by Roger Overend
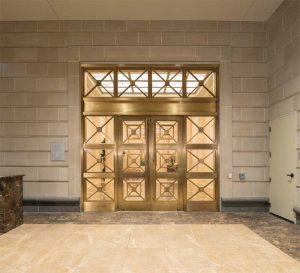
When designing building entryways, especially highly visible and heavily trafficked ones, architects and specifiers must successfully achieve precision, performance, and beauty (the triple threat) simultaneously.
While this is no simple task, products are available to meet all three of these requirements. One such product is the balanced door, a true ‘triple threat’ when it comes to creating striking, reliable, and fail-safe entryway systems.
Balanced door basics
The fulcrum is placed at one-third the width of the balanced door, so one-third of the door leaf recesses into the facility when the door is opened. This creates a more balanced pivot point for superior weight distribution. Even though a balanced door’s fulcrum is inset, it offers a similar opening space as conventional butt-, continuous-, and pivot-hinged doors.
The balanced door was invented in 1927 during an era of increasing popularity for skyscrapers and tight-knit construction. This new building trend inspired a need for a more high-profile door with the ability to resist both the external force of whipping winds through narrow streets and the internal stack pressures.
The first commercial balanced door was manufactured in 1932. What the manufacturer did not know then was that some of the balanced door systems that were created in the first few years of production would still be in use after the turn of the millennium, more than 80 years later. It is also likely they did not foresee the advantages (detailed below) balanced doors would offer to the design and functional challenges of today’s architects and specifiers.
Precision
The varied balanced hardware components set balanced doors apart from their conventional counterparts, and allow them to offer the pinnacle of precision. As a unified system, the many parts work together to facilitate nearly effortless door opening with reliable closing.
Components of precision
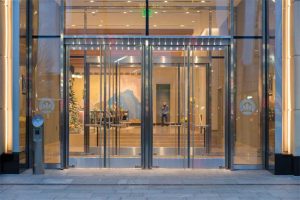
Photo courtesy Ellison Bronze
Starting from the top, a check and guide channel assembly can be found in the balanced door’s frame header. This component provides a conduit for the elliptical cycle of a balanced door, as well as the capacity to manage closing and latching speeds. These adjustments are achieved through a removable component of the guide channel assembly containing hydraulic fluid and two valves––one capable of adjusting initial closing speed and another for latching speed. These modifications can be made from the underside of the header without having to remove the component based on the facility’s needs, an important consideration to avoid removing large and heavy doors during maintenance. These can be accomplished by a facilities manager or a door installer.
The component working in conjunction with the check and guide assembly, and thereby serving as the door’s fulcrum, is the roller guide located in the door’s top rail. Typically, a door roller guide is cast in a manganese alloy housing for strength, as it absorbs the shock caused by the door’s opening and closing. Contained within the roller guide is a sealed roller bearing that moves back and forth in the underside of the guide channel to help facilitate the door’s elliptical path.
A top pivot bearing is set into the door top rail and contains a steel roller bearing inside. It is joined to the door’s top arm by a heavy-duty stainless steel pivot pin. When the pin engages into the pivot bearing, the top arm is able to support the lateral weight of the door’s top portion.
At the bottom of the door, the lower arm bears the weight, and is therefore thicker and heavier than the top arm. Both arms are welded to the heavy-duty tube shaft running the door’s length. In order to ensure long-term durability, it is important to select a door manufacturer who uses true penetration welds to attach the arms to the shaft, rather than a wedged fit.
The door’s bottom pivot component differs from the top in that its bearing is made of an engineered self-lubricating composite. This is done to minimize corrosion, as the bottom portion is susceptible to corrosives like salt from coastal environments, deicing chemicals, or cleaning solutions.