follow.