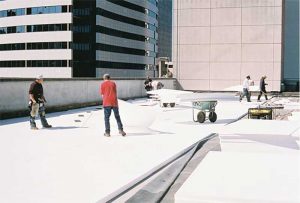
Application
Familiar with tapered EPS insulation’s long-term R-values, compressive strength, and customizable thickness, a California-based manufacturer chose to incorporate the rigid foam insulation in its roofing and waterproofing membrane for the Washington State Convention Center (WSCC). The Seattle landmark building’s roofing system had started to leak and fail due to weathering and age, and the manufacturer was brought in to replace the outdated assembly with one that would withstand the cold, wet Pacific Northwest climate.
The manufacturer required the convention center’s insulation have a compressive strength of 276 kPa (40 psi), which would be strong enough to be able to support a garden following the roof replacement. The manufacturer also specified 1 x 2-m (4 x 8-ft) tapered EPS insulation panels with thicknesses from 25 to 150 mm (1 to 6 in.) for ease of manageability. This allowed for a quick installation, and cut down on the amount of labor and construction time in Seattle’s tight labor market.
To address the leaking, the manufacturer chose tapered EPS panels that were custom-designed at a 3-mm (1/8-in.) slope to allow maximum drainage and prevent ponded water. In addition to promoting positive drainage, the manufacturer sought an insulation with resistance to moisture retention.
Water resistance
In a city where rain occurs for an average of 152 days per year, the manufacturing company needed to utilize construction techniques and product solutions adept at overcoming Seattle’s rainy weather. They addressed this problem by turning to EPS for its non-hygroscopic properties—the insulation has little or no tendency to absorb moisture due to its closed cell structure.
EPS does have some small interstitial spaces, but it expels water well. All insulations take up moisture, so the question becomes, ‘How well do they dry?’ While it takes XPS a long time to dry, EPS dries quickly and returns to posted R-values.
As illustrated in a study by third-party agency Energy Materials Testing Laboratories (EMTL), EPS does not absorb appreciable moisture in well-constructed roofing assemblies. EMTL simulated winter exposure conditions and found, “the same amount of moisture absorbed (an average of 0.2 percent by weight) has little or no effect on its compressive or flexural strength, and the EPS insulation retains between 95 and 97 percent of its thermal efficiency.”
EPS’ ability to block heat flow despite frequent rainfall made the product a natural fit for the Seattle roofing membrane.
Environmental benefits
Like moisture retention, energy efficiency and environmental concerns were intrinsic to the WSCC project. Naturally, the choice of insulation would have to align with the convention center’s environmental building practices.
EPS supports energy efficiency by creating a tighter building envelope. Less air leakage keeps the convention center cooler in the summer and warmer in the winter, lowering heating and cooling bills, and reducing the facility’s impact on the environment.
Moreover, this rigid foam insulation does not contain any ozone-depleting gases, may have recycled content, and is 100 percent recyclable if it is ever removed or replaced. By combining sustainable form with environmentally friendly functionality, “EPS plays a key role in a building’s ability to comply with ASHRAE 90.1–2001, Energy Standard for Buildings Except Low-Rise Residential Buildings, a benchmark requirement for most green building programs,” says EPS-IA.
With its environmental attributes contributing to long-term thermal performance, coupled with its ability to withstand moisture, tapered EPS is built to last on the rooftop of Seattle’s premier convention center.
Lasting the test of time
Autumn’s mild temperatures make it the ideal season to get to work on the roof, and positive slope and insulation are key components of many such projects. While considered a roofing construction best practice, a positive slope can be costly and material/labor intensive to create with stacks of thick rigid foam insulation. To face these challenges, which echo industry-wide commodity price and workforce issues, tried-and-tested products like customizable tapered EPS continue to hold the answer.
David Stassi is field technical support manager at Insulfoam, a manufacturer of expanded polystyrene (EPS) insulation products. A graduate of Colorado State University, prior to joining Insulfoam, Stassi worked as a field sales representative for OMG Roofing Products. Stassi can be reached via e-mail at david.stassi@insulfoam.com.
A great piece of work. Thanks for sharing a good article. Very helpful in understanding International Building codes and tapered roofing systems.
A great piece of work. Thanks for sharing a good article. Very helpful in understanding International Building codes and tapered roofing systems.