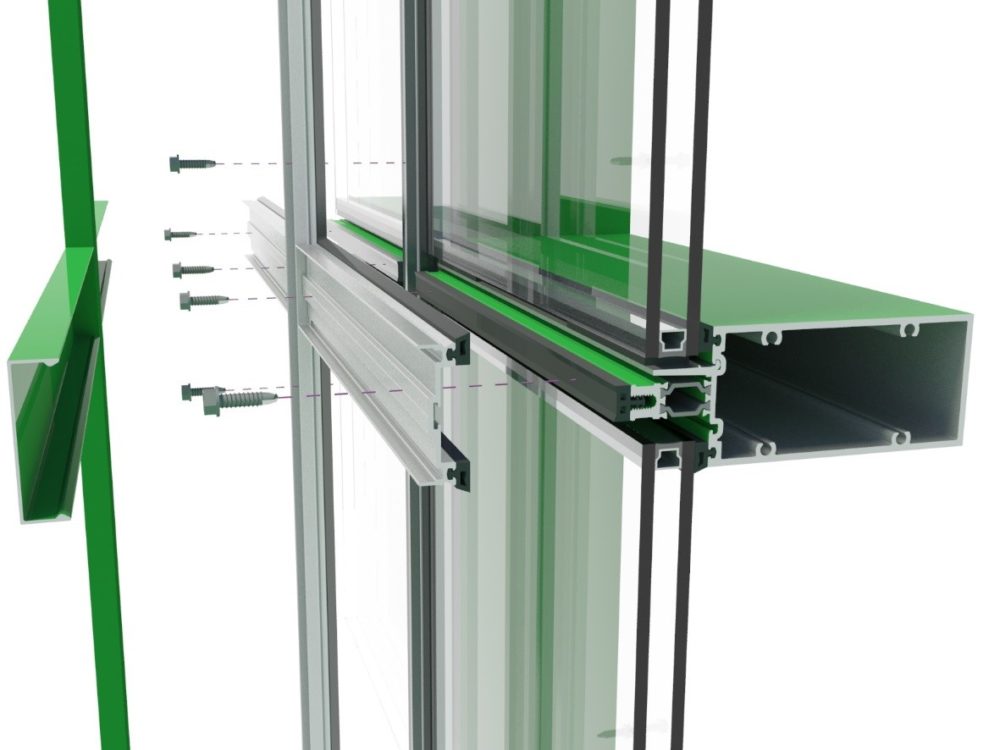
Image courtesy Tubelite
Understanding the curtain wall
There are two main categories of curtain walls. The first comprises the ‘stick-built’ systems, in which all structural components are assembled at the project jobsite. Stick-built systems are optimal for building façades with little repetition among components, where architectural designs are more complex and few economies of scale can be reached by factory production.
Unitized curtain walls, on the other hand, involve having glazed and aluminum components factory-assembled into panels and shipped to the construction site. Good for tall structures that use repeat components, this method is advantageous in that the controlled factory setting improves tolerances and installation to complete the enclosure faster.
The extruded aluminum members comprising the curtain wall frame can be two separate pieces (one for the building interior and one for the exterior) joined at pressure points, as is common in stick-built systems. They can also be a single extruded profile, which is more common for unitized systems. With either method, engineered systems to interrupt the thermal bridge created by the metal cross section must be installed. Two systems include the pour-and-debridge thermal barrier and polyamide thermal barrier strips.
The pour-and-debridge thermal barrier
For this method of thermal barrier, the aluminum profile is extruded with a channel designed to hold an insulating polymer. The channel is mechanically abraded to ensure adhesion of the polymer. A mechanical lock inside the thermal cavity locks the thermal barrier to the aluminum to provide superior structural strength for the composite. (Structural strength is extrusion- and cavity-specific; there is a great deal of data available depending on the extrusion type.) This allows the maximum separation of the aluminum required for lower U-factors while providing structural strength.
Polyurethane polymers are poured as liquid into the thermal barrier channel (or cavity) where they solidify into a structural, thermal component. Finally, the metal bridge (or floor) is removed from the bottom of the aluminum channel during the debridging operation. The result is a true, non-metal-to-metal structural aluminum and polymer composite. By eliminating the conductive pathway of the interior to the exterior of the curtain wall framing, the energy efficiency of the building is significantly improved.
Polyurethane polymers feature thermal conductivity 1300 times lower than aluminum and the thermal benefits occur within a very small amount of separation. The width and type of thermal barrier separation should be determined based on the given building’s energy use or reduction requirements. (Once the thermal performance is determined [usually by U-factor], the manufacturer will select the appropriate thermal barrier and the required separation to achieve the desired performance.)
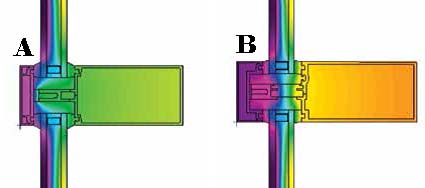
B: Curtain wall profile with polyurethane thermal barrier improves thermal efficiency by interrupting the flow of cold air through the extrusion. This also works to interrupt the flow of hot air in desert climates. Simulations conducted with – 18 C (0 F) outside and 21 C (70 F) inside temperatures.
Images courtesy Azon
A complete separation of the aluminum framing with an encapsulated polymer core maintains critical structural abilities to avoid strains and forces. Curtain walls —especially those used on tall buildings—are considered structural façade elements as part of a building’s wall system and must provide shear and tensile strength to sustain loads from high winds or even blasts or hurricanes. Thermal barriers must also accommodate stresses in the unitized curtain wall system that are created by thermal expansion and pressure differences. Fortunately, polyurethane polymers offer an exceptional amount of structural strength, particularly shear strength, allowing designers to maximize the span of glazing within the curtain wall framing. (Manufacturers of thermal barrier composites should be able to provide expected shear values, and structural testing, based on the type of extrusion selected.)
In addition to the introduction of a polymer to interrupt the thermal bridge, energy efficiencies can be gained by manipulating the shape of the aluminum extrusion itself. The latest developments in this area include wide cavity and dual cavity construction.
Wide cavity
Creating a wider cavity in the frame achieves a lower U-factor in most fenestration products. One can compare the U-factor of 2.44 W/m2K (0.43 Btu/[hr-F-ft]), achievable with a thermal isolator (Figure 1a) to that of a wider cavity, achieved by the use of a polyurethane thermal barrier (Figure 1b). In this example, the U-factor is improved to 2 W/m2K (0.35 Btu/[hr-F-ft]), and can be lowered to 1.7 W/m2K (0.3 Btu/[hr-F-ft]), assuming the use of performance glazing.