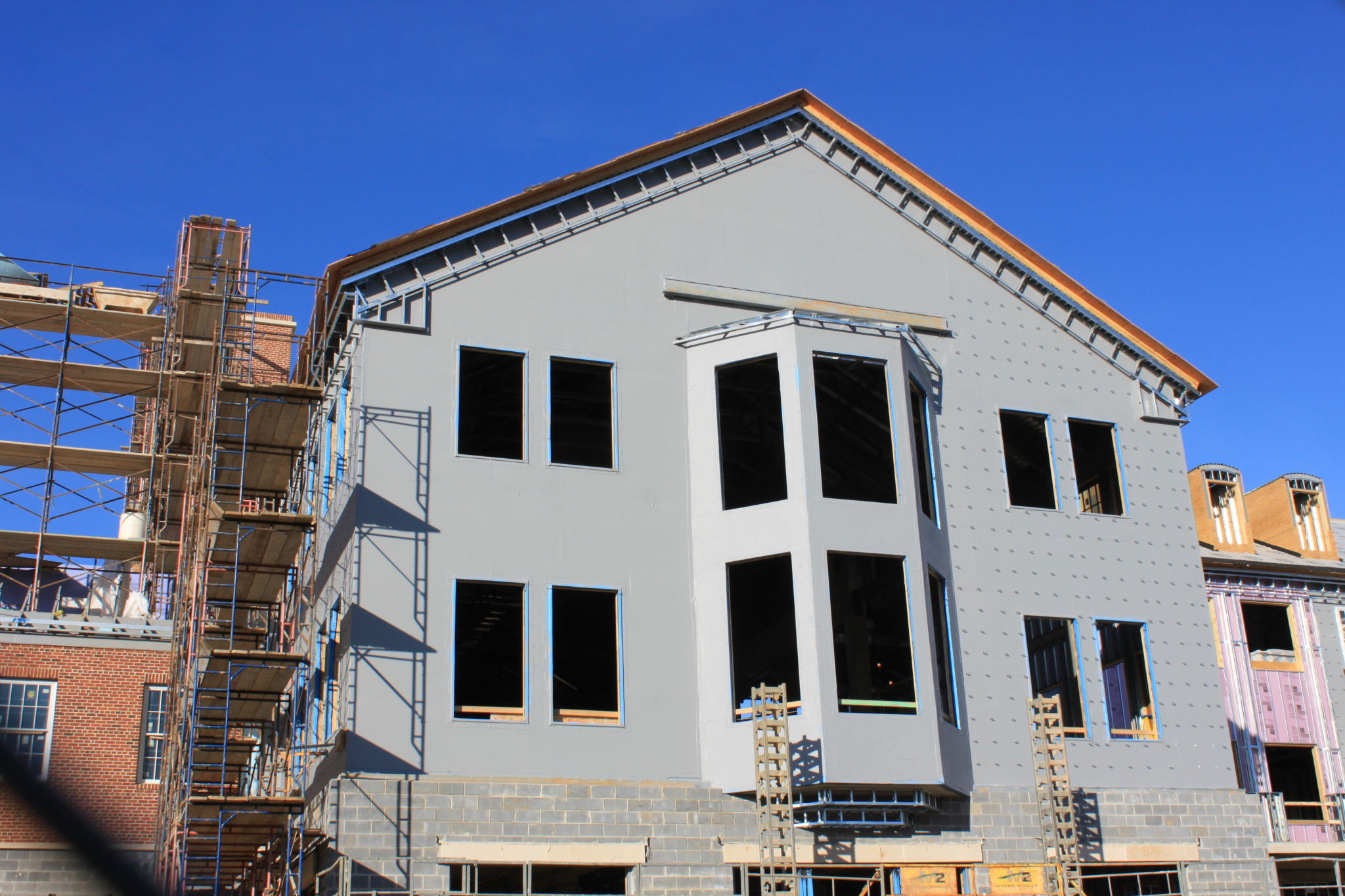
Long-term durability expectations
To provide an analogy, use of thick-film air barrier membranes is akin to using coal-tar pitch roofing. By sheer virtue of ‘having more membrane,’ it takes longer for the membrane to ‘wear.’ Additionally, as this article discusses, thin-film membranes’ application are inherently more difficult to control (to achieve correct wet/dry film thickness). Thick-film air barriers are high-bodied membranes typically needing only one application instead of multiple ones.
How long the company has been engaged in FAAB manufacturing
This question is not meant to favor a longstanding air barrier manufacturer over a newer one; rather, it merely establishes a ‘company regularly engaged in the manufacture of’ these types of membranes with many successful years. Of course, in any area of building science, newer technologies are not to be ignored, and should be heralded. It should be noted, however, it is not unheard of some companies rushing a new product to market before proper and thorough field testing.
Crack-bridging performance properties
A standard commonly used by thick-film manufacturers is ASTM C836, Standard Specification for High-solids-content, Cold-liquid-applied Elastomeric Waterproofing Membrane for Use with Separate Wearing Course. Some thin-film manufacturers may state “crack-bridging,” but neglect to reference the specific standard to back up the claim. (Thicker membranes have more body and mass to span the cracks.)
Tensile and elongation properties
These performance properties may be lower in thinner-film FAABs. Design professionals should ensure the numbers are being reported.
Single-source opportunities
Are all accessories provided by the primary air barrier manufacturer? Some thin-film providers do not manufacture and provide a complete accessory compliment such as through-wall flashings, transition membranes, termination sealants, and primers. Compatibility of accessories by other manufacturers then becomes another question.
