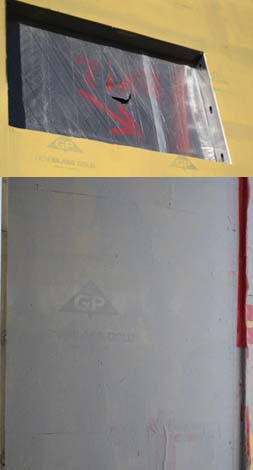
Who’s minding the store?
In many cases, contractors are solely left to decide if enough material is applied to the correct wet film/dry film thickness. The language in some thin-film manufacturer’s data states many gypsum sheathing products require additional material to achieve hide and ensure pinhole-free coating to meet the spec. When the sheathing manufacturer’s logo can easily be seen (Figure 1), it is a telling sign desired mil thickness was not achieved.
Not being discussed in great detail is the increased difficulty (and needed vigilance) of achieving a uniform, unbroken membrane over substrates—especially in the case of CMU backup walls exhibiting higher surface porosity. Thin-film coatings typically require several coats over CMU or what is called out as ‘block filler.’ Each coat is required to be back-rolled and must be fully cured before the second coat is applied. This equates to additional material, labor, time, and cost to finish the installation (presuming the specification is being followed correctly).
Vapor-permeable FAAB specification
Some FAAB specifications contain both thick-and thin-film membranes. In a number of these, thickness is required to be “not less than 40 mils dry film thickness.” Where a thin-film product has been tested at a DFT of 15 mils (i.e. 0.4 mm [0.015 in.]) and a vapor permeance of 10 perms, installing that same membrane at the project specification (requirement) of not less than 40 mils will yield wildly different permeance results. In the event this thin-film membrane were to comply with the 40-mil minimum DFT, it would result in a more than doubling the thickness and a reduction of its water vapor permeance. As a result, the drying potential
of the wall assembly may come into question.
The minimum performance and physical properties discussed herein are based on available industry-leading specifications such as MasterSpec. As noted, these are minimum standards by which all FAAB should be based. Physical performance criterion such as tensile strength and crack bridging—not listed in MasterSpec—hold even more consideration for long-term envelope performance and durability.
Air barrier technical data and specifications should reference these performance capabilities as well as include their accompanying standard, such as:
- ASTM D412;
- ASTM C836; and
- ASTM C1305, Standard Test Method for Crack Bridging Ability of Liquid-applied Waterproofing Membrane.
Case study
On a recent project in New England, a thick-film FAAB was specified, submitted, and approved. Shortly thereafter, the general contractor was persuaded to accept a so-called ‘value-engineered’ alternative thin-film FAAB reportedly to “save $0.45 per square foot.” In the mockup in Figure 2, the thin-film FAAB application to CMU (at left) is shown to bear discontinuities in the form of breaches in the membrane exposing the substrate underneath. The thick-film FAAB is shown at right on the same mockup.
The back-up wall is CMU. The thin-film manufacturer was going to require a substrate smooth enough so the product could be installed at its recommended thickness without breaches. To get this required smooth surface on the CMU, the mason required an additional $1.45/sf in surface prep. The presumed cost savings would not only be lost by this additional cost, but to use the thin-film it would also cost the owner an additional $1/sf. This project was approximately 3700 m2 (400,000 sf), so to use the thin-film material would have actually cost the owner an additional $400,000.
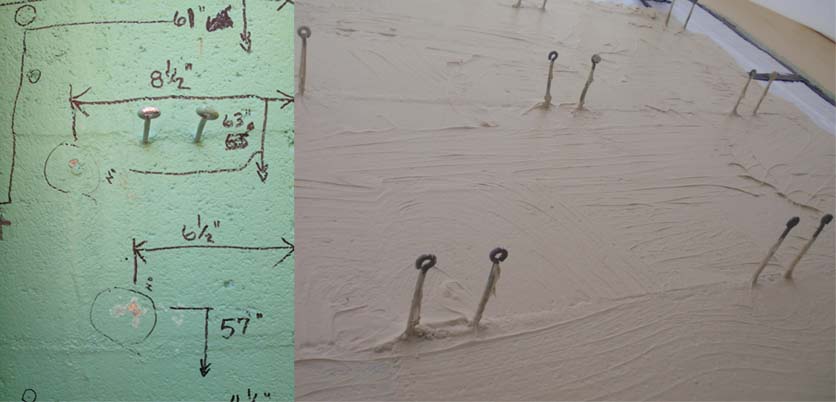
Thick-bodied thick-film air barriers are typically applied in a single application over substrates with varying porosity without the need for an additional layer. One argument of thin-film air barrier manufacturers is that substrate panel edges and transitional areas are the only areas in need of reinforcement (via transition membranes, etc.).
However, one only need to think about racking forces acting in the x and y axis of an exterior wall. Z-axis movement is also noted due to positive/negative wind and air pressure forces. Gypsum panels have been known to fracture within the field areas, not always at their edges. It is for these and other reasons thicker membranes, such as those used on foundations and roofs, should be used to maintain the same robustness on above-grade wall assemblies.