by David Stassi
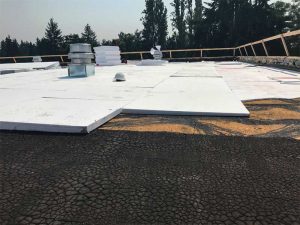
According to the 2015 International Building Code (IBC), roofs are required to have a design slope. Today, the design-build sector is increasingly specifying tapered expanded polystyrene (EPS) insulation solutions to comply with codes—many existing buildings that are being retrofitted require the slope to be altered to meet regulations—as well as save time and money on the roof.
While the busy summer construction season has wrapped up, fall is still ideal for roofing projects. The season’s crisp weather means construction crews do not have to toil under extreme heat. Spring and summer storms have cleared away, decreasing the likelihood of roofers encountering lightning, hail, and high winds. There is also time to prepare for the freeze-thaw, ice dams, and dampness winter brings. For specifiers, fall is the right time to ensure proper selection of insulation for low-slope and roofing recover projects, setting up crews for success on the building top. Certainly, the design-build sector is familiar with insulation’s energy-saving return on investment for commercial building owners and facility managers. The ideal commercial roof insulation will also result in material, labor, and time savings during construction—all benefits given the roofing industry’s current climate. As Roofing Contractor’s State of the Industry Report and Survey 2019 outlines, 68 percent of roofing contractors polled perceive “lack of qualified workers” as a challenge. The second biggest hurdle to the pace of overall construction is “increased building material costs” at 57 percent, given the tariffs imposed on steel and aluminum.
These industry-wide workforce and resource concerns are especially felt when building up slope. The 2015 IBC, section 1507.10.1, “Slope,” requires “Built-up roofs shall have a design slope of not less than one-fourth unit vertical in 12 units horizontal (two percent slope) for drainage, except for coal-tar built-up roofs that shall have a design slope of not less than one-eighth unit vertical in 12 units horizontal (one percent slope).” To create code-compliant positive slopes on flat or low-sloped roof assemblies for drainage purposes, building and design professionals often turn to insulation.
Typically, teams have to move and install multiple layers of insulation to create said slope, requiring considerable time and resources to achieve the desired build-up in the roof assembly. These insulations are limited to 100 mm (4 in.) in thickness. Conversely, EPS is manufactured in thicknesses of up to 1016 mm (40 in.), which allows EPS to cut various tapered configurations. EPS also offers custom crickets saddles and sumps to assure positive drainage. These customizable tapered EPS insulation solutions can deliver on material, labor, time, and overall cost savings for low-slope commercial roofing assemblies, while still affording long-term thermal performance.
Cost-savings in low-sloped and flat roof systems
Specifically, tapered options are cut from EPS and available with customizable thickness from 3 mm (1/8 in.) to 1016 mm. Manufacturers can fabricate the rigid foam insulation in order to meet a project’s exact dimensional requirements, including density. Since it is composed of 98 percent air, the tapered solution is also ultra-lightweight.
For more data on how tapered EPS’ physical and mechanical properties impact projects’ bottom lines, it is important to consider material, labor, and time savings, respectively.
Material savings
Compared with extruded polystyrene (XPS) and polyisocyanurate (ISO), EPS requires fewer layers of rigid foam insulation to get the job done. Since XPS and ISO are limited in thickness, many layers are needed to achieve higher R-value assemblies. Each layer costs additional labor and materials (such as adhesive) to install.
Using EPS assemblies, crews typically install a single layer or two of tapered rigid foam insulation versus having to install numerous sheets of relatively thin insulation to achieve the same slope and R-values as XPS and ISO assemblies.
Additionally, since EPS manufacturers create a custom design to meet job-specific needs, there is less product waste. Such resource savings is critical when one considers the rising costs of construction materials.
A great piece of work. Thanks for sharing a good article. Very helpful in understanding International Building codes and tapered roofing systems.
A great piece of work. Thanks for sharing a good article. Very helpful in understanding International Building codes and tapered roofing systems.