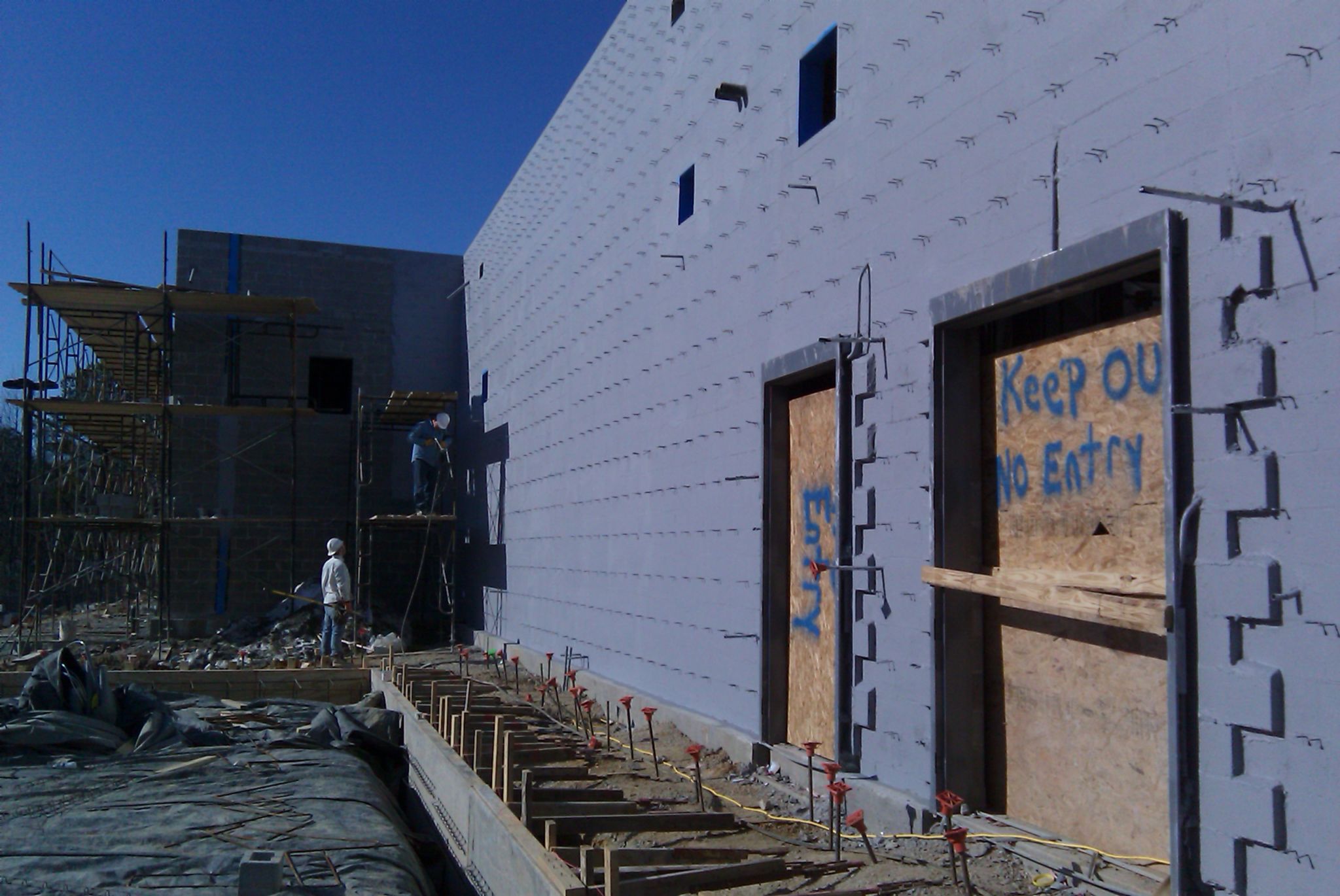
Air barrier warranties apply to the primary membrane and accessory items. Warranties are
solely for defective material (e.g. material-only warranty). If a contractor cherry-picks the membrane and various accessories from multiple companies, each company will provide warranties for only those products each has provided. Single-source helps ensure compatibility.
In projects where exterior insulation and finish systems (EIFS) are employed, to acquire the ‘system’ warranty, the EIFS manufacturer often requires its thin-film air barrier be installed beneath.
Marked coverage rate disparity based on substrates
Thin-film coverage rates can be as much as five to six times that of thick-film air barrier per gallon of installed product. Costs become an overriding deciding factor where the bottom line is the only thing that matters. However, the first cost of an FAAB is not as important as the lifecycle cost for the building’s entirety.
Back-rolling
Back-rolling adds another layer of installation cost for thin-film products. Roller-only formulations
require more time and labor to install.
‘Additional material’ required
For thin-film products, added material is commonly required, based on substrate porosity, as mentioned in the manufacturer’s literature. [Some thick-film manufacturers recommend initial higher-build applications of their membranes when applied to “rough” surfaces. The phrase “additional material required” is language specific to thin-film manufacturer’s literature. To clarify, “additional material” is required in the event the initial application has failed to achieve the specified wet film thickness (or achieve ‘hide,’ as yet other thin-film manufacturer’s literature would dictate)]. Who is policing the installer when higher-porosity substrates (such as exterior gypsum sheathing, precast concrete, concrete masonry units [CMUs]) mandate more material? General contractors might be enticed at the prospect of a lower-cost air barrier, but are they really getting what was specified? Are all the transitional conditions getting proper detailing with transition membranes and through-wall flashing?
It is an established fact the thinner a membrane is, the more difficult it is to achieve a complete and uninterrupted film during application. This is based on the marked variations in substrate porosity of exterior gypsum sheathing, concrete, concrete masonry units, etc.
Testing specifics
Thin-film FAAB performance standards are tested at X mils. However, the specifications may require Y thickness, which is often two to three times that ‘X.’ This leads to the question of what those performance characteristics are at Y thickness.