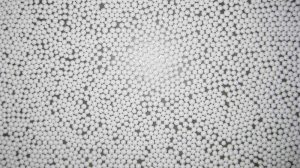
Labor savings
Along with the obstacle of more expensive building materials, roofers still have to contend with a shortage of skilled laborers, from “asking workers to do more work, struggling to meet deadlines, increasing costs for new work, and having to reject new projects,” the National Roofing Contractors Association (NRCA) reports. Fortunately, during the aforementioned tapered EPS installation process, workers do not have to navigate complicated filler panel systems. While XPS and ISO require complex stack and fill techniques, teams utilizing EPS have pre-cut blocks that already account for roof crickets, saddles, valleys, and ridges, along with all types of drainage systems and layouts. In application, crews can easily and precisely handle and install these customized, lightweight tapered EPS pieces into roofing assemblies.
Time savings
The tapered EPS approach to building up a slope can significantly reduce the number of person-hours onsite. In total, factory-cut, custom-built blocks call for less material handling, do not need to be cut prior to installation, and can be installed faster than their XPS and ISO counterparts due to their ultra-lightweight nature. All of these factors help accelerate tapered roofing jobs’ timelines.
As detailed in Figure 1, specifying tapered EPS insulation can result in material and labor savings compared to other tapered insulation options. Some manufacturers estimate contractors can see up to 30 percent overall cost reduction. By utilizing more cost-effective approaches to rigid foam insulation, professionals can address common industry concerns and stay in the black.
Understanding EPS rigid foam insulation and thermal performance
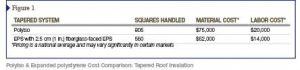
To fully understand how EPS compares to XPS and ISO, it is important to know how these common types of rigid foam insulation are made.
EPS rigid foam insulation consists of a uniform, closed cellular structure that can meet or exceed the requirements of ASTM C578, Standard Specification for Rigid, Cellular Polystyrene Thermal Insulation. As ASTM C578 says, “This specification covers the types, physical properties, and dimensions of cellular polystyrene boards with or without facings or coatings made by molding (EPS) or extrusion (XPS) of expandable polystyrene.”
Block molding plants make EPS by producing polystyrene beads that are the size of sugar granules. Manufacturers bring the beads into contact with steam, and the beads’ inner pre-foaming agent begins to boil, expanding them to 40 to 50 times their original size. After a maturing period, the beads settle into a mold, where they are exposed to steam again. During this process, the beads fully expand and fuse together to fill the specified mold cavity.
By comparison, the manufacturing process for XPS and ISO varies greatly from EPS. With these rigid foam insulations, manufacturers create a foam using a gas expansion/blowing agent. First, they introduce the gas into a liquid plastic, which forms a foam via numerous bubbles. The gas then gets trapped in the bubbles as the plastic hardens.
Since the gas’ R-values are greater than air’s R-value, XPS and ISO have higher initial resistance to heat flow than EPS. Like ISO, XPS uses blowing agents that are also fugitive. However, during the rigid foam insulations’ service life, air diffuses in, while blowing agents diffuse out of the cells. Known as thermal drift, this phenomenon can cause R-values of XPS and ISO to degrade over time.
Both ISO and XPS are subject to using a long-term thermal resistance (LTTR) value, the time-weighted average for five years. However, most roofs last longer than five years. The expected long-term R-value for XPS is 4.3 per inch, which is a similar R-value to Type IX EPS. For ISO, the value has been under scrutiny by the NRCA, with values expected less than the posted LTTR value.
Since EPS is composed of 98 percent air, the rigid foam insulation is safe from thermal drift. As the EPS Industry Alliance (EPS-IA) explains, “EPS is stable and does not experience any thermal drift and does not lose R-value over its life. In the long run, the thermal performance of EPS insulation is constant.” Third-party research backs this claim, showing EPS does not experience deterioration in R-value. The researchers tested EPS insulation samples from roofs of varying ages at 21 C (70 F) for thermal resistance, and found no change in R-values. This consistent thermal performance has led some EPS manufacturers to provide a long-term warranty of the rigid foam insulation’s full R-value.
A great piece of work. Thanks for sharing a good article. Very helpful in understanding International Building codes and tapered roofing systems.
A great piece of work. Thanks for sharing a good article. Very helpful in understanding International Building codes and tapered roofing systems.