Tilt wall basics
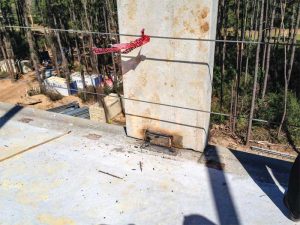
In its most common application, a tilt wall project begins with jobsite and subgrade preparation, installation of underslab utilities, and construction of interior and perimeter footings. On completion of this phase, construction proceeds with the placement and finishing of the concrete slab-on-grade. While other methods prefer to delay the slab placement until the building is enclosed, today’s technology allows contractors to achieve the required floor slab flatness and levelness suitable for high-bay racked storage in an open-air environment. The slab-on-grade now becomes the work platform for the construction of the tilt wall panels, with carpenters assembling formwork (typically lumber, but sometimes aluminum) to the height and width of individual panels. The formwork acts like a mold for the concrete panels, forming the top and bottom edges of the wall panels as well as acting as dividers between adjacent panels. The exact shape, size, and detail of each panel is formed, including openings for doorways and windows as well as cast-in architectural features such as reveals and recesses. Next, ironworkers place and tie the steel grid of reinforcing bars within the panel forms. Steel inserts for attachment of lifting devices and embedded plates for connecting panels to the footing, roof system, and each other are placed at precise locations within the panels and tied to the mats of reinforcing bars. The slab beneath the forms is cleaned of leftover debris and standing water, and then finishers place concrete into the forms to create the panels. Now comes the point where tilt wall construction gets its name. Once the concrete panels have cured, the top and bottom forms are stripped and pipe braces are attached to the interior face of the panels. The erection crew then connects the first panel to a large crane with cables hooked into the inserts. The size of the crane depends on the height and weight of the concrete panels, but its maximum capacity is two- to three-times the weight of the largest panel. For example, a 300-ton crane for 45,359-kg (100,000 lb) panels. The crane lifts, or ‘tilts up,’ the panel from its horizontal orientation on the slab into a vertical position above the footings. Workers help guide the concrete panel into position and the crane sets it into place. The pipe braces, previously attached to the panel, are anchored to the floor slab and used to plumb the panel into its final position. The cables are then disconnected from the panel. The crew moves to the next panel and repeats this process, typically allowing a 19-mm (¾-in.) wide joint between panels. The whole sequence takes approximately 20 to 30 minutes per panel, allowing crews to erect several hundred linear feet of wall in a single eight-hour day.
Short history of stacking panels
Lacking a definitively researched history, the stacking of tilt wall panels is anecdotal and situational. Its beginnings appear to be driven mostly by limited technology and very little aesthetic need or desire. The authors’ firms were early experimenters in this method, and not the only ones. Some early applications of stacked tilt wall panels can be found in southwest Ohio dating back to the mid-1980s. Driven by limited crane capacities (and therefore limitations on panel height and weight), nearly a dozen four-story office buildings were constructed using a loadbearing one-story panel vertically stacked over a loadbearing three-story panel. While lacking the architectural sophistication of today’s tilt wall offices, these projects provided an early proof of concept for stacking loadbearing panels vertically.
Additional examples of stacked tilt wall construction appeared in the 1990s from Ottawa, Ontario, in the north to Florida in the south. In Ottawa, a ‘house-of-cards’ approach was employed in the construction of four- and five-story buildings. The approach represented an improvement over the typical market expectation of a reinforced concrete frame with non-loadbearing precast cladding. The improved tilt wall building was constructed one story at a time, starting with the erection of single-story loadbearing tilt wall panels around the perimeter, then the forming and shoring of one-story of cast-in-place interior formwork, and finally the casting of one-story of columns and elevated slab. The process was then repeated either three or four additional times until the buildings reached their eventual height.
The authors have also reviewed drawings of stacked panels made in the late 1990s and used to construct a five-story office building in the Florida market. The approach was to stack two stories over three. The connection technology (still available) is a rebar dowel system requiring a male/female alignment of the two-story panel onto the three-story base panel with a grouted joint. This is a difficult and complex procedure, which is perhaps why the approach was not, until current times and techniques, more widespread.
The authors’ approach has been to rethink the five-story stacking as a ‘four-plus-one’ approach with a single panel, picked from its edge rather than the traditional backside, stacked on a four-story base panel. Their six-story stacking approach simply adds a floor, a ‘four- plus-two’ stack, to the baseline approach described below.
I would love to see, or provide if not currently available, similar articles showcasing the benefits of Structural and Architectural precast concrete as a means and method of construction, including information with regard to the installation of same.
What about the cost?
I agree with Mark. While the three of you embrace tilt up, Fabcon has successfully manufactured and installed panels taller than 70′ and currently are working in the multi-story distribution center market. Precast is load bearing, keeps the construction site cleaner and less crowded, erects quickly and is engineered to provide fire, water permeation, tornado, hurricane and earthquake protection. We have been in business for 49 years and operate out of 4 plant locations where we manufactured & installed over 16 million square feet of panels for 390 projects in 2018. Additionally, we have worked in 43 states, 4 provinces and the District of Columbia. Our panels provide functional aesthetics in any weather conditions and offer superior R-Values up to 28.2.